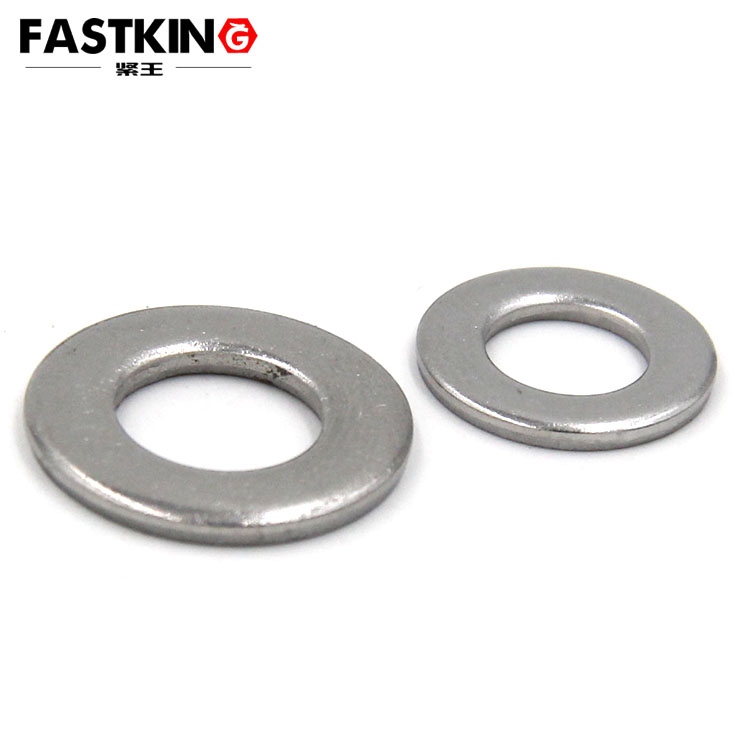
Usage and Applications of DIN 125 Flat Washers
In modern industry, DIN 125 flat washers, as standard fastener components, are widely used in various mechanical and structural connections. Their design and functionality make them a crucial element in ensuring the stability and reliability of connections. This article provides a detailed introduction to the usage methods and application scenarios of DIN 125 flat washers
Definition and Features of DIN 125 Flat Washers
(1) Definition
DIN 125 flat washers are manufactured according to the German Industrial Standard (DIN) and are primarily used between bolts or nuts and the surfaces of connected components. Their main function is to distribute the pressure from bolts or nuts over a larger contact area, thereby protecting the surface of the connected components.
(2) Features
-
Uniform Pressure Distribution: DIN 125 flat washers distribute the pressure from bolts or nuts over a larger surface area, reducing the risk of damage caused by excessive local pressure.
-
Reduced Friction: By increasing the contact area, flat washers reduce friction between the bolt and the connected component, extending service life.
-
Prevention of Loosening: The use of flat washers can reduce the risk of nut loosening caused by vibration or dynamic loads.
-
Material Diversity: DIN 125 flat washers are typically made from materials such as carbon steel and stainless steel, offering good corrosion resistance and mechanical strength
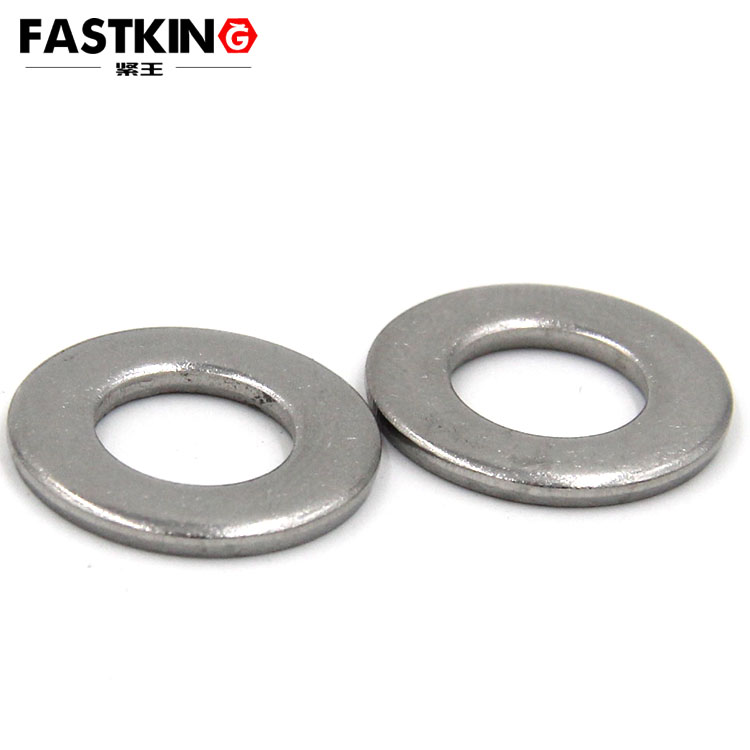
Usage Methods
(1) Tool Preparation
When installing or removing DIN 125 flat washers, appropriate tools such as wrenches or torque wrenches are required. Select the right tool based on the size of the nut or bolt to ensure stability and safety during operation.
(2) Installation Steps
-
Clean Surfaces: Before installation, ensure that the surfaces of the bolt, nut, and connected components are clean and undamaged.
-
Place Washer: Position the DIN 125 flat washer between the head of the bolt or nut and the connected component, ensuring that the washer’s hole aligns with the bolt or nut threads.
-
Tighten Nut or Bolt: Use a wrench or torque wrench to tighten the nut or bolt according to the specified torque value.
-
Inspect Connection: After tightening, check the connection for any looseness or leaks to ensure a secure fit.
(3) Removal Steps
Loosen Nut or Bolt: Use a wrench to rotate the nut or bolt counterclockwise to loosen it.
Remove Washer: Carefully remove the DIN 125 flat washer after loosening, avoiding damage to the bolt or nut threads.
Inspect Components: After removal, inspect the surfaces of the bolt, nut, and connected components for any damage, and replace if necessary.
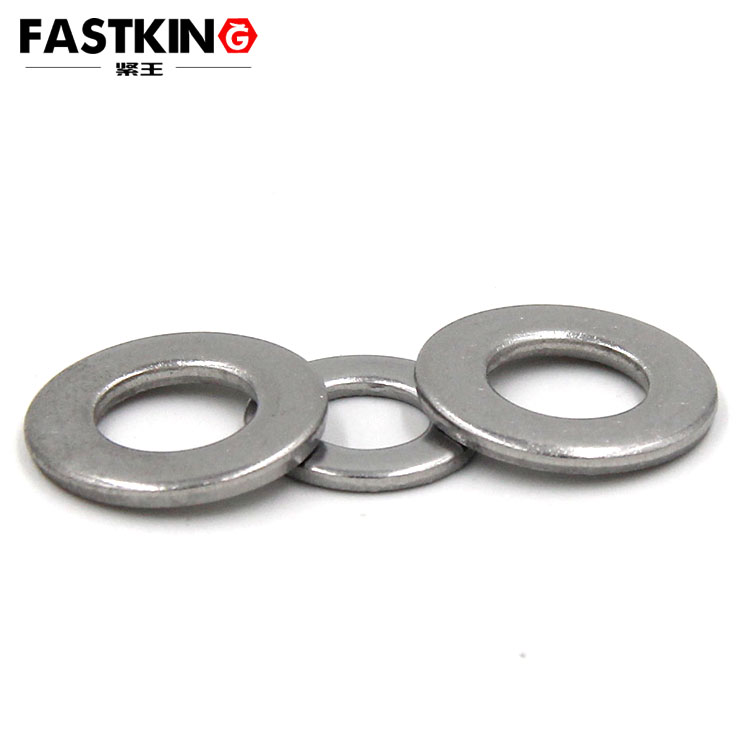
Application Scenarios
(1) Mechanical Manufacturing
DIN 125 flat washers are widely used in the mechanical manufacturing sector, such as in automobiles, construction machinery, and ships. They effectively prevent nut loosening caused by vibration, ensuring the stability and safety of equipment.
(2) Construction
In the construction field, DIN 125 flat washers are used to fasten structural components of buildings, bridges, and roads. Their high strength and durability ensure stability in harsh environments.
(3) Electronic Devices
In the manufacturing of electronic devices, DIN 125 flat washers are used to fasten circuit boards and sockets. Their compact design and locking performance make them suitable for use in tight spaces.
(4) Petrochemical Industry
In the petrochemical industry, DIN 125 flat washers are used to secure critical components, ensuring the stability and safety of equipment in high-temperature and high-pressure environments.
(5) Rail Transportation
In rail transportation, DIN 125 flat washers are used to fasten wheels, bogies, and other critical components of rail vehicles, ensuring stability and safety during operation.
Summary
Due to their ability to distribute pressure uniformly, reduce friction, prevent loosening, and offer material diversity, DIN 125 flat washers have become indispensable fastener components in the fields of mechanical manufacturing, construction, electronic devices, and petrochemicals. Proper installation and removal methods, along with adaptability to working environments, significantly enhance the stability and reliability of equipment.