Flange nylon lock nuts represent a specialized fastening component that combines the benefits of a flange surface with nylon locking functionality, playing an indispensable role in modern industrial assembly. These nuts incorporate a nylon ring or insert within the threaded portion, utilizing the elastic deformation properties of nylon material to achieve reliable vibration resistance, while the flange design provides increased contact area for more even load distribution and protection of connected surfaces.
Compared to conventional nuts, flange nylon lock nuts offer three significant advantages: First, superior vibration resistance that effectively withstands shock and impact; second, the flange design reduces surface pressure on connected components; third, convenient installation without requiring additional lock washers or adhesives. These characteristics make them ideal for automotive, aerospace, and mechanical equipment applications.
Primary Application Scenarios for Flange Nylon Lock Nuts
Automotive Manufacturing Industry
In automotive applications, flange nylon lock nuts are widely used in engine systems, transmission components, and chassis parts. The high-temperature, high-pressure environment of engines presents severe challenges for fasteners, with these nuts capable of withstanding operating temperatures up to 120°C while maintaining secure fastening under engine vibration conditions. Transmission and driveshaft connections benefit from their ability to prevent lubricant leakage, while chassis suspension systems effectively absorb road impact and vibration.
Rail Transportation Sector
High-speed rail and subway systems demand exceptional safety standards, where flange nylon lock nuts play critical roles in car body connections, bogie assembly, and track fastening. Continuous vibration and alternating loads during operation can loosen standard nuts, while the nylon locking mechanism provides durable vibration resistance. Particularly in track fastening systems, the flange design prevents micro-motion wear between rails and baseplates, extending track service life.
. Mechanical Equipment Manufacturing
Industrial machinery such as printing presses, textile equipment, and packaging machines operate under constant vibration, where flange nylon lock nuts maintain consistent clamping force. Critical components like bearing fixation and gearbox assembly in heavy machinery utilize these nuts to prevent precision loss or part damage from loosening. For equipment requiring frequent maintenance, their reusability (typically over 10 cycles) significantly reduces maintenance costs.
Electronics and Electrical Appliances
High-end electronic devices and household appliances employ these nuts for securing circuit boards, motors, and enclosures. Their non-conductive properties prevent signal interference while resisting connection failure from transport or operational vibration. Vibration-prone components like air conditioner compressors and washing machine drums particularly benefit from their pressure-distributing flange design that prevents thin metal casing deformation.
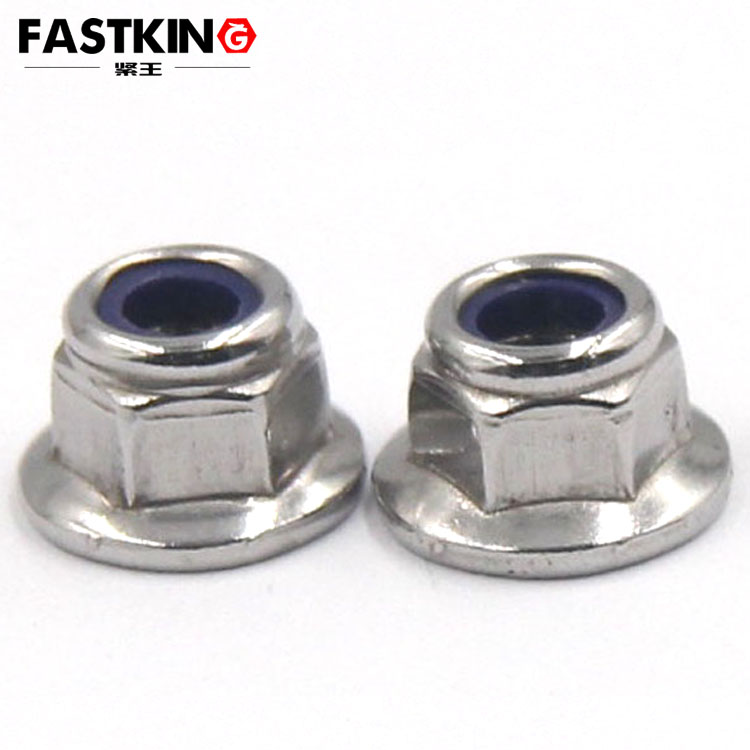
Construction and Steel Structures
In curtain wall installation, steel structure connections, and piping systems, these nuts address loosening caused by wind loads and thermal expansion. High-rise building steel joints benefit from both connection strength and micro-motion fatigue resistance. Pipe flange connections utilize the nylon locking feature to compensate for preload loss from thermal cycling, preventing medium leakage.
Proper Usage Methods for Flange Nylon Lock Nuts
Pre-installation Preparation
Selecting the appropriate nut requires consideration of thread specifications (e.g., M6, M8), flange diameter, nylon ring position (top or middle), and material (typically carbon steel or stainless steel). Inspect threads for damage and clean surfaces of oil and debris. For stainless steel, molybdenum-based lubricant can reduce galling risk.
Tool selection critically impacts results—calibrated torque wrenches are recommended. For batch installation, pneumatic/electric tools should have torque control. Socket size must match the flange dimensions to prevent slippage and damage.
Standard Installation Procedure
First, insert the bolt through the connection hole, ensuring sufficient thread protrusion (minimum 1-2 pitches beyond the nut). Hand-thread the nut several turns to verify smooth engagement, avoiding cross-threading which permanently damages the nylon insert.
Using a torque wrench, tighten in stages: 30% → 70% → 100% of target torque. Typical values: M6≈8-10Nm, M8≈18-22Nm, M10≈35-40Nm (varies by bolt grade). Orient the flange against the workpiece with nylon ring facing bolt end. For through-holes, add flat washers for better load distribution. Stop immediately if abnormal resistance occurs.
Special Condition Techniques
For high-temperature environments, select heat-resistant nylon (e.g., PA66) or pre-treat rings at 150°C. Pre-soaking in hot water (2-3 minutes) softens the nylon for easier initial assembly.
In corrosive environments, prioritize stainless steel (A2-70/A4-80). Extreme conditions may require special coatings/alloys. Regularly inspect for nylon ring cracking.
For frequent disassembly, track usage cycles (typically ≤10-15). When wear or reduced locking force appears, replace immediately. For reused nuts, increase torque 10-15% to compensate.
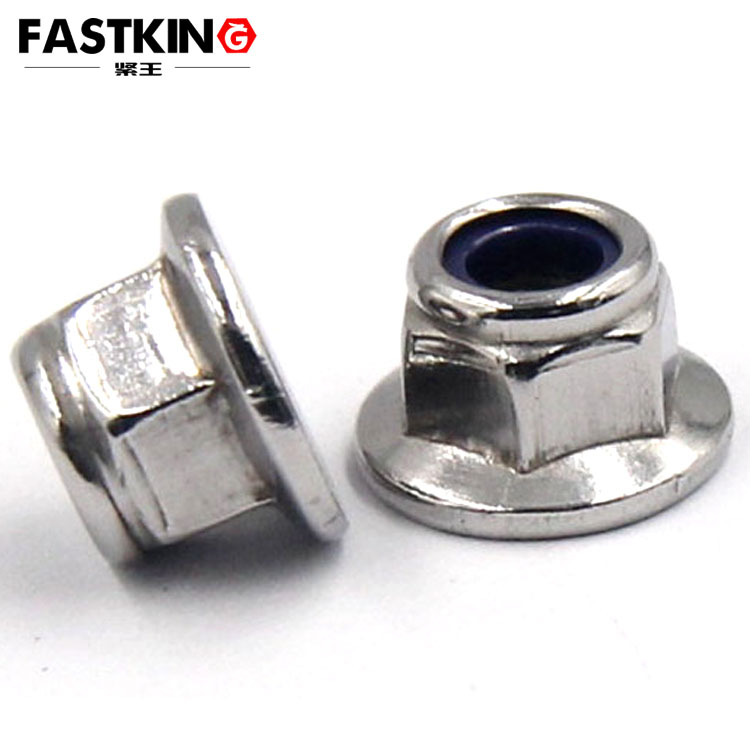
Usage Precautions and Troubleshooting
Common Installation Errors
Cross-threading causes premature nylon failure—prevent by ensuring axial alignment and hand-tightening ≥3 turns first. Over-torque crushes nylon or stretches bolts—strictly follow specifications.
Neglecting surface preparation reduces flange friction—use larger flanges for soft/coated materials (≥3× bolt diameter for aluminum).
Environmental factors matter—UV degrades nylon (use UV-resistant types outdoors); chemicals may attack nylon (verify compatibility).
Maintenance and Inspection
Regular checks should include:
- Visual inspection for corrosion/damage
- Marking method (alignment marks on nut/bolt) to detect loosening
- Sample residual torque measurements on critical joints
For loosening incidents, analyze root causes (excessive vibration, insufficient preload, or nylon failure) rather than simply retightening. Consider replacement, additional washers, or design improvements. Critical joints may require ultrasonic bolt stress monitoring.
Service Life and Replacement Criteria
Replace when:
- Visible nylon cracks/severe wear occur
- Flange deformation/rust affects flatness
- Thread damage impedes smooth engagement
- Maximum reuse cycles are exceeded
Storage affects lifespan—avoid >50°C, >70% RH, and direct sunlight. Keep unopened packages for ≤6 months. Don't mix batches due to potential nylon variations.
Development Trends of Flange Nylon Lock Nuts
Material Innovations
Advanced nylons (PA46, PPA) raise temperature limits >150°C. Nanocomposites enhance wear/creep resistance. Bio-based nylons improve sustainability.
Metal advancements include high-strength lightweight alloys and superior coatings (Dacromet, Zn-Ni) for marine corrosion resistance.
Design and Manufacturing Advances
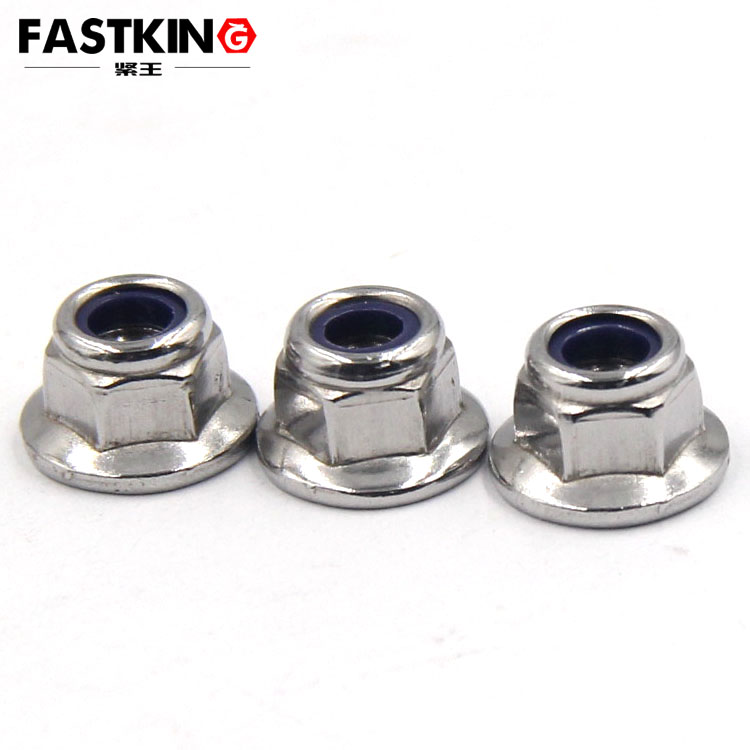
3D printing enables complex nylon insert geometries (e.g., multi-chamber designs for progressive locking). Smart nuts with embedded sensors enable real-time preload monitoring. Computational modeling optimizes flange textures for ideal friction coefficients.
Precision forming ensures dimensional consistency, while laser inspection guarantees 100% QC. Automated packaging/labeling streamlines production traceability.
Application Expansion
Growing demand in:
- Renewable energy (wind turbines, EV batteries)
- Medical devices (MRI-compatible antimagnetic versions)
- Aerospace (special alloy/high-performance nylon combinations)
Industry 4.0 integration enables predictive maintenance through IoT-connected fasteners and digital twin simulations for lifecycle performance optimization, further expanding application possibilities.