40Cr alloy steel is a commonly used medium-carbon alloy steel known for its high strength, toughness, and wear resistance. It is widely applied in industries such as mechanical manufacturing, automotive, and aerospace. Taper pins, as common fasteners, are primarily used for positioning and securing two or more components to ensure precise relative positioning during assembly and use. The blackening treatment of the flat ends of taper pins is a surface treatment process aimed at enhancing their corrosion resistance, wear resistance, and aesthetic appeal.
Definition and Purpose of Blackening Treatment
Blackening treatment, also known as bluing, is a chemical surface treatment process that forms a dense oxide layer on the metal surface to improve its corrosion and wear resistance. For 40Cr alloy steel taper pins, blackening not only enhances surface hardness but also improves appearance, making them more competitive in the market.
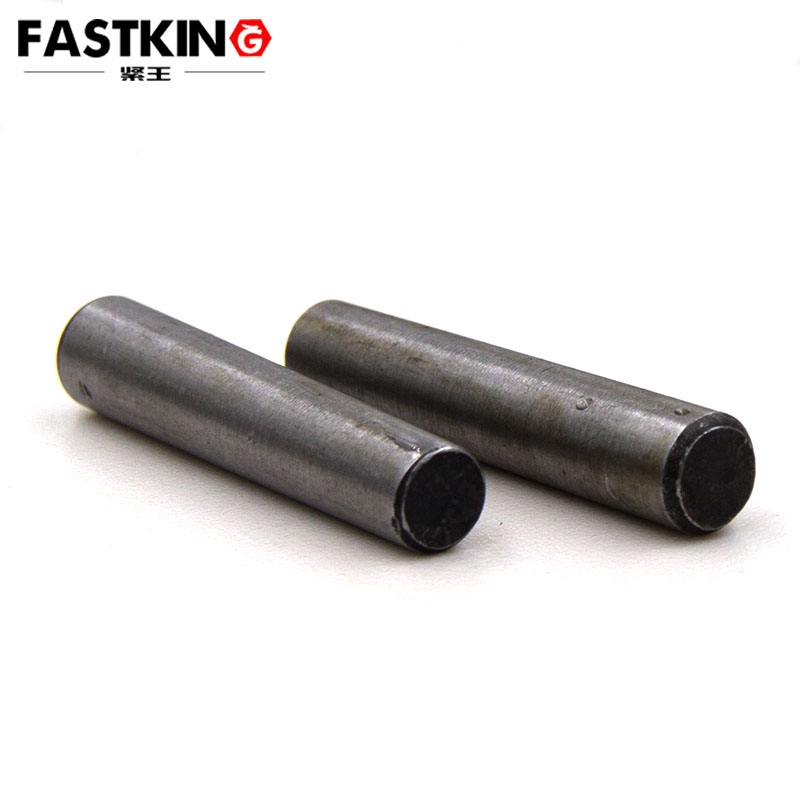
Usage Occasions for Blackened Flat Ends of 40Cr Alloy Steel Taper Pins
1. Mechanical Manufacturing Industry: In mechanical manufacturing, taper pins are commonly used for positioning and securing various mechanical components. Blackened taper pins can better resist corrosive media in the environment, extending their service life.
2. Automotive Industry: Automotive components are often exposed to harsh environments, such as high temperatures, humidity, and corrosive gases. Blackened taper pins effectively prevent rust, ensuring the safety and reliability of vehicles.
3. Aerospace: The aerospace industry demands extremely high corrosion and wear resistance for components. Blackened taper pins meet these stringent requirements, ensuring the safe operation of aircraft.
4. Electronic Devices: In electronic devices, taper pins are used to secure and position precision components. Blackening not only improves corrosion resistance but also reduces surface friction, facilitating assembly and disassembly.
Methods for Blackening the Flat Ends of 40Cr Alloy Steel Taper Pins
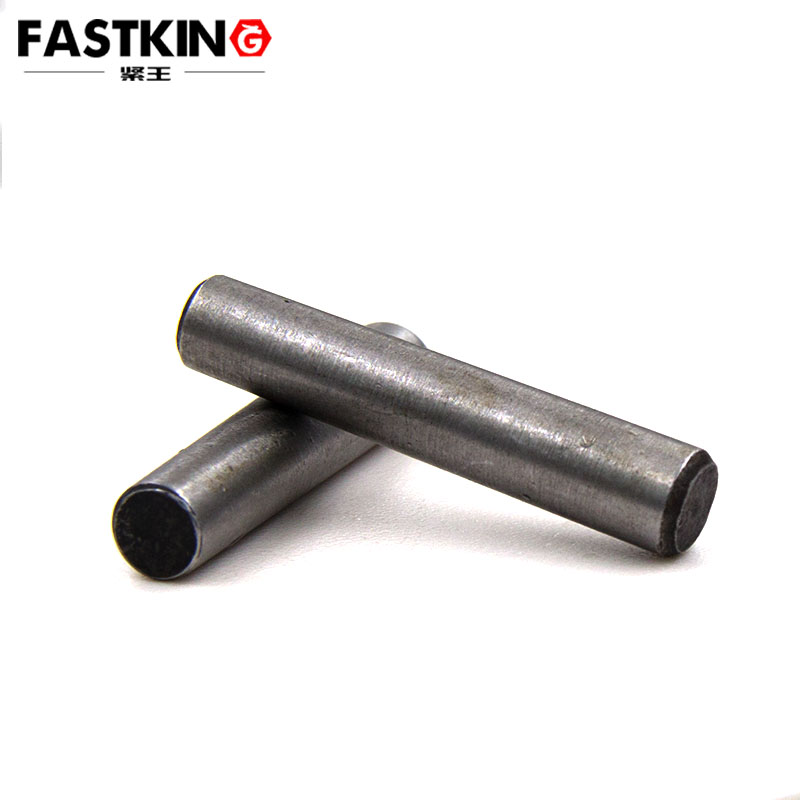
1. Pre-Treatment:
Cleaning: Thoroughly clean the taper pins to remove oil, rust, and other impurities. Common cleaning methods include alkaline cleaning, acid cleaning, and ultrasonic cleaning.
Degreasing: Use organic solvents or alkaline solutions to remove surface oils, ensuring the effectiveness of subsequent treatments.
Acid Cleaning: Remove surface scale and rust through acid cleaning, typically using hydrochloric or sulfuric acid solutions.
2. Blackening Treatment:
Chemical Blackening: Immerse the cleaned taper pins in a blackening solution, commonly composed of sodium hydroxide, sodium nitrite, and sodium nitrate. At high temperatures (typically 135-145°C), a dense magnetite (Fe3O4) layer forms on the surface.
Time Control: The blackening process typically lasts 10-30 minutes, with adjustments based on the pin size and required coating thickness.
Temperature Control: The temperature of the blackening solution must be strictly controlled, as excessively high or low temperatures can affect the results. It is usually maintained between 135-145°C.
3. Post-Treatment:
Rinsing: Immediately rinse the taper pins with clean water after blackening to remove residual blackening solution.
Soaping: Immerse the pins in a soaping solution, typically soap water or a specialized soaping agent, to enhance surface lubrication and corrosion resistance.
Drying: Finally, dry the taper pins using hot air or natural drying.
4. Quality Inspection:
Visual Inspection: Check for uniform and smooth surfaces without noticeable color differences or spots.
Coating Thickness Measurement: Use a coating thickness gauge to ensure the blackening layer meets design requirements.
Corrosion Resistance Testing: Conduct salt spray tests or other methods to evaluate the corrosion resistance of the blackened layer.
Precautions
1. Safety Measures: The chemicals used in blackening are corrosive and toxic. Operators must wear protective gloves, masks, and goggles to ensure safety.
2. Process Control: Strictly control the composition, temperature, and duration of the blackening solution to ensure consistent quality of the blackened layer.
3. Equipment Maintenance: Regularly inspect and maintain blackening equipment to ensure its proper operation and long-term stability.
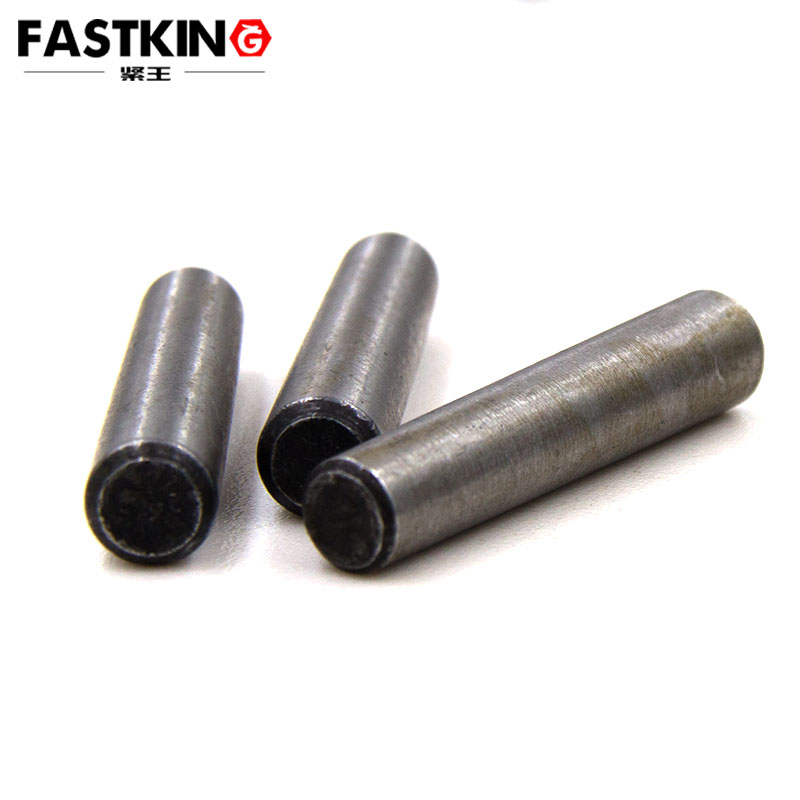
Conclusion
The blackening treatment of the flat ends of 40Cr alloy steel taper pins is an effective surface treatment process that significantly enhances their corrosion resistance, wear resistance, and aesthetic appeal. Through proper pre-treatment, blackening, and post-treatment processes, taper pins can perform excellently in various demanding applications. In practice, the appropriate blackening process and parameters should be selected based on specific usage environments and requirements to achieve optimal results.