Taper pins with screw ends are specialized fasteners composed of a tapered pin body and a threaded end. This unique design makes them indispensable in mechanical assembly. The tapered section ensures precise positioning, while the threaded part provides reliable fastening force. The combination of these features makes taper pins with screw ends crucial components in mechanical assembly.
I. Correct Usage of Taper Pins with Screw Ends
When installing taper pins with screw ends, it is essential to ensure that the pin holes are clean and free of debris. Use specialized installation tools to press the pin into the hole until the threaded section is fully exposed. During installation, control the force applied to avoid damaging the surface of the components. For workpieces made of different materials, select taper pins with screw ends of corresponding hardness to ensure assembly quality.
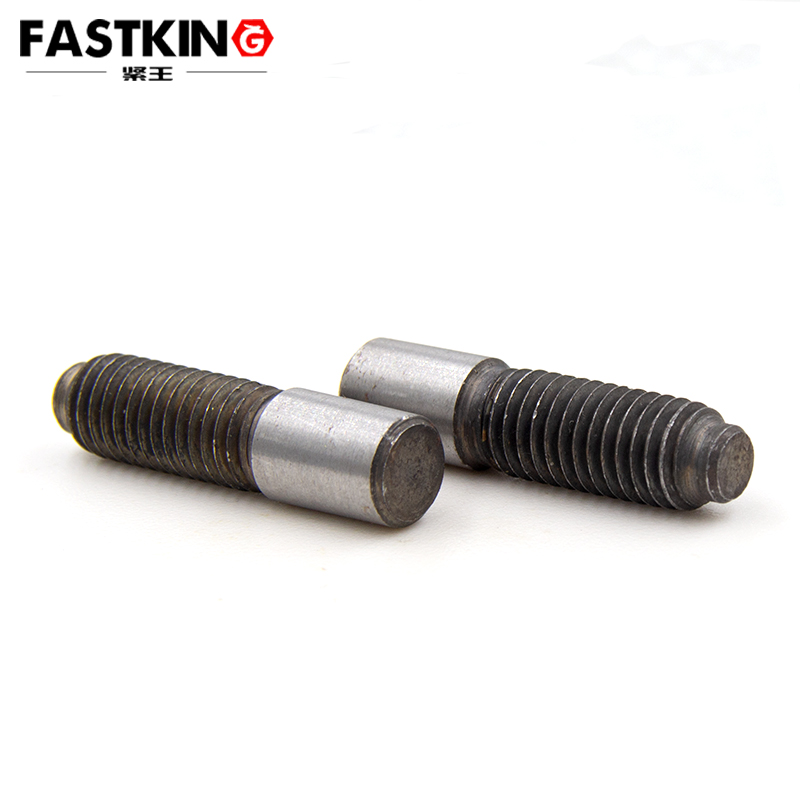
For removal, a specialized pin extractor is required. Screw the threaded end of the extractor into the pin's tail, then apply even force to pull it out. Avoid using excessive force or hammering, as this may damage the workpiece or cause safety hazards.
In terms of maintenance, regularly check the tightness of the pins and replace any that show signs of wear promptly. Store the pins in a dry environment to prevent rust, which could affect their performance.
II. Typical Application Scenarios of Taper Pins with Screw Ends
In the field of mechanical manufacturing, taper pins with screw ends are widely used in the assembly of precision equipment such as machine tools and molds. They effectively ensure the positioning accuracy of components and improve the operational stability of equipment. For example, in the assembly of CNC machine tool spindles, taper pins with screw ends ensure precise alignment between the spindle and the housing.
In the automotive industry, taper pins with screw ends play a significant role in the assembly of critical components such as engines and transmissions. They not only provide precise positioning but also withstand significant vibration and impact loads, ensuring vehicle safety.
In the aerospace sector, the application of taper pins with screw ends is even more stringent. They are used in critical areas such as aircraft engines and landing gear, where they must meet extremely high reliability and durability requirements.
III. Technical Advantages of Taper Pins with Screw Ends
Taper pins with screw ends offer excellent positioning accuracy. Their tapered design allows for micron-level precision, meeting the requirements of precision assembly. At the same time, the threaded section provides reliable fastening force, effectively preventing component loosening.
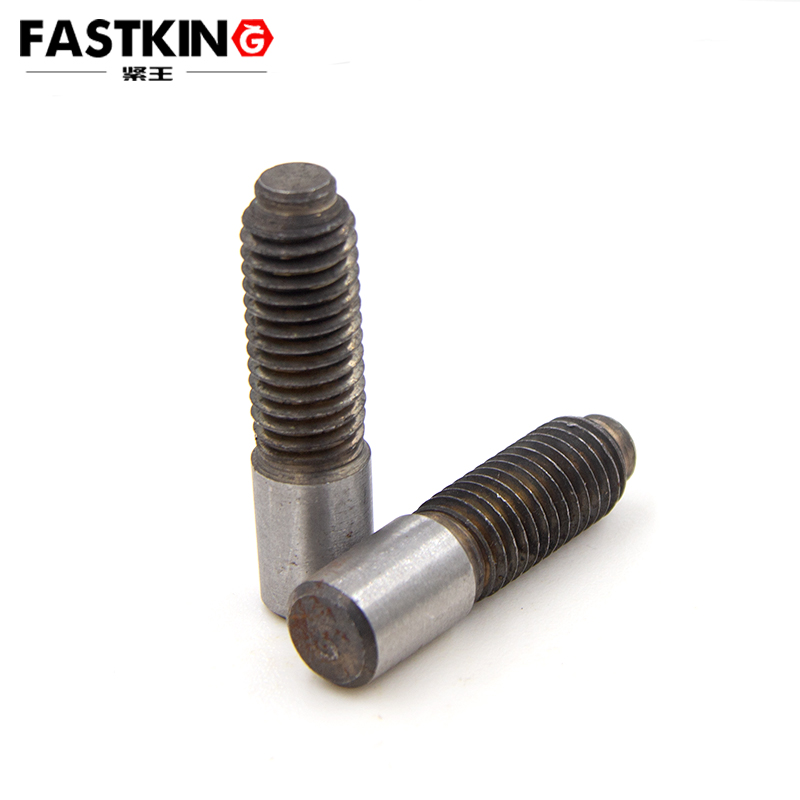
In terms of load-bearing capacity, taper pins with screw ends can simultaneously withstand radial and axial loads, exhibiting excellent shear resistance. This characteristic ensures stable connection performance even in vibrating environments.
Reusability is another significant advantage of taper pins with screw ends. Through specialized heat treatment processes, these pins achieve high hardness and wear resistance, allowing for multiple installations and removals without compromising performance.
Although small, taper pins with screw ends play a vital role in modern mechanical manufacturing. As manufacturing technology advances, the performance of these pins will continue to improve, and their application scope will expand further. Proper use and maintenance of taper pins with screw ends not only enhance assembly quality but also extend the service life of equipment, contributing significantly to the advancement of the manufacturing industry.