Cylindrical pins are common mechanical connectors widely used in various fields such as mechanical equipment, automotive, aerospace, and electronic devices. Their primary function is to position, secure, or connect two or more components, ensuring precise relative positioning during assembly and use. This article will provide a detailed introduction to the usage scenarios and methods of cylindrical pins, helping readers better understand and apply this important mechanical component.
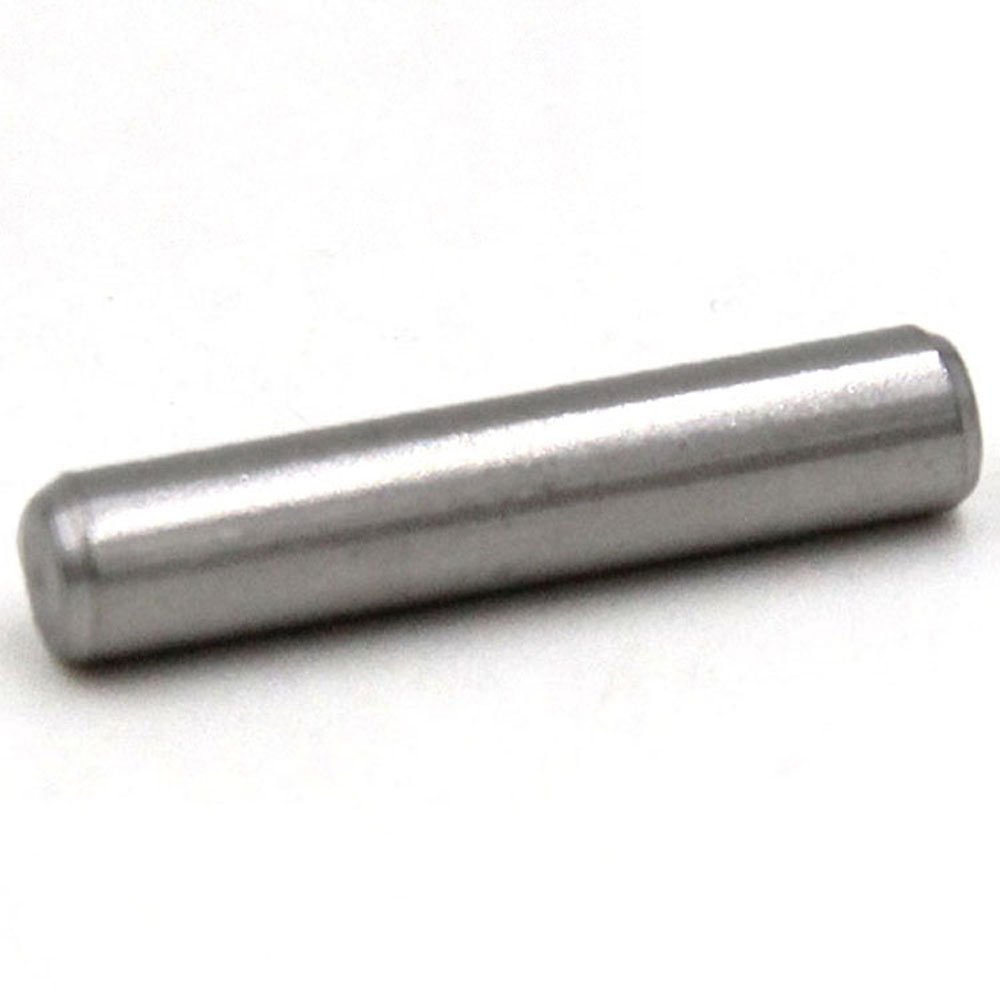
Basic Concepts of Cylindrical Pins
Cylindrical pins are cylindrical metal pins typically made from materials such as steel, stainless steel, copper, or aluminum. Their diameter and length can be customized according to specific requirements, and common surface treatments include zinc plating, blackening, and chrome plating to enhance corrosion resistance and wear resistance. The ends of cylindrical pins can be flat, chamfered, or threaded to accommodate different installation needs.
Usage Scenarios of Cylindrical Pins
1. Positioning and Securing in Mechanical Equipment
In mechanical equipment, cylindrical pins are often used to position and secure two or more components. For example, in machine tools, stamping dies, and fixtures, cylindrical pins ensure that components maintain precise relative positions during assembly, preventing displacement caused by vibration or external forces. The high precision and stability of cylindrical pins make them indispensable connectors in mechanical equipment.
2. Applications in Automotive Manufacturing
In automotive manufacturing, cylindrical pins are widely used in the connection and positioning of key components such as engines, transmissions, and chassis. For instance, in the connection between the engine block and cylinder head, cylindrical pins ensure precise alignment between the cylinder head and block, preventing misalignment due to thermal expansion or vibration. Additionally, cylindrical pins are used to secure brake pads and suspension systems, ensuring the safety and stability of the vehicle during operation.
3. Aerospace Applications
In the aerospace field, the requirements for cylindrical pins are more stringent. Since aerospace equipment operates in extreme environments, cylindrical pins must possess high strength and corrosion resistance. For example, in critical areas such as the fixation of aircraft engine blades and the connection of fuselage structures, cylindrical pins ensure the stability of components under high vibration, temperature, and pressure conditions.
4. Connection and Fixation in Electronic Devices
In electronic devices, cylindrical pins are commonly used for the fixation and connection of circuit boards. For example, in computer motherboards and smartphone motherboards, cylindrical pins ensure precise alignment between the circuit board and the casing, preventing poor contact caused by vibration or external forces. Additionally, cylindrical pins are used to secure heat sinks and connectors, ensuring the stable operation of electronic devices.
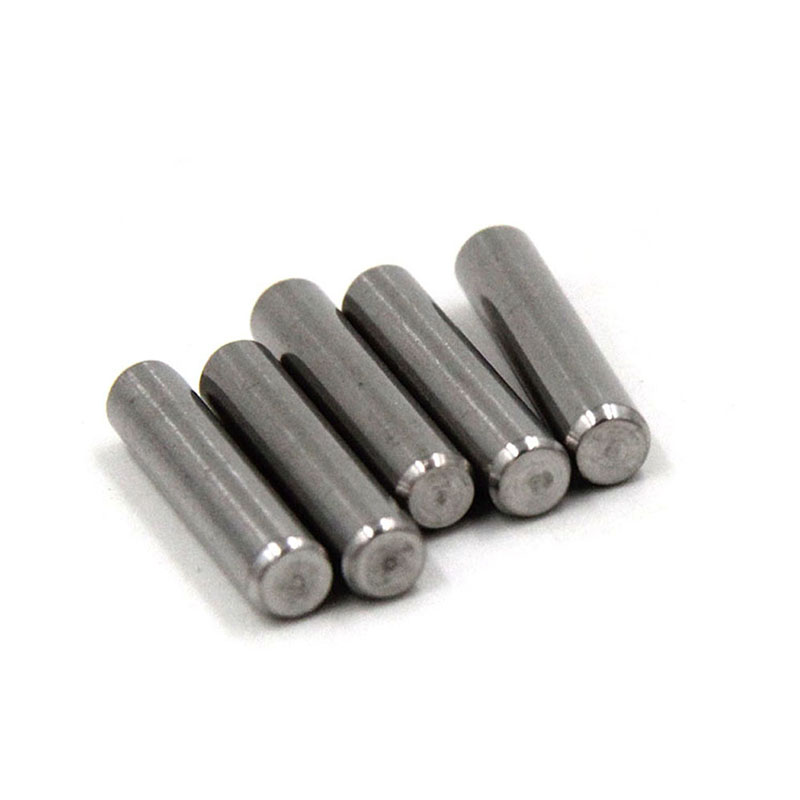
5. Applications in Other Fields
Beyond the aforementioned fields, cylindrical pins are also widely used in industries such as construction, furniture, and toys. For instance, in furniture manufacturing, cylindrical pins can be used to connect wooden boards and metal frames, ensuring the structural stability and aesthetics of the furniture. In the construction industry, cylindrical pins are used to secure steel structures and connect pipelines, ensuring the safety and durability of buildings.
Usage Methods of Cylindrical Pins
1. Selecting the Appropriate Cylindrical Pin
Before using a cylindrical pin, it is essential to select the appropriate pin based on the specific application scenario. Considerations include:
Material: Choose the material based on the working environment. For example, in corrosive environments, stainless steel or zinc-plated cylindrical pins should be selected; in high-temperature environments, heat-resistant alloy steel pins are preferable.
Diameter and Length: Select the diameter and length based on the aperture and thickness of the connecting components. The diameter of the cylindrical pin should match the aperture, and the length should be slightly greater than the total thickness of the connecting components.
Surface Treatment: Choose the surface treatment based on the usage environment. For example, in humid environments, zinc-plated or chrome-plated cylindrical pins should be selected to enhance corrosion resistance.
2. Pre-Installation Preparations
Before installing the cylindrical pin, the following preparations are necessary:
Cleaning the Connecting Components: Ensure that the apertures and surfaces of the connecting components are clean, free from oil, rust, or other contaminants that could affect the installation and performance of the cylindrical pin.
Checking the Aperture: Use measuring tools to check the aperture of the connecting components, ensuring it matches the diameter of the cylindrical pin. If the aperture is too small, a reamer can be used for adjustment; if the aperture is too large, the connecting components may need to be replaced or a larger diameter cylindrical pin should be used.
3. Installation Methods of Cylindrical Pins
The main installation methods for cylindrical pins include:
Press-Fit Method: Align the cylindrical pin with the aperture of the connecting component and press it in using a press or hammer. During pressing, ensure that the cylindrical pin remains perpendicular to the aperture to avoid tilting or bending. For larger diameter pins, lubricant can be used to reduce friction and facilitate installation.
Tap-Fit Method: For smaller diameter pins, a hammer can be used to gently tap them into place. Care should be taken to control the force to avoid damaging the pin or the connecting component.
Threaded Connection Method: For threaded cylindrical pins, a wrench or screwdriver can be used to screw them into the threaded hole of the connecting component. Ensure proper alignment of the threads to avoid damage.
4. Post-Installation Inspection and Maintenance
After installing the cylindrical pin, the following inspections and maintenance are necessary:
Checking Installation Quality: Use measuring tools to check the position and depth of the cylindrical pin, ensuring a tight fit with the aperture of the connecting component without any looseness or tilting.
Regular Inspection and Maintenance: During use, regularly inspect the connection status of the cylindrical pin to ensure there is no looseness, wear, or corrosion. If any abnormalities are found, timely replacement or repair is necessary.
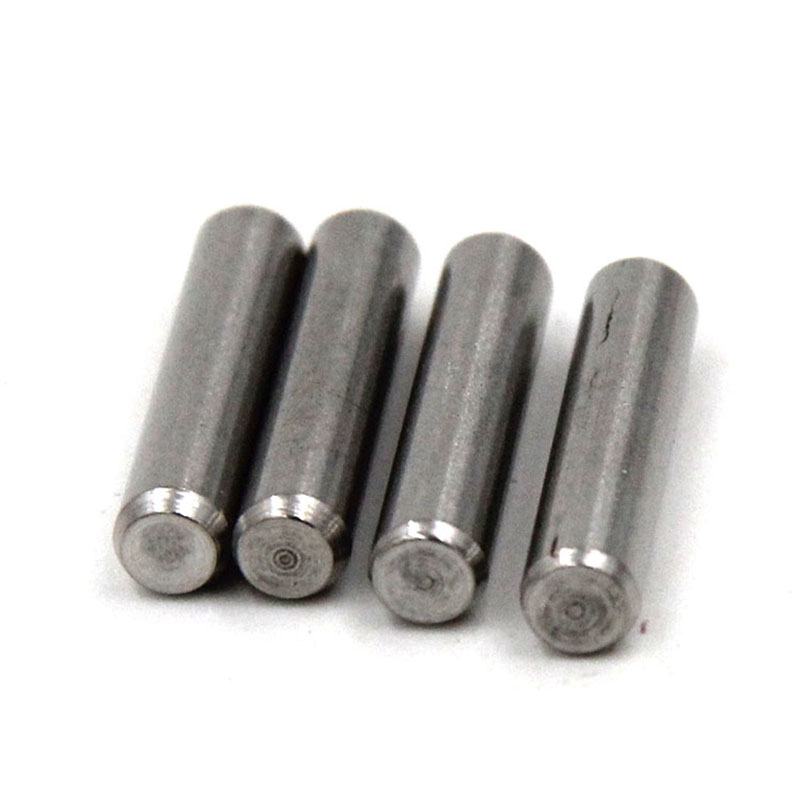
Precautions for Using Cylindrical Pins
1. Avoid Overloading: The load-bearing capacity of cylindrical pins is limited. Avoid overloading to prevent pin breakage or damage to the connecting components.
2. Prevent Corrosion: In humid or corrosive environments, select corrosion-resistant cylindrical pins and perform regular anti-rust treatments.
3. Correct Installation: Ensure that the cylindrical pin is installed vertically to avoid tilting or bending, which could affect its performance.
4. Regular Inspection: Regularly inspect the connection status of the cylindrical pin during use to ensure there is no looseness, wear, or corrosion.
Conclusion
As an important mechanical connector, cylindrical pins are widely used in mechanical equipment, automotive, aerospace, and electronic devices. By selecting the appropriate cylindrical pin, using correct installation methods, and performing regular inspections and maintenance, the optimal performance of cylindrical pins can be ensured in various application scenarios, enhancing the stability and lifespan of equipment. It is hoped that this article will help readers better understand and apply cylindrical pins, providing reference and guidance for practical work.