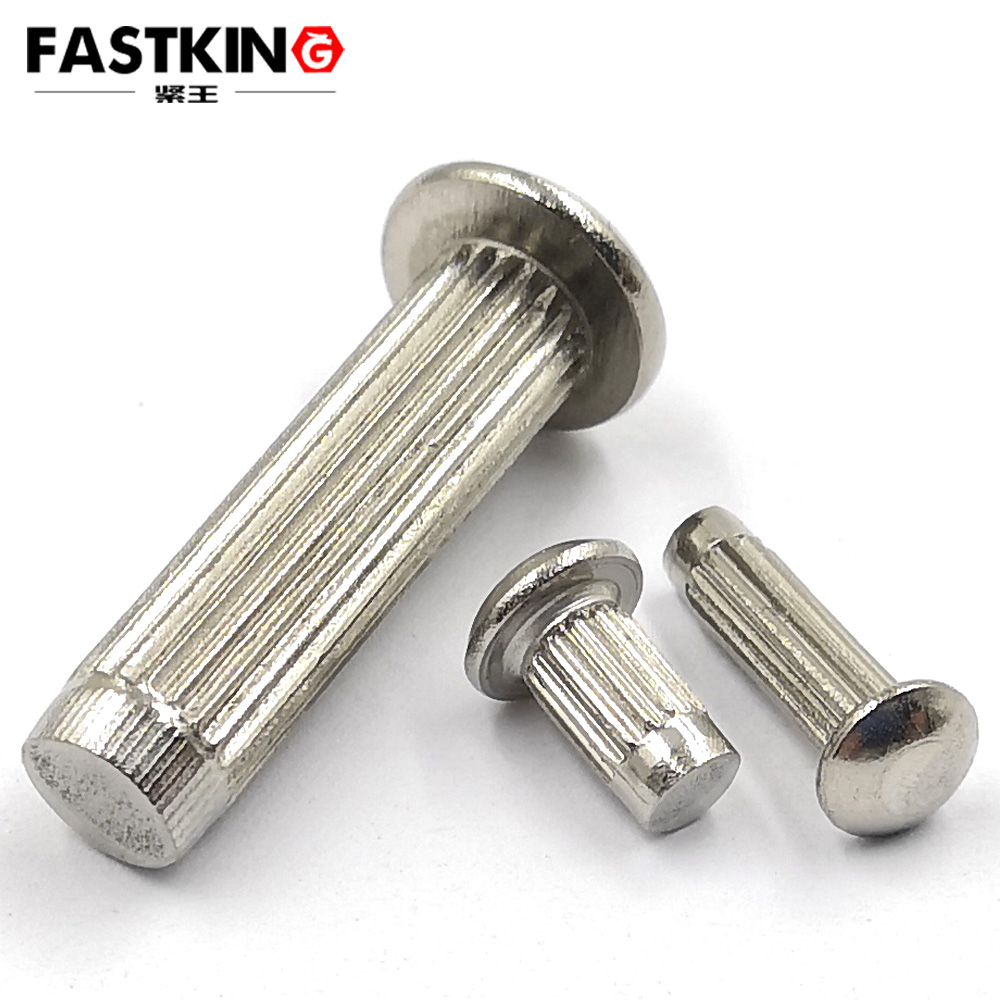
Typical Application Scenarios of Signage Rivets
In the machinery sector, signage rivets are primarily used to secure equipment nameplates, operation instruction plates, and safety warning signs. These signs carry crucial information such as model parameters, operating instructions, and precautions, and must remain stable over time. For instance, on heavy machinery, signage rivets need to withstand vibrations and impacts during operation, requiring excellent anti-vibration properties.
In electronics manufacturing, signage rivets are equally prevalent. Products like mobile phones, computers, and household appliances use signage rivets to attach product labels and certification marks. These rivets must ensure reliable connections while also considering aesthetic factors, often undergoing surface treatments to harmonize with the product's appearance.
In the transportation manufacturing sector, the use of signage rivets is even more stringent. Signs on vehicles such as cars, trains, and airplanes are directly related to safety and must remain secure under various environmental conditions. Particularly in aerospace, signage rivets need to possess special properties like high-temperature resistance and corrosion resistance.
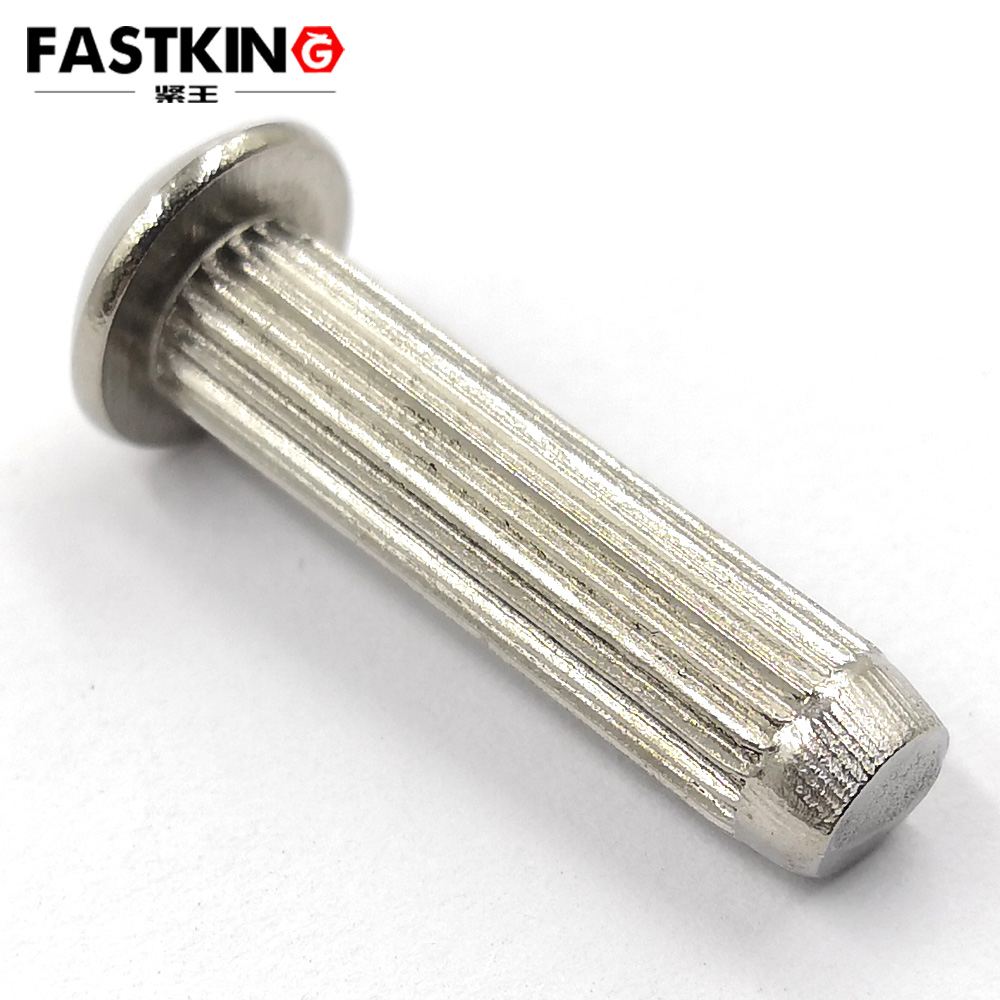
Correct Usage of Signage Rivets
Selecting the appropriate specifications for signage rivets is essential to ensure effectiveness. The choice of rivet type and size depends on the sign material, thickness, and the characteristics of the installation base. Generally, the rivet diameter should be slightly larger than the sign hole, and the length should ensure a firm grip on both the sign and the base material.
The choice of installation tools significantly impacts riveting quality. Manual rivet guns are suitable for small-scale operations, while pneumatic rivet guns are better for mass production. When using tools, it is crucial to maintain a perpendicular angle between the rivet and the workpiece surface, applying even pressure to ensure a smooth riveting process.
Quality inspection is a critical step in ensuring riveting effectiveness. After riveting, check whether the rivet head is fully formed, whether the sign is securely fixed, and whether there is any looseness. For critical equipment, vibration and pull tests are necessary to confirm that the riveting quality meets requirements.
Precautions for Using Signage Rivets
Safety is a paramount concern when using signage rivets. Operators should wear protective goggles to prevent debris from flying during riveting. When using electric or pneumatic tools, precautions must be taken to avoid pinching injuries and electric shocks. The work area should be kept clean to prevent obstructions.
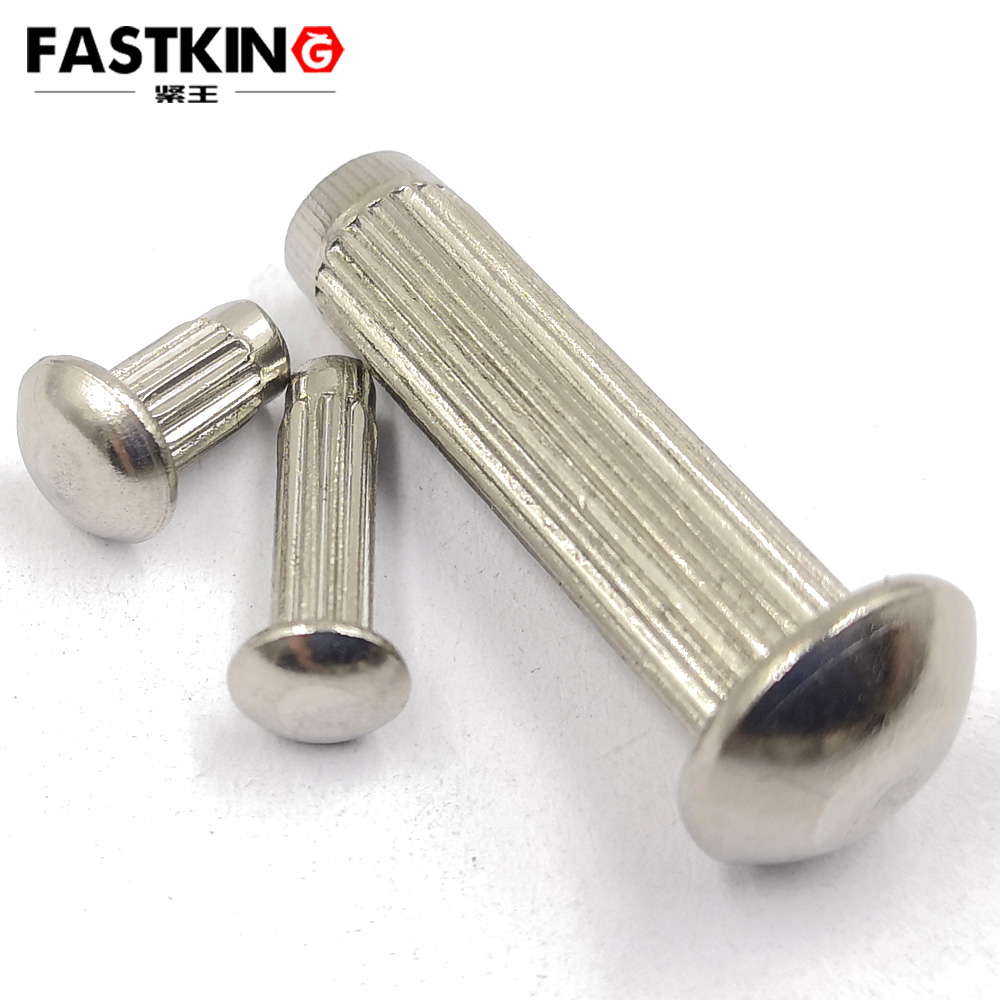
Environmental factors significantly affect riveting quality. In humid environments, rivets with good rust resistance should be selected; in high-temperature settings, rivets made from heat-resistant materials are required. Before installation, ensure that the workpiece surface is clean and dry to avoid oil contamination affecting the riveting outcome.
Maintenance is crucial for extending the lifespan of rivets. Regularly inspect the rivet connections, promptly identifying and replacing any loose or damaged rivets. For exposed rivets, applying anti-rust oil can help prevent corrosion.
Though small, signage rivets play a vital role in modern manufacturing. Proper selection and use of signage rivets not only ensure product quality but also enhance the safety and reliability of equipment. With the continuous emergence of new materials and processes, the performance of signage rivets will further improve, providing more reliable connection solutions for industrial manufacturing. In practical applications, it is essential to scientifically select signage rivets based on specific needs and strictly adhere to operational standards to ensure every connection is secure and reliable.