Structural Features of Low-Profile Hexagon Fine-Thread Nuts
A low-profile hexagon fine-thread nut is characterized by its reduced height, compact hexagonal head, and high thread density. Compared to standard nuts, its key features include:
Low-Profile Design: The nut height is only 1/2 to 2/3 that of a standard nut, making it suitable for confined installation spaces.
Fine-Thread Pitch: The thread pitch is smaller (e.g., 0.5mm for M6 fine-thread vs. 1mm for standard thread), increasing the number of threads per unit length and enhancing engagement area.
Optimized Hexagonal Head: The reduced width across flats allows for use with thin wrenches or sockets, minimizing the required operational space.
This structure ensures high-strength fastening while offering advantages such as lightweight construction, vibration resistance, and superior spatial adaptability.
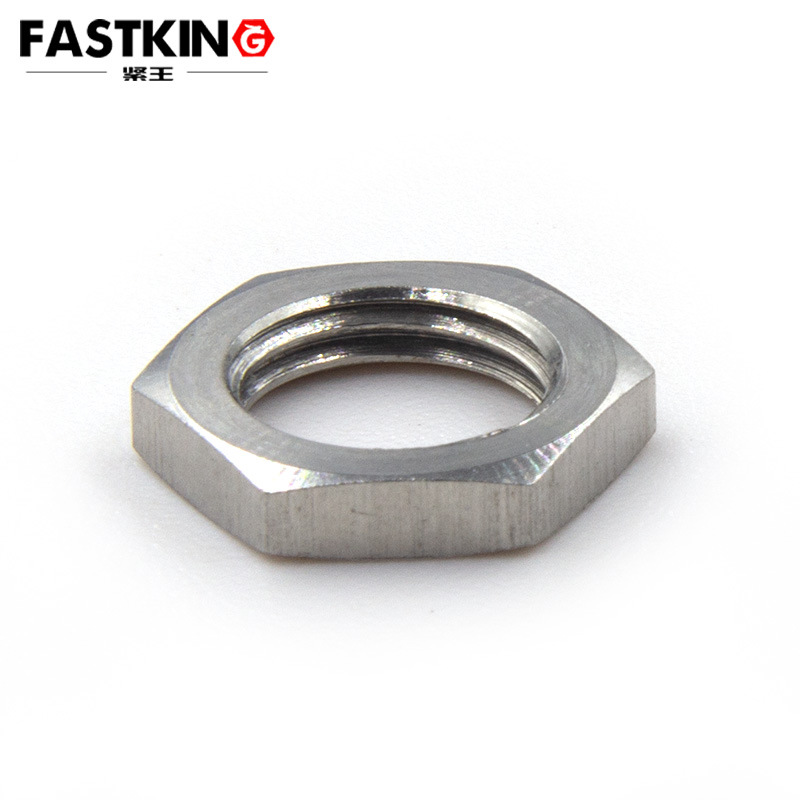
Working Principles and Technical Advantages
The functionality of low-profile hexagon fine-thread nuts relies on the synergy between their structure and material properties, manifesting in the following aspects:
High Preload and Anti-Loosening Performance
The increased contact area of fine threads enhances inter-thread friction. Under the same preload, fine-thread nuts distribute axial loads more evenly, effectively resisting loosening caused by vibration or cyclic loading. For example, in high-vibration environments like automotive engines, standard nuts may fail due to thread slippage, while fine-thread nuts extend fastener lifespan by increasing the number of engagement points.
Space Adaptability
The low-profile design makes these nuts ideal for tight spaces, such as internal structures of electronic devices or precision instrument housings. For instance, drones often use these nuts to secure circuit boards to their shells, saving space while maintaining structural integrity.
Fatigue and Shear Resistance
Fine threads exhibit lower stress concentration, and the reduced height decreases the moment arm length, enhancing shear strength under transverse loads. In rail fastening systems, these nuts mitigate fatigue fracture risks caused by frequent impacts.
Enhanced Sealing Performance
The tight thread engagement improves sealing effectiveness, especially when used with gaskets, preventing fluid or gas leakage. These nuts are widely used in hydraulic fittings and pressure vessel flanges.
Typical Application Scenarios
Precision Instruments and Electronics
In optical devices, medical equipment (e.g., endoscopes, CT scanners), and consumer electronics (e.g., smartphones, laptops), these nuts secure micro-sensors, PCBs, or precision gears. Their low profile avoids interference with internal components, while fine threads ensure long-term stability.
Aerospace Industry
Applications like aircraft engine blade fastening and satellite bracket connections demand lightweight and highly reliable fasteners. These nuts reduce overall weight while leveraging fine threads’ vibration resistance to ensure safety in extreme conditions.
Automotive Engineering
In engine blocks, transmission housings, and EV battery packs, fine-thread nuts secure high-vibration components. For example, hundreds of such nuts may be used in an electric vehicle’s battery module to prevent loosening from charge-discharge cycles.
Rail Transit and Heavy Machinery
High-speed train bogies and construction machinery hydraulic systems subject nuts to frequent impacts and dynamic loads. Fine threads distribute stress, while the low-profile head accommodates complex installations.
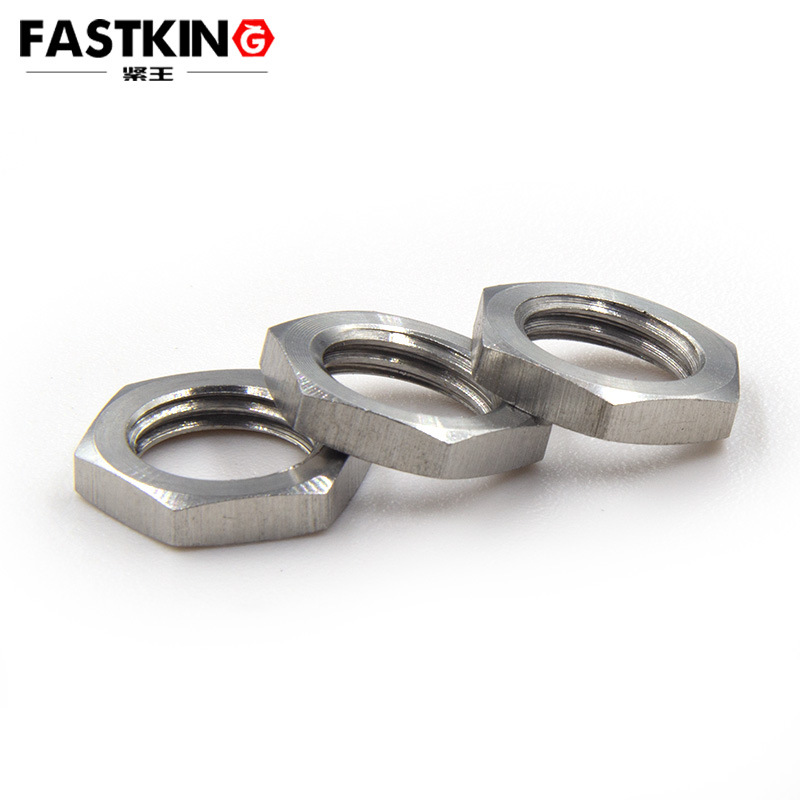
Harsh Environments
In high-temperature (e.g., boiler pipelines) or corrosive (e.g., chemical equipment) settings, stainless steel or superalloy variants of these nuts provide corrosion resistance and structural reliability.
Installation and Maintenance Guidelines
Tool Compatibility
Use thin-wall sockets or specialized wrenches to prevent slippage. For M4 fine-thread nuts, a socket with ≤3mm wall thickness is recommended.
Fine threads are sensitive to over-tightening. Use a torque wrench and adhere to standards like ISO 898-2. Excessive torque may strip threads, while insufficient torque compromises preload.
Component Matching
Pair with bolts of equivalent precision (e.g., 6H/6g thread tolerance). Clean threads before installation to avoid contamination.
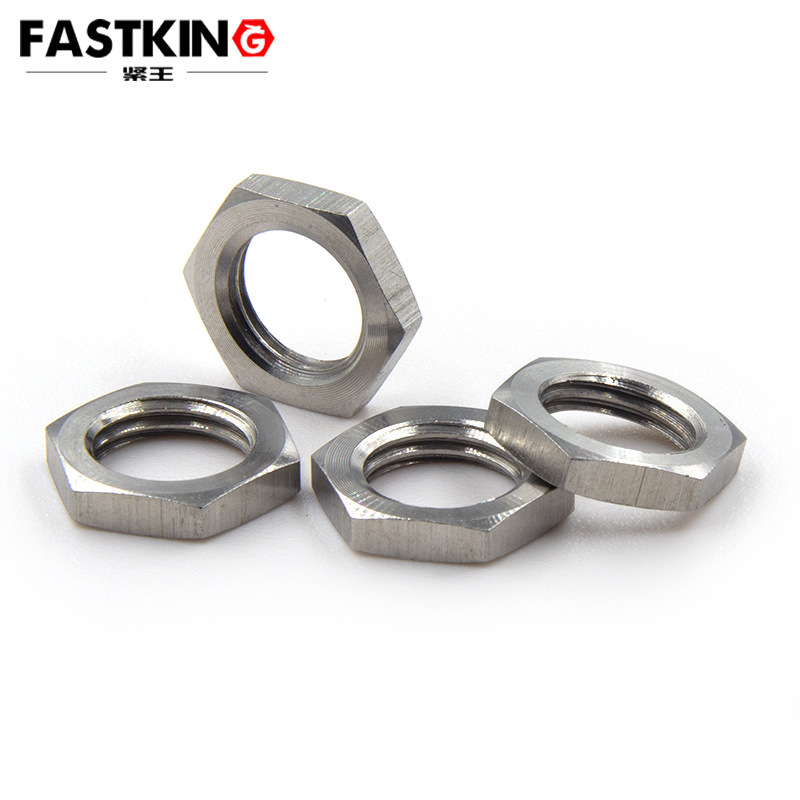
Anti-Loosening Measures
In extreme vibration environments, combine with spring washers or threadlockers (e.g., Loctite 243) for added security.
Conclusion
Low-profile hexagon fine-thread nuts address the limitations of traditional fasteners in space constraints, vibration resistance, and weight reduction through structural innovation and precision manufacturing. From microelectronics to heavy industrial equipment, their applications continue to expand, solidifying their role as critical components in modern engineering. Future advancements in materials (e.g., titanium alloys, composites) and surface treatments (e.g., Dacromet coating) will further extend their performance limits, meeting increasingly complex engineering demands.