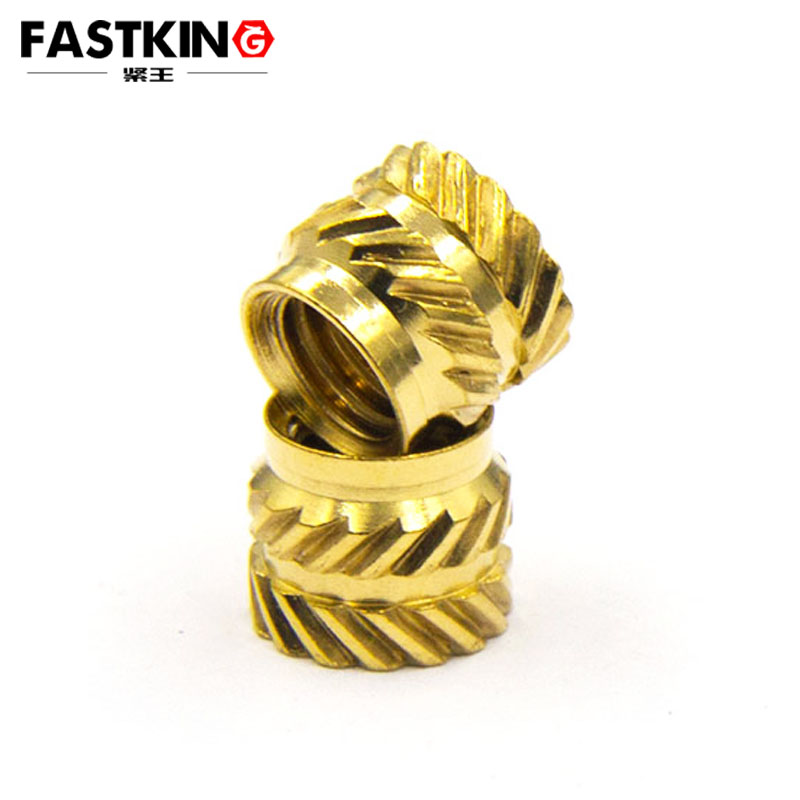
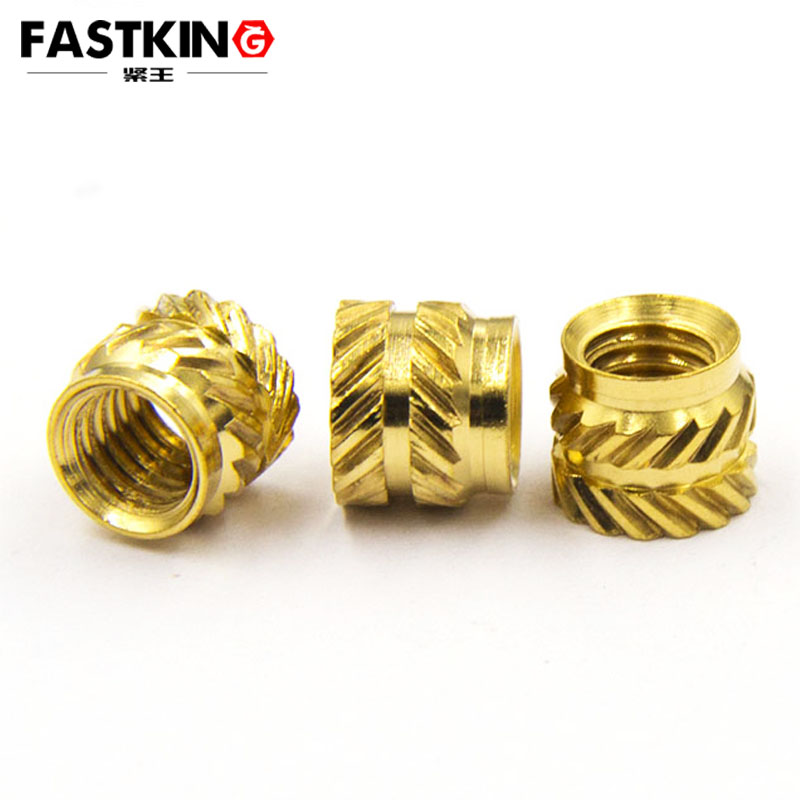
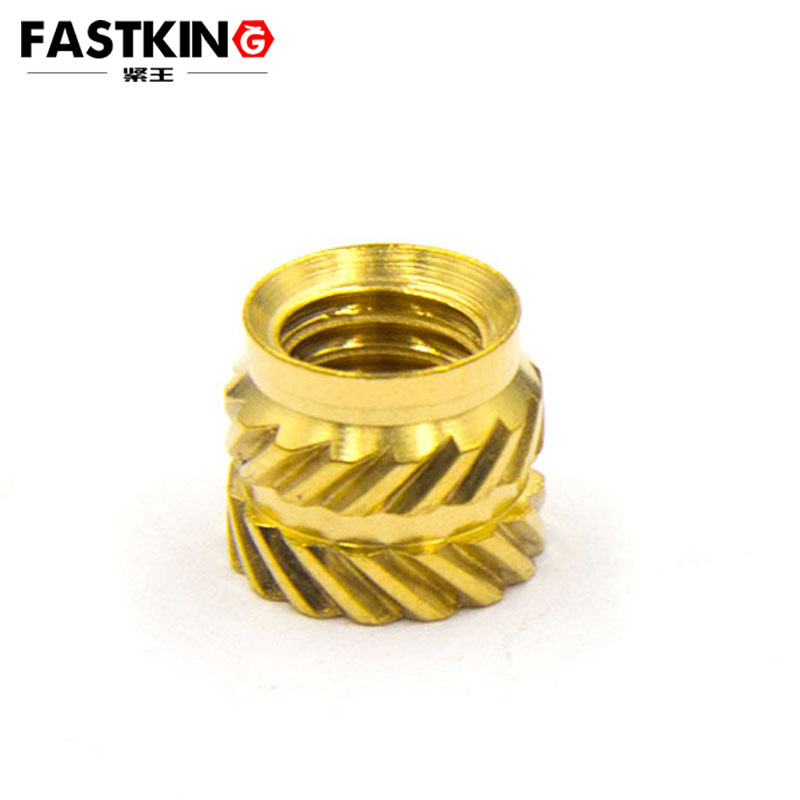
Title: Hot-melt Brass Insert Nuts: An Innovative Solution for Industrial Connections
In the modern industrial manufacturing sector, fasteners serve as indispensable elements in mechanical structures, with their performance and reliability directly impacting the safety and efficiency of entire systems. Hot-melt brass insert nuts, as an advanced connector that combines efficiency, stability, and corrosion resistance, are increasingly becoming the preferred choice in numerous industries. This article delves into the characteristics, application advantages, and significant role of hot-melt brass insert nuts in the industrial field.
I. Overview of Hot-melt Brass Insert Nuts
Hot-melt brass insert nuts, as the name suggests, are special fasteners that embed brass nuts into plastic or other non-metallic substrates using hot-melt technology. This process involves heating the nut to a semi-molten state at high temperatures and then rapidly pressing it into a pre-drilled hole. Upon cooling and solidification, the nut forms a secure mechanical bond with the substrate. The choice of brass material not only imparts excellent electrical conductivity, thermal conductivity, and corrosion resistance to the nut but also ensures good mechanical strength and an aesthetically pleasing appearance.
II. Key Features
- High-strength Connections: The hot-melt embedding technology ensures a tight bond between the nut and the substrate, providing higher tensile and shear strengths than traditional threaded connections. This effectively resists vibration and impact, extending the service life.
- Corrosion Resistance: Brass material inherently possesses good corrosion resistance, maintaining stable performance in damp and corrosive environments, making it suitable for outdoor and harsh conditions.
- Lightweight Design: The embedding method allows for weight reduction without compromising strength, aligning with modern industrial trends towards lightweight and energy-efficient designs.
- Easy Installation: Once the insert nut is installed, external operations can easily tighten or loosen it using standard tools, simplifying the assembly process and enhancing production efficiency.
- Design Flexibility: Hot-melt embedding technology permits flexible placement of nuts on components with complex shapes and sizes, meeting diverse design requirements.
III. Application Areas
Hot-melt brass insert nuts are widely used in various fields such as automobile manufacturing, electronics and electrical appliances, communication equipment, medical devices, and aerospace. In the automotive industry, they are employed in critical areas like the engine compartment and body structural parts, ensuring vehicle safety and reliability. In the electronics and electrical sector, they are commonly used for circuit board fixation and enclosure assembly, guaranteeing stable operation of electronic devices. Moreover, in the aerospace industry, their lightweight and high-strength, corrosion-resistant characteristics are indispensable.
IV. Conclusion
Hot-melt brass insert nuts have become an essential component of modern industrial connection technology due to their unique technical advantages and broad application prospects. As material science and manufacturing technology continue to advance, hot-melt embedding technology will also innovate continually, providing more industries with more efficient and reliable connection solutions. In the future, hot-melt brass insert nuts will play an even more crucial role in promoting industrial upgrading and driving intelligent manufacturing, contributing to safer, more efficient, and environmentally friendly industrial production environments.