Semi-tubular rivets have become an indispensable fastening element in modern industry, thanks to their lightweight design, high strength, ease of installation, and excellent sealing and corrosion resistance. These rivets are widely used in various fields, including aerospace, automotive manufacturing, and electronics, providing efficient and reliable connection solutions. As technology continues to advance, the application scope of semi-tubular rivets will further expand, bringing more convenience and benefits to industrial manufacturing.
Semi-tubular rivets are suitable for connecting various materials and structures, particularly excelling in the following areas:
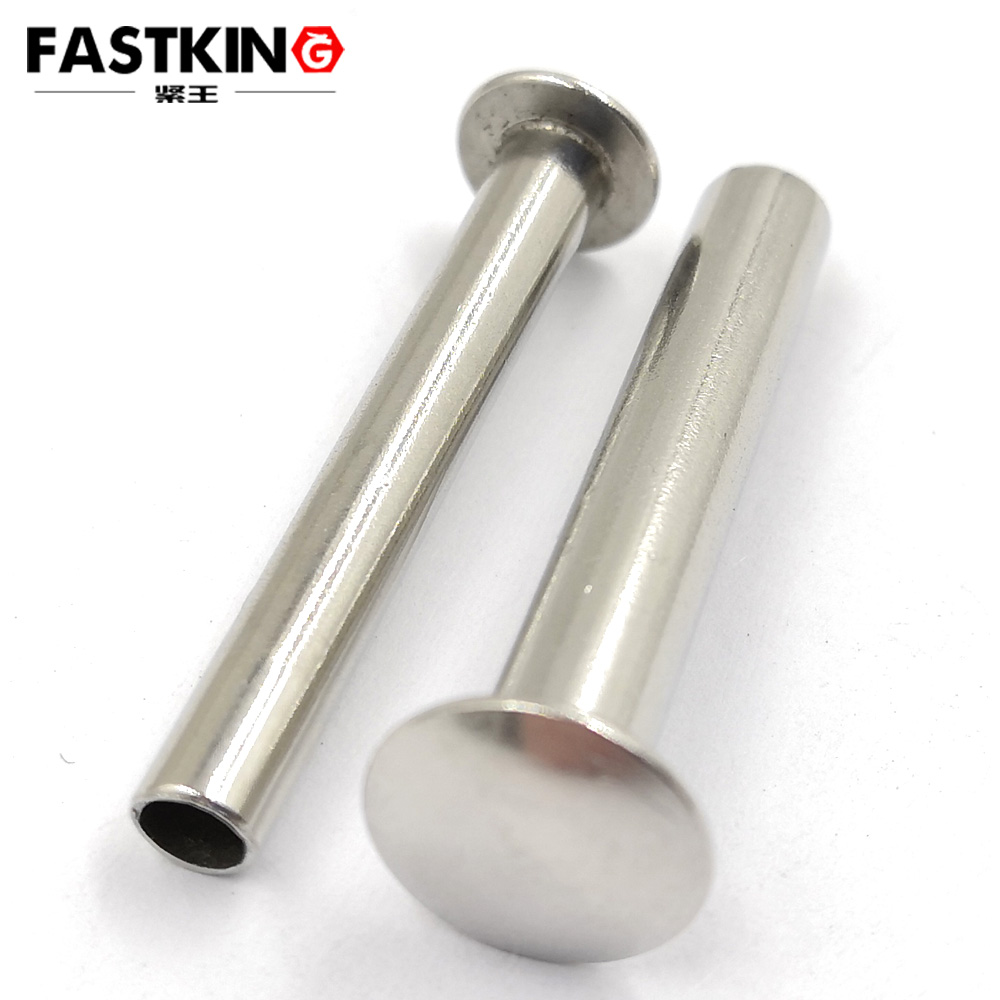
1. Aerospace Industry
Semi-tubular rivets are widely used in aerospace structural components due to their lightweight and high-strength characteristics. They are employed in the assembly of wings, fuselage frames, and internal components, where they can withstand high vibrations and dynamic loads while reducing structural weight.
2. Automotive Manufacturing
In the automotive industry, semi-tubular rivets are commonly used for assembling body parts, braking systems, and seat structures. Their vibration resistance and durability ensure stability in complex mechanical environments.
3. Electronics
Semi-tubular rivets are used to secure electronic device casings and circuit boards. Their lightweight design and excellent sealing properties prevent dust and moisture ingress, extending the life of electronic equipment.
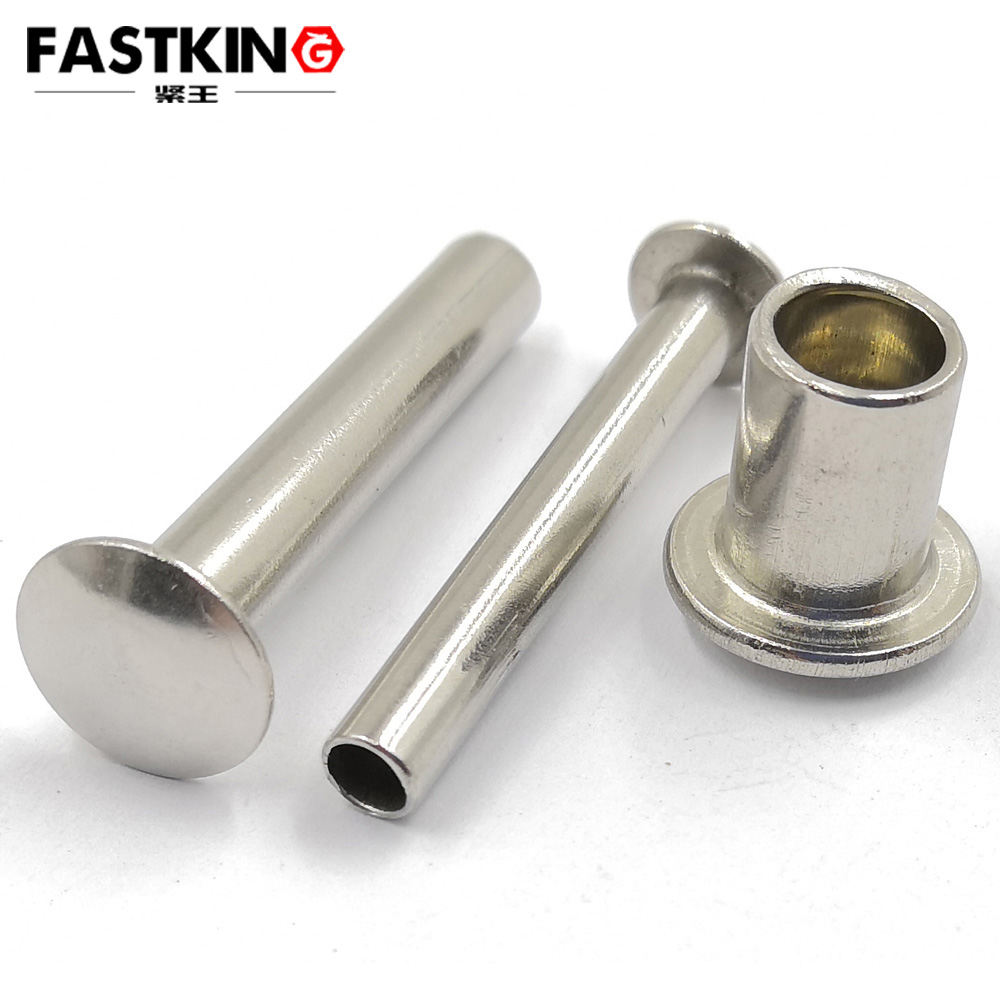
4. Furniture Manufacturing
In the furniture industry, semi-tubular rivets are used to connect wooden or metal components, providing robust structural support while maintaining a neat appearance.
5. Lightweight Metal and Plastic Connections
Semi-tubular rivets are also suitable for connecting lightweight metals and plastics without the need for pre-drilled holes, simplifying the assembly process.
Assembly Methods
The assembly process of semi-tubular rivets is simple and efficient, typically involving the following steps:
1. Preparation of Tools
Specialized riveting tools, such as rivet guns or manual riveting tools, are required.
2. Installation of Rivets
Insert the semi-tubular rivet into the hole of the components to be connected, ensuring a tight fit between the rivet and the hole.
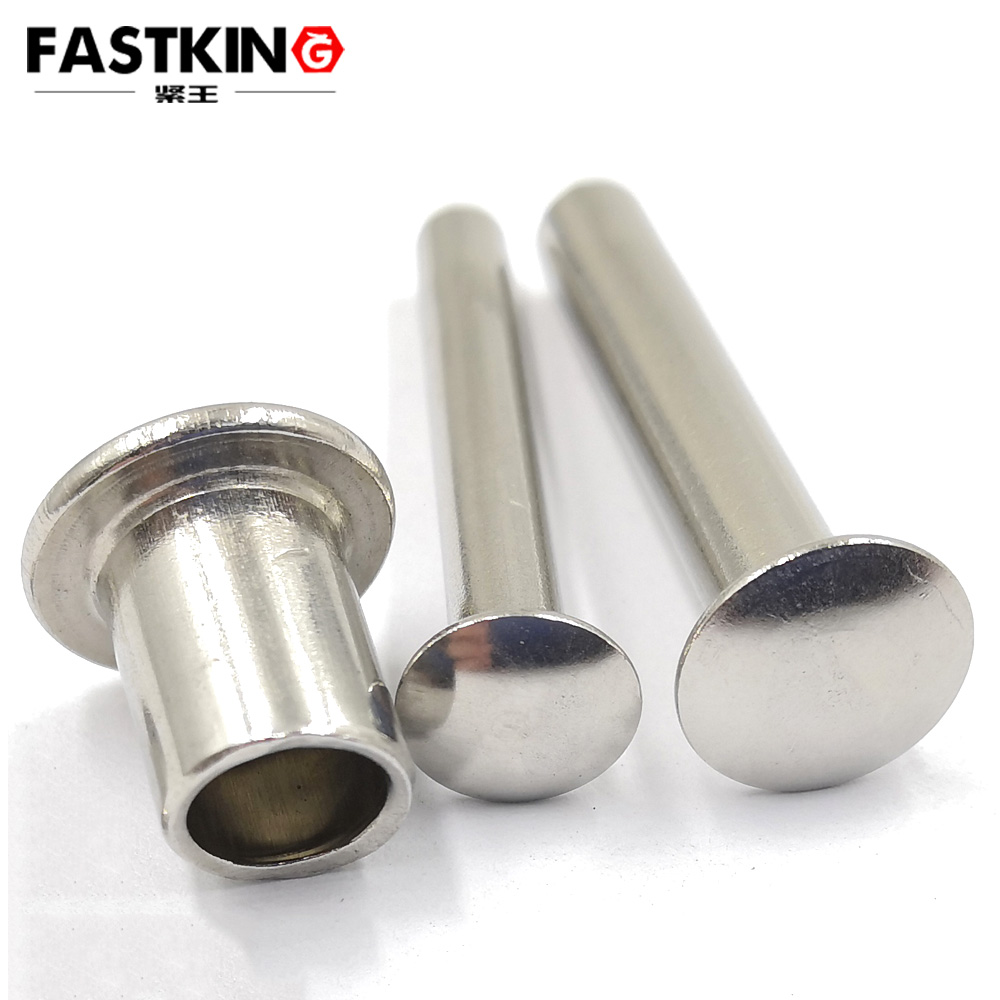
3. Riveting Operation
Use the riveting tool to apply pressure to the rivet, causing the hollow part of the rivet to deform and fill the hole, forming a secure connection. Depending on the application, "roll-over riveting" or "crimping" methods can be chosen.
4. Inspection of Connection
After riveting, inspect the connection to ensure it is secure and that the rivet head is tightly fitted against the component surface.
Advantages
Compared to traditional solid rivets, semi-tubular rivets offer several significant advantages:
1. Lightweight Design
With a hollow interior, semi-tubular rivets are lighter in weight, making them ideal for applications where weight is a critical factor, such as in aerospace and automotive manufacturing.
2. High Strength and Durability
The "mushroom head" structure formed after riveting effectively distributes stress, providing high tensile and shear strength.
3. Cost Savings
The manufacturing process for semi-tubular rivets is simpler, and they use less material, reducing production costs.
4. Ease of Installation
The assembly process is quick and straightforward, eliminating the need for pre-drilling holes and reducing assembly time and labor costs.
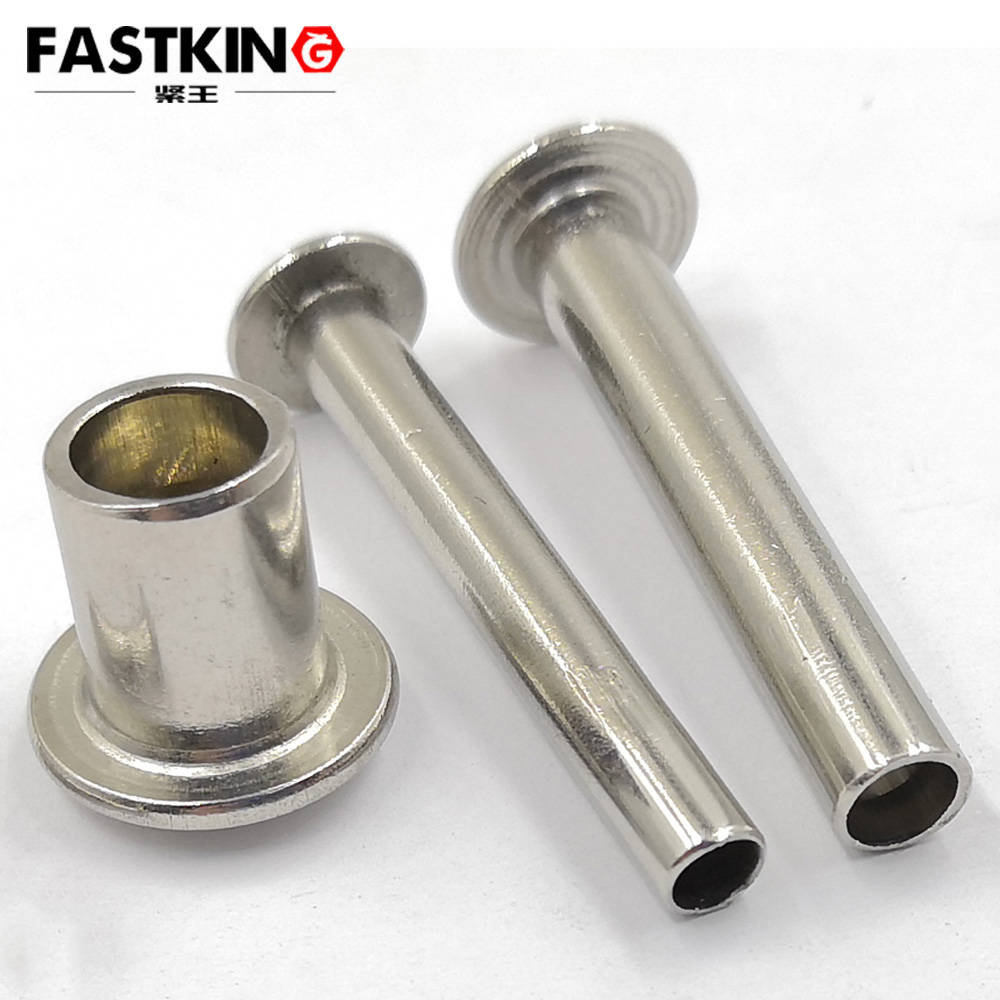
5. Excellent Sealing Performance
Semi-tubular rivets create a tight seal after riveting, preventing the leakage of liquids and gases. They are suitable for applications requiring high levels of waterproofing and dustproofing.
6. Corrosion Resistance
Typically made from corrosion-resistant materials such as stainless steel or aluminum alloy, semi-tubular rivets can withstand harsh environments and maintain long-term performance.
7. Aesthetic Appeal
The smooth head design of semi-tubular rivets provides a neat and tidy appearance, making them suitable for applications where aesthetics are important.
Conclusion
Semi-tubular rivets have become a preferred fastening solution in modern industry due to their lightweight, high-strength, and easy-to-install characteristics. Their excellent sealing and corrosion resistance make them suitable for a wide range of applications, from aerospace and automotive manufacturing to electronics and furniture. As technology continues to evolve, the use of semi-tubular rivets will likely expand further, offering more convenience and benefits to industrial manufacturing processes.