Countersunk cross screws, seemingly ordinary fasteners, play an indispensable role in modern industrial production and daily life. With their unique design and wide range of applications, they are crucial in fields such as mechanical manufacturing, electronic products, and construction engineering. This article will delve into the application scenarios and usage methods of countersunk cross screws, revealing the significant value of this "invisible hero."
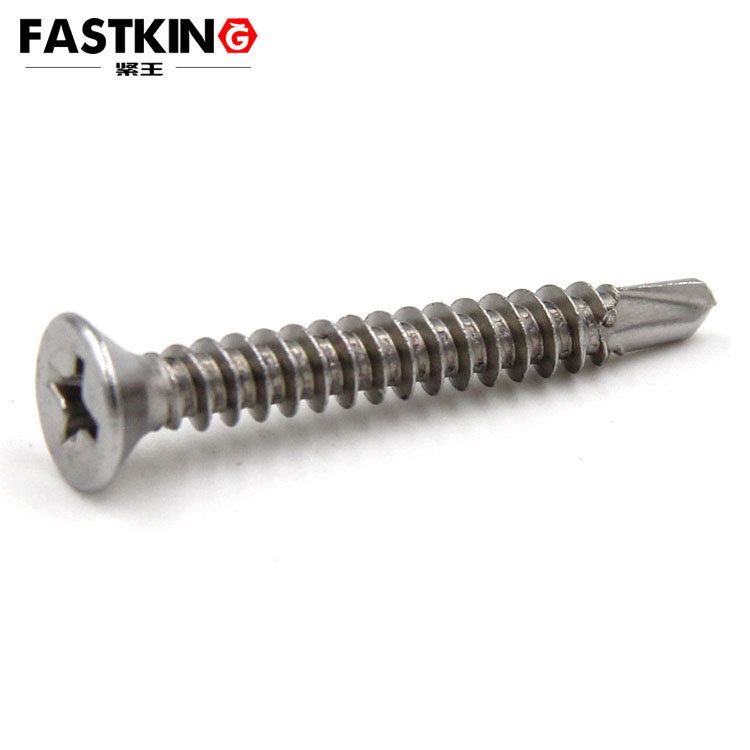
I. Unique Advantages of Countersunk Cross Screws
Countersunk cross screws feature a countersunk design that allows the screw head to be fully embedded into the workpiece surface, creating a smooth appearance. This design is not only aesthetically pleasing but also avoids safety hazards caused by protrusions, making it particularly suitable for applications requiring high surface flatness. The cross-slot design provides better torque transmission efficiency, making installation more convenient.
In terms of material selection, countersunk cross screws can be made from carbon steel, stainless steel, copper, and other materials to meet the strength and corrosion resistance requirements of different environments. Surface treatments such as zinc plating and nickel plating further enhance the durability and aesthetics of the screws.
II. Analysis of Wide Application Scenarios
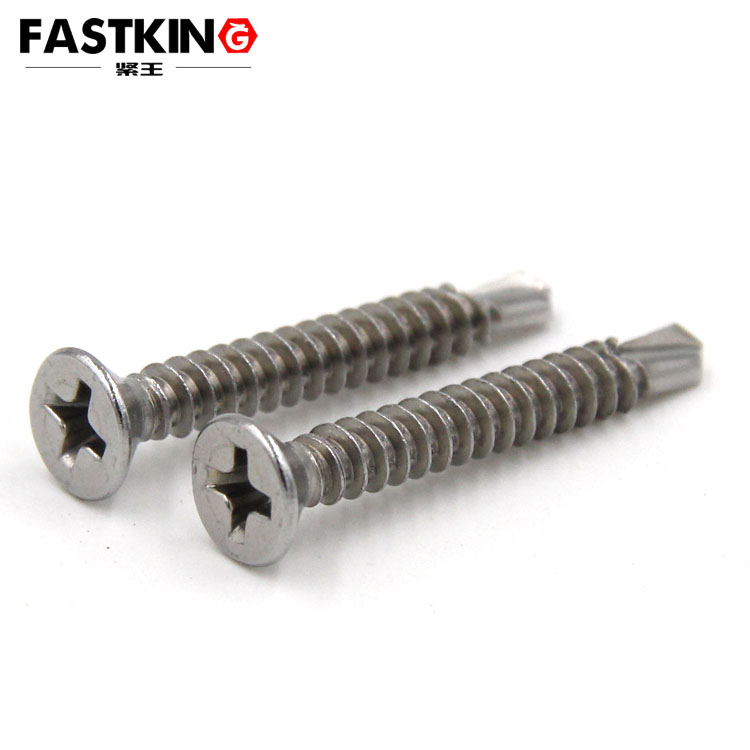
In the field of mechanical manufacturing, countersunk cross screws are key connectors for equipment assembly. For example, in CNC machine tools, the housing, panels, and other components are secured using countersunk cross screws, ensuring both reliable connections and a smooth, aesthetically pleasing surface.
In electronic product manufacturing, countersunk cross screws are even more prevalent. Precision electronic devices such as smartphones and laptops use a large number of miniature countersunk cross screws for component fixation. These screws are not only dimensionally precise but also finely surface-treated to ensure they do not damage delicate electronic components.
In the construction engineering field, countersunk cross screws are commonly used for curtain wall installation and decorative panel fixation. Their flush installation effect seamlessly integrates with building surfaces while providing reliable connection strength. In furniture manufacturing, countersunk cross screws achieve a perfect balance of beauty and practicality.
III. Detailed Explanation of Correct Usage Methods
When selecting countersunk cross screws, it is essential to determine the appropriate specifications based on the properties and thickness of the materials being joined. The screw length should ensure that 2-3 thread pitches remain after tightening, guaranteeing connection strength while avoiding damage to the workpiece from excessive length.
During installation, it is crucial to ensure accurate screw hole positioning and that the hole diameter matches the screw diameter. Use a suitable cross-head screwdriver, applying vertical force to avoid stripping. For precision equipment installation, a torque screwdriver is recommended to ensure consistent tightening force for each screw.
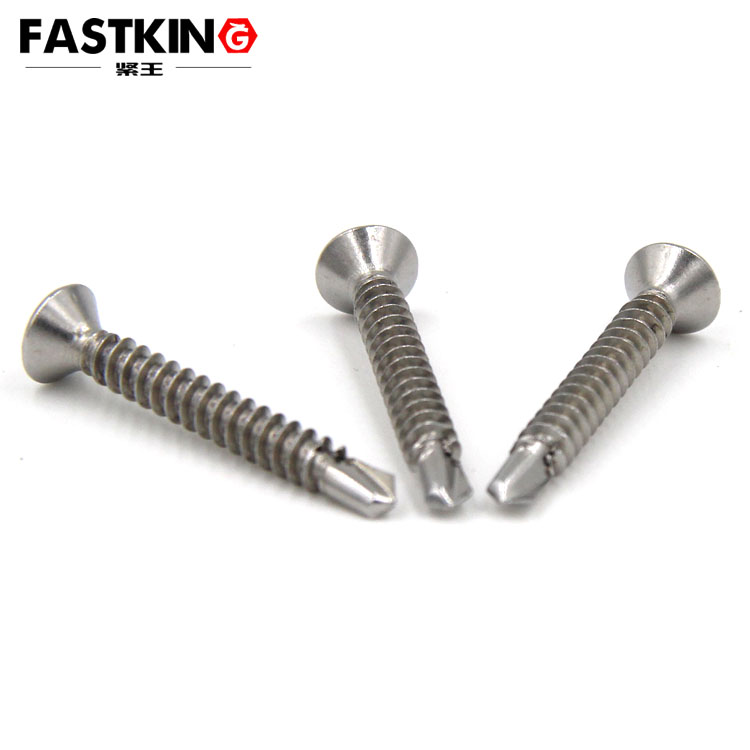
In terms of maintenance, regularly check the tightness of the screws and re-tighten if necessary. For screws used in corrosive environments, pay attention to the integrity of the surface protective layer and replace damaged screws promptly.
The application of countersunk cross screws reflects the modern industry's pursuit of perfection in details. From large mechanical equipment to miniature electronic products, from construction engineering to home decor, this seemingly simple fastener plays a vital role. With advancements in material science and manufacturing processes, countersunk cross screws will continue to demonstrate their value in more fields, providing reliable support for industrial production and daily life.