Countersunk solid rivets are a common type of mechanical fastener widely used in various industrial fields. Their defining feature is that the head sits flush with the surface of the workpiece after installation, making them suitable for applications where surface smoothness is critical. This article provides a detailed overview of the usage methods and application scenarios of countersunk solid rivets.
I. Structure and Characteristics of Countersunk Solid Rivets
Structure
Countersunk solid rivets consist of a shank and a head. The head is designed to be countersunk, ensuring it sits flush with the workpiece surface after installation. The shank is solid, providing high strength and stability.
Characteristics
High Strength: The solid structure offers excellent tensile and shear strength.
Flush Finish: The countersunk design ensures a smooth surface, ideal for applications requiring a flat finish.
Corrosion Resistance: Rivets can be made from materials like stainless steel or aluminum to suit different environmental conditions.
II. Usage Methods for Countersunk Solid Rivets
Preparation
Select the Right Rivet: Choose the appropriate rivet size and material based on the workpiece's material and thickness.
Prepare Tools: Common tools include a rivet gun, drill, and file.
Installation Steps
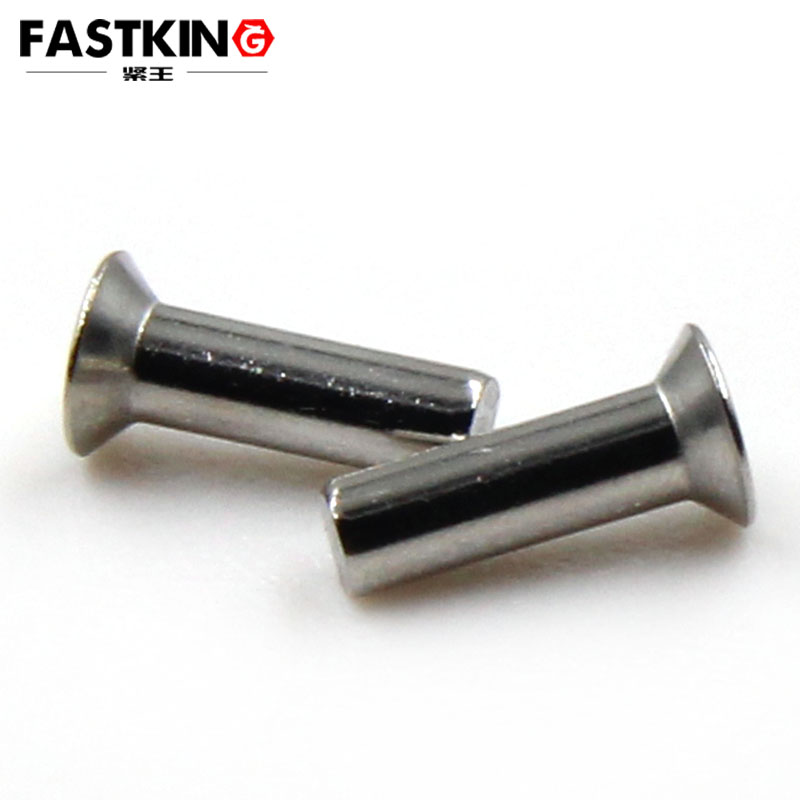
Drilling: Drill holes in the workpieces to be joined. The hole diameter should match the rivet diameter, typically 0.1-0.2mm larger.
Insert the Rivet: Place the rivet into the hole, ensuring the head sits flush with the workpiece surface.
Riveting: Use a rivet gun to expand the rivet's tail, securing it tightly against the workpiece.
Finishing: Use a file to smooth the rivet tail, ensuring it is flush with the surface.
Precautions
Hole Size Control: Incorrect hole sizes can affect riveting quality; precision is essential.
Riveting Force Control: Excessive force may break the rivet, while insufficient force may result in a weak connection.
Surface Treatment: For workpieces requiring anti-corrosion treatment, surface preparation should be done before riveting.
III. Application Scenarios for Countersunk Solid Rivets
Aerospace
In aerospace, the strength and weight of fasteners are critical. Countersunk solid rivets are widely used in aircraft fuselages, wings, and other key components due to their high strength and lightweight properties.
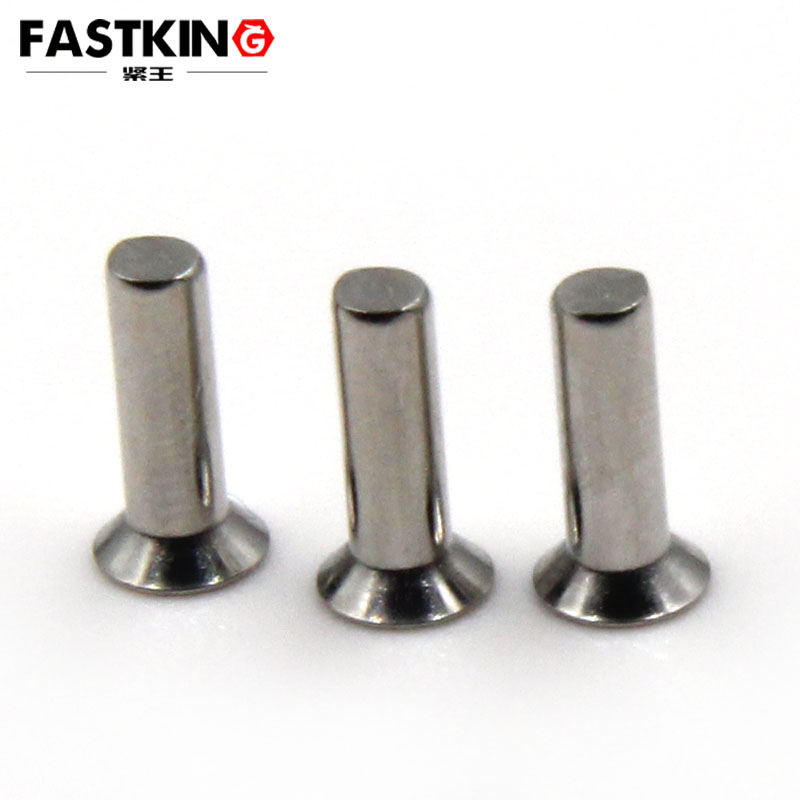
Automotive Manufacturing
In automotive manufacturing, high-strength fasteners are required for body and chassis components. Countersunk solid rivets provide reliable connections while maintaining a smooth surface, making them suitable for doors, hoods, and other parts.
Electronics
In electronics manufacturing, precision and surface smoothness are crucial. Countersunk solid rivets are used in circuit boards, casings, and other components to ensure device stability and aesthetics.
Construction Industry
In construction, steel structures require high-strength fasteners. Countersunk solid rivets are used in bridges, high-rise buildings, and other steel structures to provide reliable support and stability.
Shipbuilding
In shipbuilding, fasteners must withstand corrosion and provide high strength. Countersunk solid rivets are ideal for hulls, decks, and other components due to their corrosion resistance and strength.
IV. Advantages and Limitations of Countersunk Solid Rivets
Advantages
High Strength: The solid structure provides excellent tensile and shear strength.
Flush Finish: The countersunk design ensures a smooth surface.
Corrosion Resistance: Material options like stainless steel and aluminum suit various environments.

Limitations
Complex Installation: The installation process is more complicated than other fasteners, requiring specialized tools and precision.
Higher Cost: The high strength and precision manufacturing result in relatively higher costs.
V. Conclusion
Countersunk solid rivets are high-strength mechanical fasteners widely used in aerospace, automotive manufacturing, electronics, construction, and shipbuilding. Their high strength and flush design make them ideal for applications requiring both strength and surface smoothness. However, their complex installation and higher cost may limit their use in some scenarios. In practice, selecting the appropriate rivet size and material based on specific needs is crucial to ensuring reliable and stable connections.
Through this article, readers should have gained a deeper understanding of the usage methods and application scenarios of countersunk solid rivets. Proper selection and use of these rivets can significantly enhance product quality and performance.