Usage Methods for Torx Set Screws
1. Tool Preparation
A dedicated Torx screwdriver is essential for installing or removing Torx set screws. The screwdriver tip must perfectly match the screw’s recess size: oversized tips risk damaging the recess, while undersized ones fail to transmit torque effectively. For versatility, prepare a set of Torx screwdrivers covering multiple sizes (e.g., T5 to T30).
2. Installation Steps
Surface Preparation: Clean the threaded hole and screw surface to remove debris or contaminants.
Initial Alignment: Manually thread the screw into the hole for 2–3 rotations to ensure proper thread engagement.
Tightening: Use a Torx screwdriver to rotate the screw clockwise with controlled force until the desired torque is achieved. For precision equipment, employ a torque wrench to meet exact specifications (e.g., 5–10 N·m for small screws).
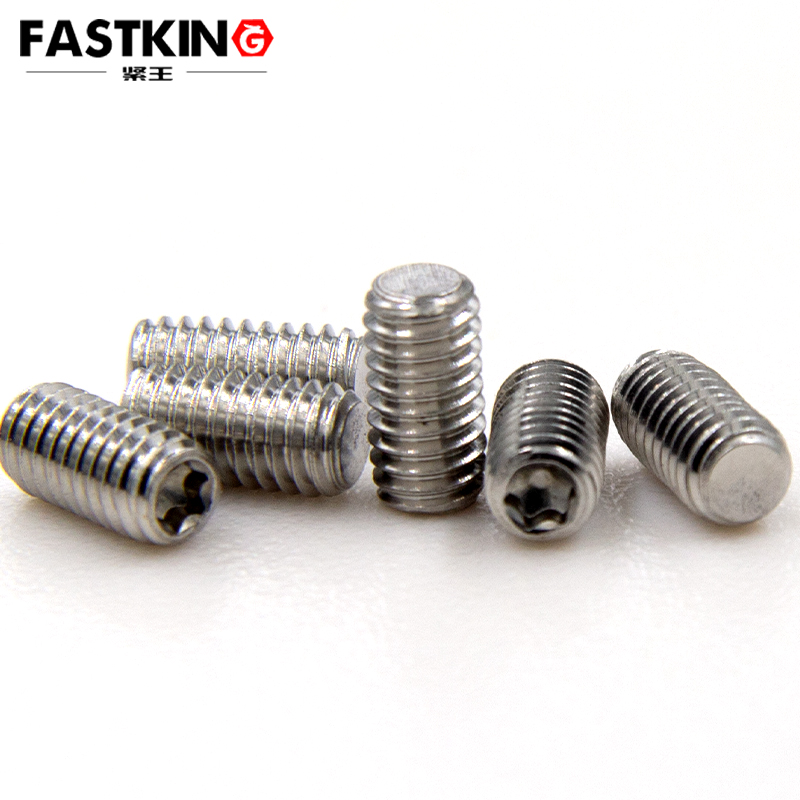
3. Removal Guidelines
To disassemble, select the correct Torx screwdriver and rotate counterclockwise. For corroded or overtightened screws:
- Apply penetrating oil (e.g., WD-40) and wait 10–15 minutes.
- Avoid excessive force to prevent recess deformation.
- For critical assemblies, schedule periodic inspections to check tightness and wear.
Application Scenarios
1. Precision Instrumentation
In optical devices, microscopes, or metrology tools, Torx set screws ensure vibration-resistant alignment. For example, microscope lens barrels rely on these screws to maintain optical component positioning, preventing image distortion caused by micromovements.
2. Electronics Manufacturing
Smartphones, laptops, and wearables use Torx set screws for securing motherboards, chassis, and internal modules. Their compact design supports miniaturization trends, while their tamper-resistant recess enhances consumer device security.
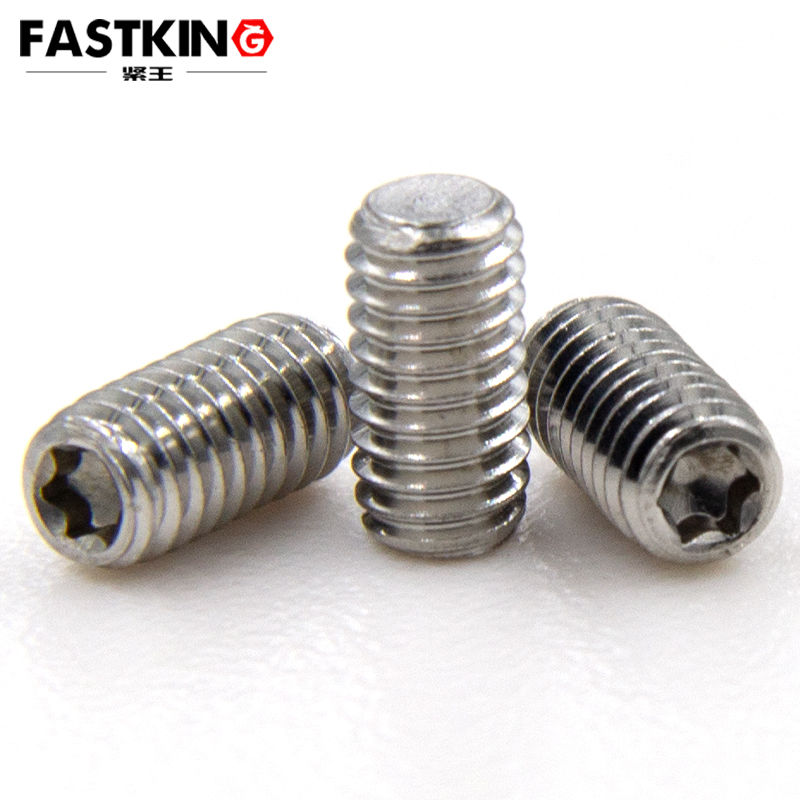
3. Automotive Industry
From engine components (e.g., sensor mounts) to interior trim, Torx set screws excel in high-vibration, high-temperature environments. Their anti-loosening properties reduce maintenance frequency in critical systems like brake assemblies or transmission housings.
4. Aerospace Engineering
Aerospace applications demand extreme reliability. Torx set screws are used in aircraft skin fastening, avionics mounts, and satellite mechanisms. Their recess design minimizes cam-out (slippage) during high-torque installation, ensuring stability under intense aerodynamic stress.
Usage Considerations
1. Torque Control
Adhere to manufacturer-recommended torque values based on screw material (e.g., stainless steel, alloy steel) and diameter. Over-tightening risks thread stripping, while under-tightening compromises joint integrity. Example torque ranges:
- M3 screws: 1.5–3 N·m
- M6 screws: 10–15 N·m
2. Environmental Adaptability
Corrosive Environments: Opt for A2/A4 stainless steel or zinc-nickel coated screws.
High-Temperature Settings: Select heat-resistant alloys (e.g., Inconel) to account for thermal expansion.
Outdoor Applications: Pair with silicone sealants to prevent moisture ingress.
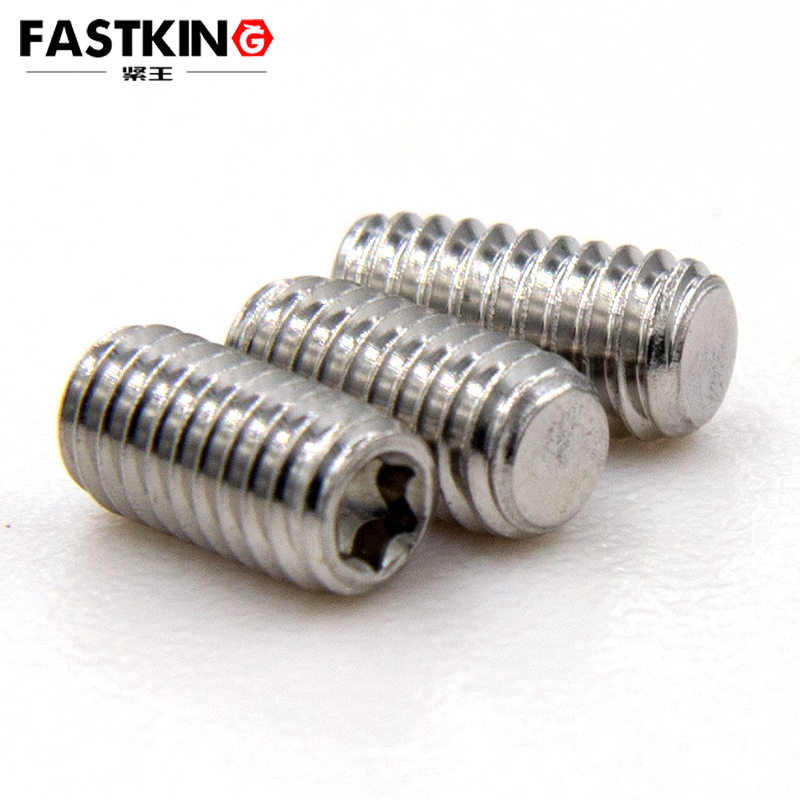
3. Maintenance Protocols
- Conduct quarterly torque checks in high-vibration systems (e.g., industrial robots).
- Replace screws showing wear, corrosion, or recess deformation.
- Use thread-locking adhesives (e.g., Loctite 243) for permanent installations.
Conclusion
As a high-efficiency fastening solution, Torx set screws play an indispensable role in modern manufacturing. Their precision torque transmission, tamper resistance, and versatility make them ideal for industries prioritizing reliability and miniaturization. By mastering proper installation techniques and selecting appropriate variants for specific environments, engineers can optimize equipment performance and longevity. With advancements in materials science—such as carbon-fiber-reinforced polymers or smart screws with embedded sensors—Torx set screws are poised to drive innovation in next-generation industrial systems.