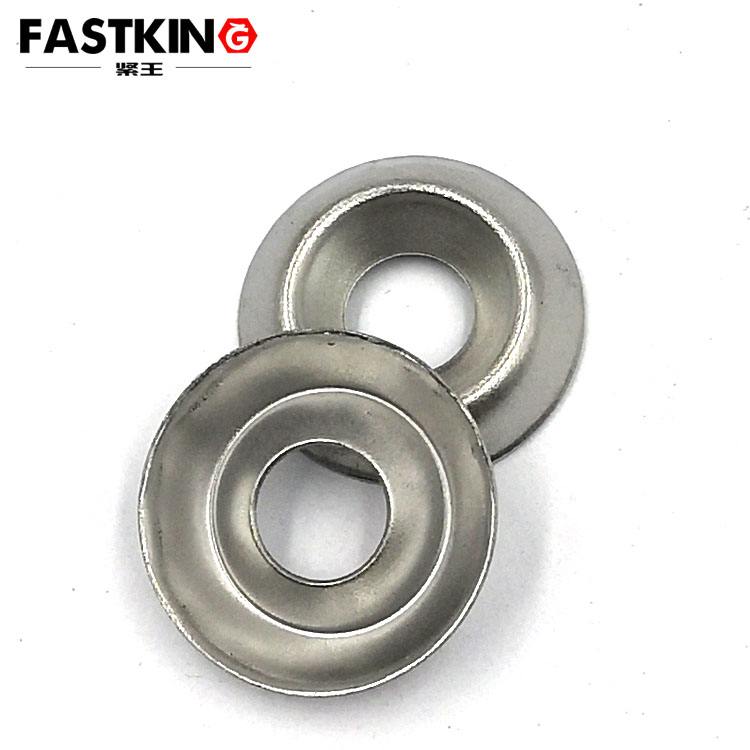
Structural Characteristics of Wave Washers
Wave washers employ a distinctive wave-like design, which grants them excellent elastic properties. When subjected to axial pressure, the washer can undergo moderate elastic deformation. This deformation ensures the tightness of the connection without imposing excessive stress on the connected components.
In terms of material selection, wave washers are often made from high-quality metals such as spring steel and stainless steel. These materials offer excellent mechanical properties and corrosion resistance, enabling them to adapt to various harsh working environments. Surface treatments like galvanizing and blackening further enhance the washer's durability.
Regarding specifications and sizes, wave washers are available in various models, ranging from M3 to M24, meeting the needs of different bolt sizes. Custom specifications can also be manufactured based on customer requirements, highlighting their application flexibility.
Usage Methods for Wave Washers
When installing wave washers, they should be placed between the connecting component and the nut, ensuring the wavy side faces the nut. Proper installation direction allows the washer to fully utilize its elastic function, achieving optimal anti-loosening effects.
Controlling the tightening force is a critical step. Using a torque wrench to tighten according to standard torque values ensures both connection reliability and prevents over-tightening, which could lead to washer failure. It is recommended to tighten gradually in multiple steps to ensure even force distribution.
For maintenance, regularly inspecting the washer's condition is essential. If deformation or corrosion is observed, the washer should be replaced promptly. In corrosive environments, stainless steel materials or additional protective coatings can be used.
Application Scenarios for Wave Washers
In the automotive manufacturing industry, wave washers are widely used in critical areas such as engines and chassis. Their superior anti-loosening performance ensures vehicle driving safety, while their elastic properties effectively mitigate the adverse effects of vibrations.
In mechanical equipment installation, wave washers are indispensable fastening components. They can compensate for uneven connecting surfaces, evenly distribute loads, and improve equipment operational stability. Their performance is particularly notable in heavy machinery.
The aerospace industry has extremely stringent requirements for components, and wave washers have gained widespread application due to their reliability and durability. Washers made from special materials can withstand extreme temperatures and environments, ensuring flight safety.
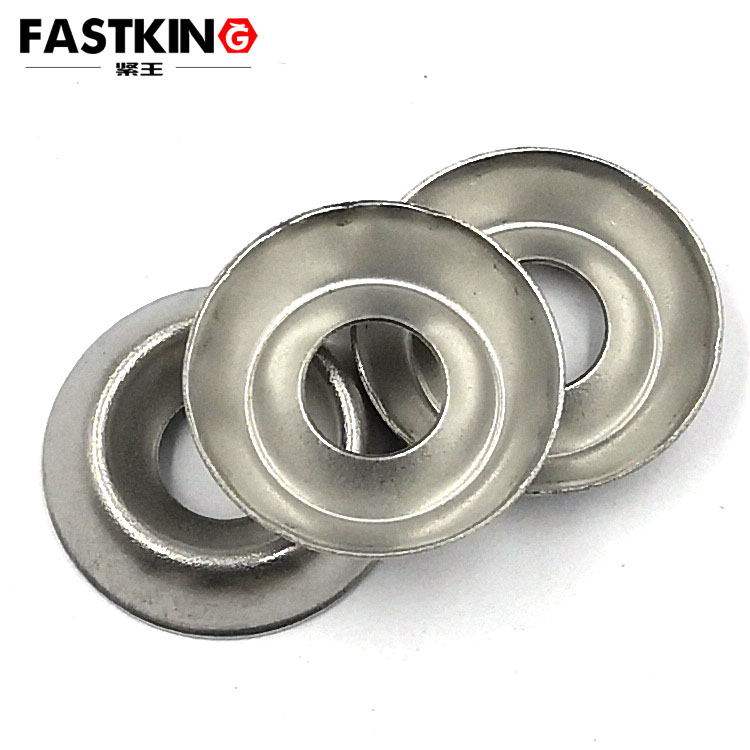
Though small, wave washers play a crucial role in modern industry. Proper use and maintenance of wave washers not only enhance equipment operational reliability but also extend equipment service life. With advancements in materials science and manufacturing technology, the performance of wave washers will continue to improve, and their application fields will further expand. In industrial production, paying attention to the selection and use of such fundamental components often yields significant results with minimal effort.