The Ubiquitous Foundation of Industry
In the automotive manufacturing sector, small hex nuts are essential for ensuring vehicle safety. From the engine compartment to the chassis, thousands of small hex nuts tightly connect various components. For instance, the connection between the cylinder head and the cylinder block in a car engine requires high-strength small hex nuts that must withstand high temperatures and pressures, ensuring stable engine performance under extreme conditions.
In the aerospace industry, the application of small hex nuts reaches its pinnacle. The assembly of aircraft skin and the fixation of engine components necessitate the use of specially treated titanium alloy small hex nuts. These nuts must possess an exceptionally high strength-to-weight ratio and be capable of resisting extreme temperature variations and intense vibrations.
In electronic products, small hex nuts exhibit different characteristics. In precision devices such as smartphones and laptops, miniature small hex nuts are tasked with securing critical components like motherboards and heat sinks. These nuts, often only 2-3mm in size, must ensure the stability of the devices during frequent use.
The Art of Precision Application
Selecting the appropriate small hex nut involves considering several factors. First is the material: ordinary carbon steel nuts are suitable for general applications, stainless steel nuts are used in environments requiring corrosion resistance, and titanium alloy nuts are employed where weight and strength are of particular concern. Second is the strength grade: nuts of different grades can withstand varying preloads and working loads.
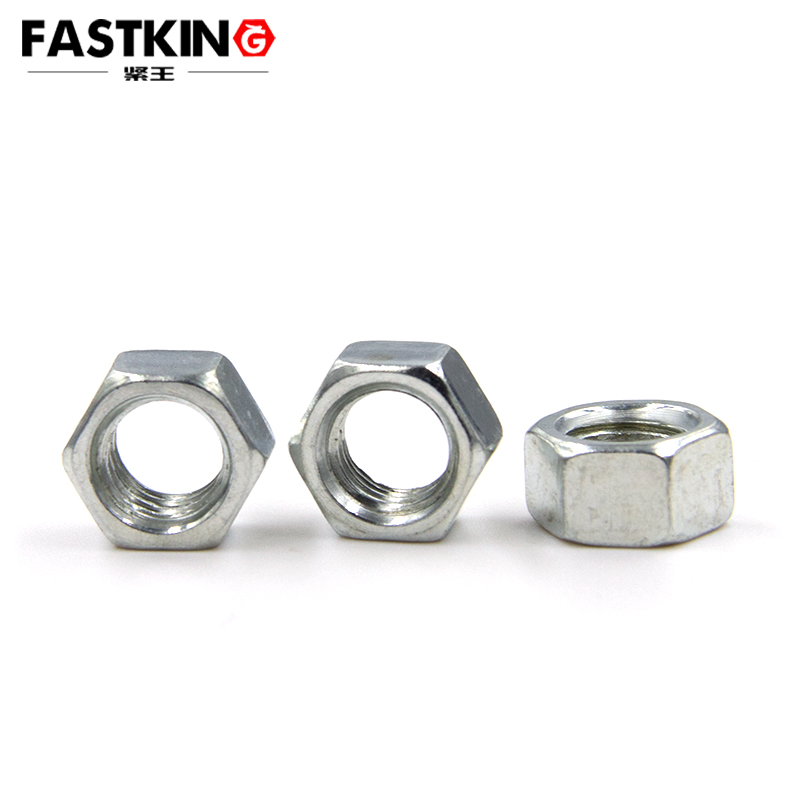
The correct installation method directly affects the performance of small hex nuts. Using a torque wrench to tighten to the specified torque value is a basic requirement. Over-tightening can lead to thread damage or bolt fracture, while under-tightening may fail to achieve the desired fastening effect. In critical applications, anti-loosening washers or thread-locking adhesives are also necessary to prevent nut loosening.
Maintenance is equally important. Regularly checking the tightness of nuts, especially on equipment subject to significant vibration, requires a well-established inspection system. For nuts exposed to harsh environments, rust prevention measures are essential, and replacement may be necessary when needed.
Technological Innovation and Development Trends
Advances in materials science have brought new opportunities for the development of small hex nuts. The application of nanotechnology has made nut surface treatments more refined, significantly enhancing wear resistance and corrosion resistance. The emergence of new composite materials allows nuts to maintain strength while becoming lighter.
Innovations in manufacturing processes are mainly reflected in improvements in machining accuracy and production efficiency. The widespread use of CNC machine tools has enabled nut dimensional accuracy to reach the micrometer level, while the application of automated production lines has greatly increased production efficiency and reduced costs.
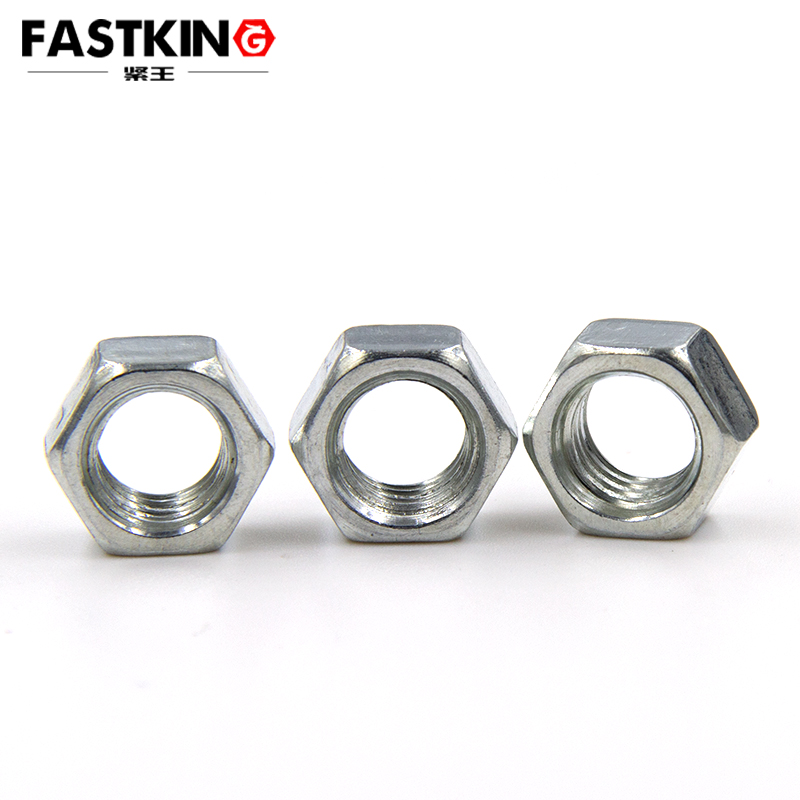
In the future, with the development of smart manufacturing, small hex nuts may integrate sensors to enable real-time monitoring of fastening status. The maturation of 3D printing technology will also provide new solutions for the custom production of special specification nuts.
The evolution of small hex nuts reflects the progress of industrial civilization. From initial hand forging to modern intelligent production, and from single functions to multifunctional integration, the development of small hex nuts bears witness to humanity's relentless pursuit of precision manufacturing. In the future development of industry, this seemingly simple component will continue to play its irreplaceable role, supporting the operation of the modern industrial system in a more intelligent and reliable manner.