Locking Nuts: A Reliable Fastening Solution for High-Efficiency Anti-Loosening
Locking nuts are specialized anti-loosening fasteners that play a crucial role in industries such as aerospace, automotive manufacturing, and rail transit. These nuts prevent loosening due to vibration through the continuous pre-tension generated by their elastic deformation. Made from high-quality spring steel or stainless steel, locking nuts are designed to provide reliable and durable fastening solutions in demanding applications.
Core Advantages of Locking Nuts
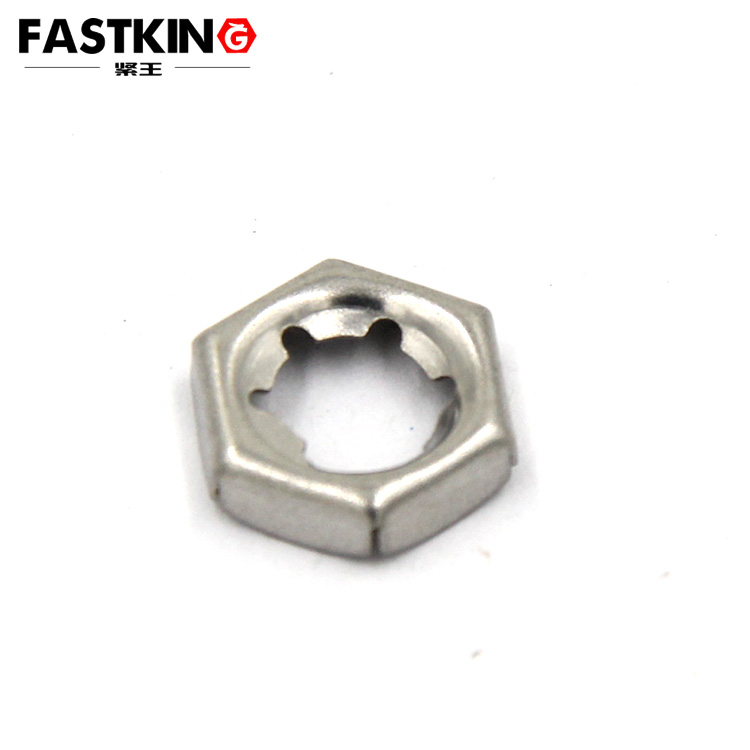
Locking nuts are manufactured from high-quality spring steel or stainless steel, undergoing precision stamping and heat treatment processes to achieve excellent elastic properties and fatigue resistance. With a hardness of HRC42-48, these nuts offer sufficient strength and durability. Their unique non-circular design generates elastic deformation during fastening, creating a continuous anti-loosening force.
In terms of mechanical performance, locking nuts support a maximum strength grade of 10, meeting the fastening requirements of most high-demand applications. Tested for anti-loosening capabilities, these nuts can withstand over 2000 vibration cycles without loosening, significantly outperforming standard fasteners.
The nuts feature a standard hexagonal shape, allowing for easy operation with a common wrench. The unique elastic deformation design effectively prevents loosening caused by vibration, enhancing safety during use. Standardized thread specifications and dimensions ensure good interchangeability and compatibility.
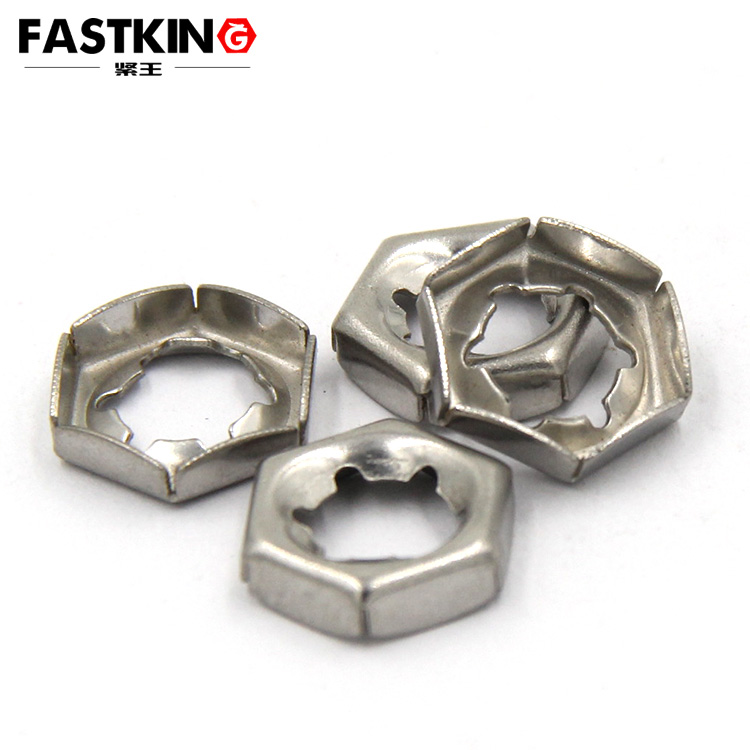
Proper Use of Locking Nuts
When installing locking nuts, ensure that the threads are clean and undamaged. Use an appropriate wrench for installation, avoiding excessive pre-tightening force. Pay attention to the nut's orientation, ensuring the deforming part faces the fastened component. During tightening, follow the specified torque values to prevent over-tightening, which could lead to elastic failure.
For routine maintenance, regularly inspect the nut's fastening status and retighten if necessary. Check the threads and deformed parts for any damage, and replace the nut promptly if any issues are found. When storing, keep the nuts in a dry, ventilated area, avoiding direct sunlight and chemical corrosion.
Common issues include elastic failure and thread damage. These can be identified by visual inspection and checking the fastening status. Damaged nuts should be replaced promptly to avoid compromising equipment operation.
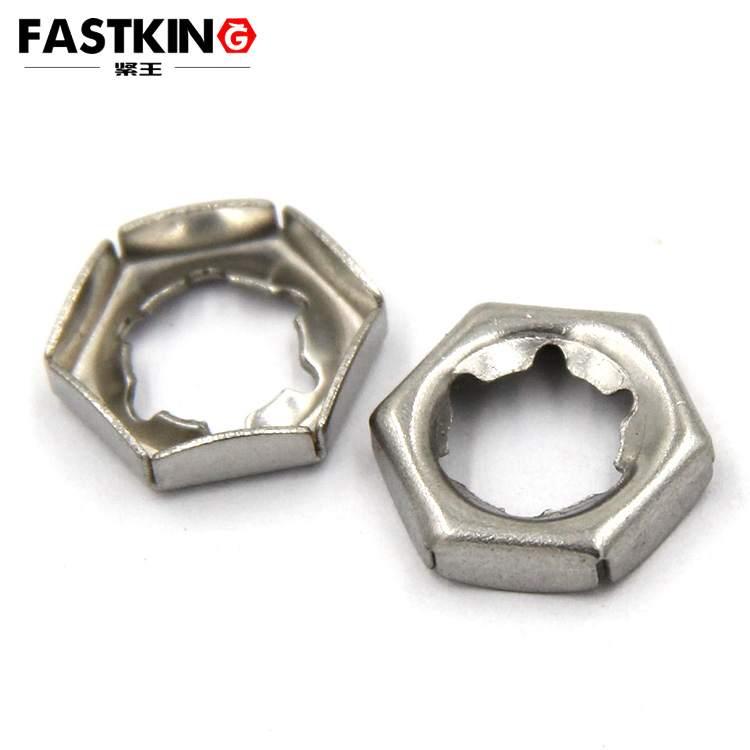
Typical Applications of Locking Nuts
In the aerospace industry, locking nuts are widely used for fastening connections in engines, airframe structures, and avionics equipment. Their reliable anti-loosening performance ensures flight safety. In automotive manufacturing, they are commonly used in critical areas such as chassis, suspension systems, and powertrains, meeting the demands of vibrating environments in vehicles.
In rail transit systems, locking nuts are used for fastening connections in bogies, car body joints, and signaling equipment, ensuring the safe operation of trains. In the field of construction machinery, they are applied in hydraulic systems, transmission systems, and working devices, providing reliability for equipment operation.
Conclusion
Locking nuts have become a benchmark in the anti-loosening fastener field due to their outstanding performance and broad applicability. As high-end manufacturing continues to evolve, locking nuts will play a crucial role in emerging sectors such as aerospace and new energy vehicles, providing a solid guarantee for reliable fastening solutions.