As a special type of fastener, hexagonal long nuts play a crucial role in modern mechanical assembly and construction projects. Compared to standard nuts, hexagonal long nuts feature extended thread length and larger contact area, making them excel in applications requiring higher fastening force and more stable connections. These nuts are typically manufactured from materials such as carbon steel, stainless steel, or alloy steel, often with surface treatments like zinc plating, chrome plating, or other anti-corrosion coatings to enhance durability.
Structurally, hexagonal long nuts maintain the six symmetrical flat surfaces of standard hex nuts, allowing installation and removal with conventional wrenches. The "long" characteristic primarily manifests in the nut's height, typically 1.5-3 times that of standard nuts or even longer. This elongated design not only increases thread engagement length but also creates more thread contact surfaces internally, significantly improving connection reliability and anti-loosening capability.
II. Working Principles of Hexagonal Long Nuts
Mechanical Principle Analysis
The working principle of hexagonal long nuts is based on the mechanical characteristics of threaded connections. When paired with bolts, long nuts form a screw pair through their internal threads mating with the bolt's external threads. Due to the inclined plane principle of threads, rotating the nut generates axial force that tightly compresses the connected components together. The unique aspect of hexagonal long nuts lies in their extended structure that substantially increases thread contact area.
According to the mechanical formula F=μ×N (friction force equals friction coefficient multiplied by normal force), under the same tightening torque, long nuts can provide greater axial preload. Simultaneously, the increased thread contact area means reduced load per thread, thereby decreasing stress concentration on individual threads and improving the fatigue life of the connection system. Experimental data shows that under identical material conditions, the anti-loosening capability of long nut connections is 30%-50% higher than standard nuts.
Anti-Loosening Mechanism
The anti-loosening performance represents a core advantage of hexagonal long nuts. Their anti-loosening mechanism primarily manifests in three aspects: First, the increased thread contact surfaces provide greater frictional resistance; second, long nuts allow additional locking measures such as jam nut method; third, some long nut designs incorporate asymmetric or deformed threads at the end that create elastic deformation during final tightening, forming mechanical locking.
In practical applications, when connection points experience vibration or alternating loads, standard nuts tend to gradually loosen due to microscopic sliding between threads. Long nuts, however, require more energy to make all contact points slide simultaneously because of their multiple thread contact points, thus exhibiting excellent anti-vibration loosening characteristics. This makes hexagonal long nuts ideal for vibration-intensive environments like vehicles, aerospace, and heavy machinery.
III. Typical Application Scenarios of Hexagonal Long Nuts
Heavy Industry Applications
In heavy machinery manufacturing, hexagonal long nuts are widely used for base fixation of large equipment, flange connections of pressure vessels, and critical connections in mining machinery. For instance, in column connections of large hydraulic presses, long nuts ensure connections remain secure under enormous working loads. Similarly, flange connections in wind turbine towers typically use high-strength long nuts to withstand alternating stresses and vibrations from strong winds.
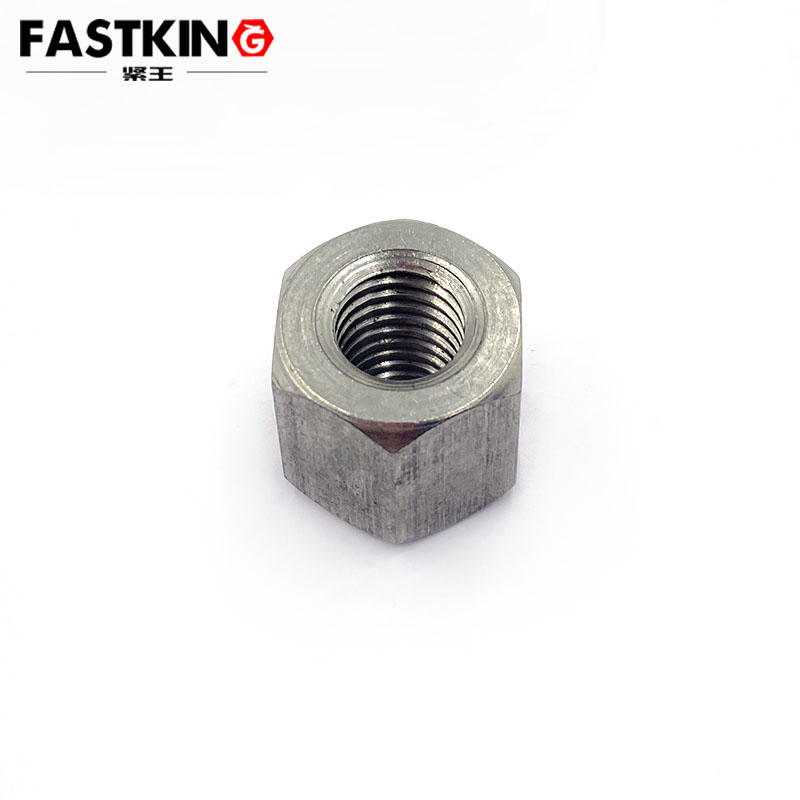
Pipeline flange connections in the petrochemical industry represent another important application. Under high-temperature and high-pressure conditions, traditional flange connections often experience preload reduction due to material creep. Using long nuts with appropriate hot-tightening processes can effectively compensate for preload loss caused by temperature changes, ensuring long-term sealing stability. Data shows that under identical conditions, flange connections using long nuts exhibit over 60% lower leakage rates than standard nut connections.
Transportation Industry Applications
The transportation sector imposes extremely high requirements on fastener reliability and safety. In railway construction, hexagonal long nuts are extensively used for rail-to-sleeper connections and switch fixation. Continuous vibrations from train operation pose significant challenges to conventional nuts, while long nuts maintain stable clamping force over extended periods thanks to their superior anti-vibration performance, greatly reducing maintenance frequency and costs.
In automotive manufacturing, hexagonal long nuts are commonly used for engine mounts, chassis critical connections, and safety-related components. Modern vehicle lightweight designs result in relatively reduced body stiffness, making vibration issues more prominent. Long nut connections can significantly improve overall NVH (Noise, Vibration, and Harshness) performance. Particularly in electric vehicles, long nuts are also used for battery pack structural fixation, ensuring connection reliability throughout the vehicle's lifecycle.
Construction and Infrastructure Applications
In high-rise buildings and large bridge construction, hexagonal long nuts are used for steel structure node connections, prestressed anchoring systems, and other critical components. For example, cable saddle fixation in cable-stayed bridges and hanger anchoring in suspension bridges all rely on high-strength long nuts. These applications require fasteners to withstand not only massive static loads but also dynamic forces from wind and seismic activity.
Building curtain wall support structures represent another typical application. Curtain wall systems must withstand various complex loads including wind pressure and thermal deformation, where connection point reliability directly impacts building safety. Long nut connections can accommodate larger installation tolerances while providing sufficient fastening force reserves. Statistics show that in typhoon-prone regions, curtain wall systems using long nuts demonstrate significantly lower damage rates than traditional connection methods.
IV. Selection and Installation Guidelines for Hexagonal Long Nuts
Selection Considerations
Proper selection of hexagonal long nuts requires evaluating multiple factors: First, determine material grade based on application - Grade 8.8 carbon steel for general use, stainless steel for corrosive environments, and Grade 10.9 or 12.9 alloy steel for high-strength requirements. Second, length selection typically recommends thread engagement length no less than 1 times the nominal diameter, extending to 1.5 times for vibration environments.
Surface treatment is another critical selection factor - zinc-plated long nuts suit most conventional environments, while coastal or chemical plant areas may require more corrosion-resistant treatments like Dacromet or hot-dip galvanizing. Additionally, for electrical insulation or galvanic corrosion prevention, nylon-coated or full stainless steel long nuts are available. Importantly, long nuts should pair with matching grade bolts to avoid premature failure from strength mismatches.
Proper Installation Methods
Installation quality directly impacts hexagonal long nut performance. First, ensure threads are clean and undamaged, repairing any damaged threads with taps or dies if necessary. During installation, applying appropriate thread locker or lubricant (like molybdenum disulfide) can reduce friction coefficient for more accurate preload while providing additional anti-loosening protection.
Torque control represents the installation cornerstone - use torque wrenches according to relevant standards or manufacturer recommendations. For critical connections, consider torque-angle method or direct tension measurement to ensure accurate preload. In high-vibration environments, double-nut locking is advisable: first tighten the long nut to specified torque, then install a standard nut on top and tighten it in reverse direction to lock both nuts together.
Regular inspection and maintenance are equally important, especially during initial operation or in environments with significant temperature fluctuations, where rechecking and retightening after operation is recommended. For long nut connections exposed to harsh environments, regular anti-corrosion treatment extends service life.
V. Conclusion
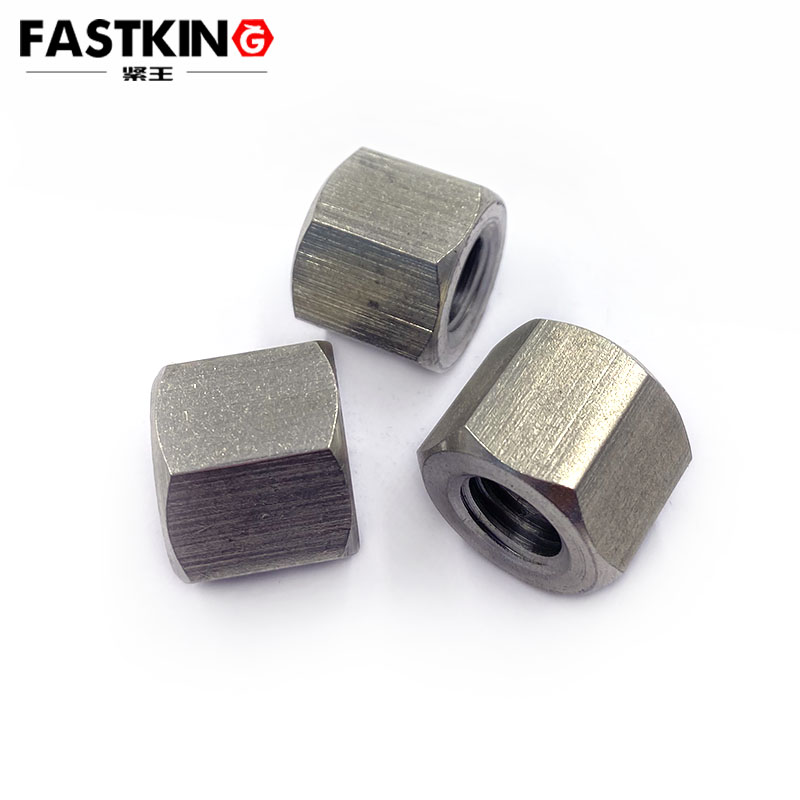
As a fastening solution developed through engineering practice, hexagonal long nuts demonstrate irreplaceable value across numerous industrial fields with their unique structural design and outstanding performance characteristics. From heavy industry to precision instruments, from ground construction to aerospace equipment, long nut applications continue expanding. With advancements in materials science and manufacturing technology, future hexagonal long nuts will evolve toward higher strength, smarter functionality, and greater environmental friendliness, providing more reliable connection solutions for modern engineering.
Understanding hexagonal long nut working principles and proper application methods is essential for engineering designers, installation technicians, and maintenance personnel. Only through appropriate selection and correct usage based on specific application scenarios can this fastener's performance advantages be fully utilized, ensuring safe and reliable operation of mechanical systems and building structures.