Countersunk blind rivets are widely used across various industries due to their ease of installation, strong and reliable connections, and aesthetic appeal. They are particularly suitable for applications where a smooth surface and high connection strength are required. This article will provide a detailed introduction to the application scenarios and usage methods of countersunk blind rivets to help readers better understand and apply this type of fastener.
Structure and Features of Countersunk Blind Rivets
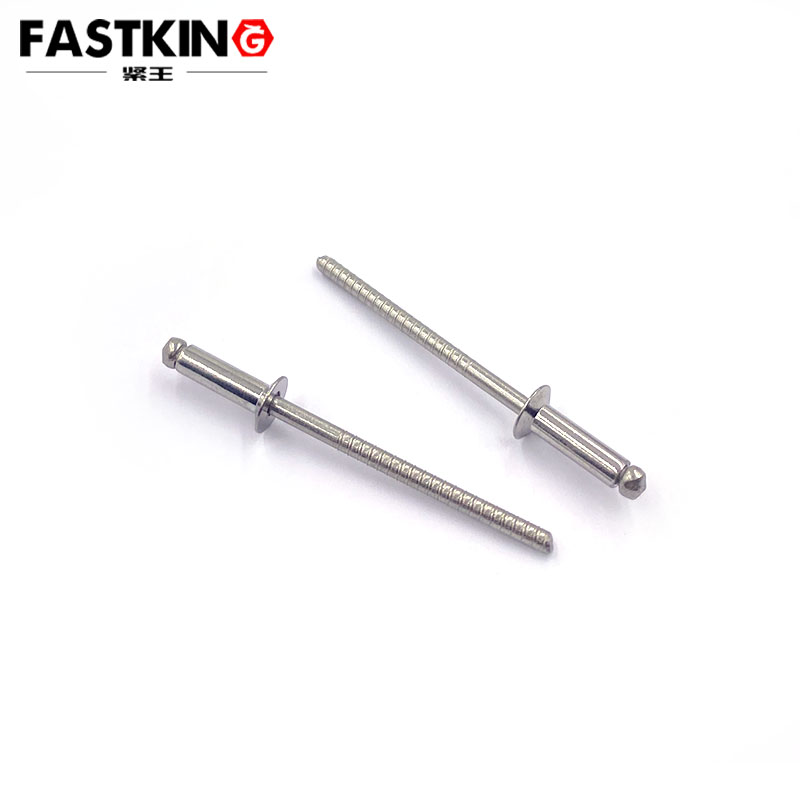
Countersunk blind rivets consist of two main parts: the rivet body and the mandrel. The rivet body is typically made from materials such as aluminum alloy or stainless steel, while the mandrel is made from high-strength steel. The key feature of this type of rivet is that the head of the rivet can be flush with the surface of the workpiece after installation, providing a smooth appearance, which is ideal for applications with high surface flatness requirements.
Main Features:
1. Smooth Surface: The head of the rivet is flush with the workpiece surface, offering an aesthetically pleasing appearance and no interference with subsequent processing.
2. Strong Connection: The blind riveting process creates a robust connection, suitable for high-strength connection requirements.
3. Easy Installation: With the use of a dedicated rivet gun, installation is quick and straightforward, resulting in high efficiency.
4. Wide Application Range: Suitable for connecting various materials, including metals and plastics.
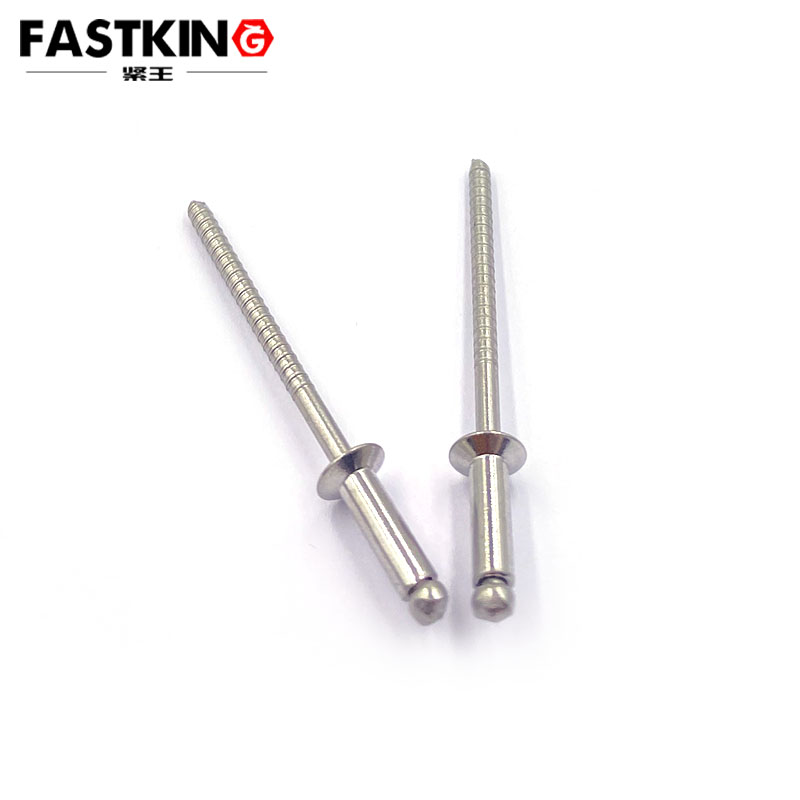
Application Scenarios of Countersunk Blind Rivets
Countersunk blind rivets are widely used across multiple industries. The following are some of the primary application scenarios:
1. Aerospace
In the aerospace industry, where weight and strength requirements for fasteners are extremely high, countersunk blind rivets are extensively used for connecting aircraft fuselages, wings, and other components. Their lightweight and high-strength characteristics meet the industry's stringent demands. Additionally, the smooth surface of the rivets aligns with the high aerodynamic requirements of aerospace applications.
2. Automotive Manufacturing
In automotive manufacturing, the connection of body panels and chassis components requires high strength and good sealing properties. Countersunk blind rivets fulfill these requirements while their easy installation aligns with the efficiency demands of automotive production lines.
3. Electronics
In the electronics industry, especially for connecting device casings and internal structures, countersunk blind rivets provide a strong connection while maintaining a smooth surface. This ensures that the appearance and functionality of the devices are not compromised.
4. Construction Industry
In construction, countersunk blind rivets are commonly used for fixing decorative materials such as facades and ceilings. Their smooth surface ensures an aesthetically pleasing appearance after installation, and the strong connection can withstand wind pressure and vibrations.
5. Home Appliance Manufacturing
For home appliances like refrigerators and washing machines, the connection of outer casings requires both a smooth surface and strong connection. Countersunk blind rivets meet these requirements while their easy installation aligns with the efficiency demands of home appliance production lines.
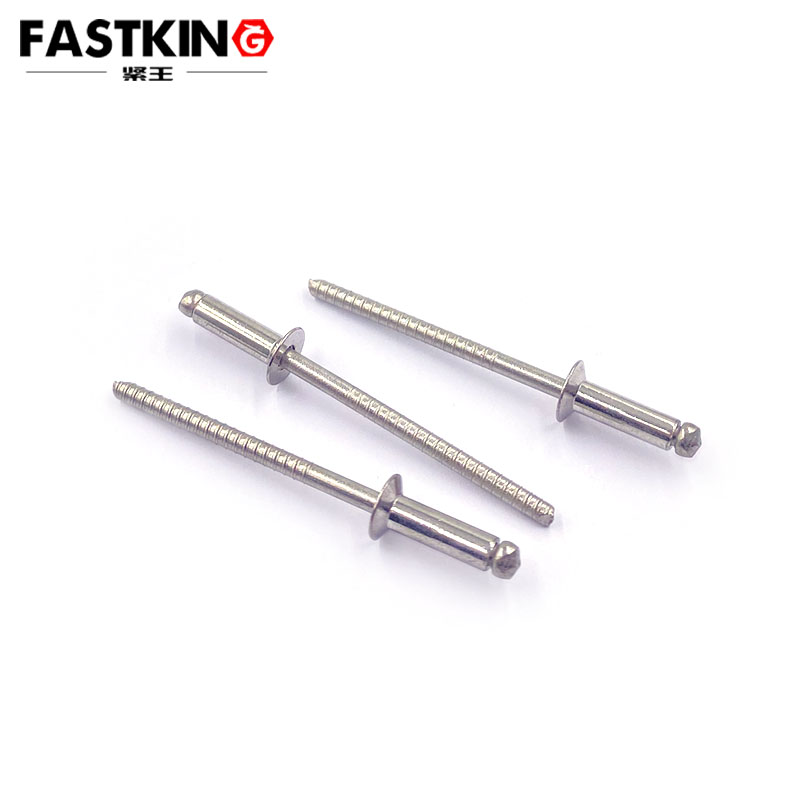
Usage Methods of Countersunk Blind Rivets
The installation of countersunk blind rivets requires a dedicated rivet gun. The following steps outline the installation process:
1. Preparation
Select the Right Rivet: Choose the appropriate rivet size and material based on the thickness and strength requirements of the materials to be connected.
Prepare Tools: Ensure that the rivet gun is in good working condition and prepare any auxiliary tools such as a drill and measuring instruments.
2. Drilling
Mark Hole Positions: According to the design requirements, mark the positions where the rivets will be installed on the materials.
Drill Holes: Use a drill to create holes at the marked positions. The hole diameter should match the rivet diameter, typically slightly larger (0.1-0.2 mm) than the rivet diameter.
3. Rivet Installation
Insert the Rivet: Place the rivet into the drilled hole, ensuring that the head of the rivet is flush with the surface of the workpiece.
Use the Rivet Gun: Align the rivet gun's head with the mandrel of the rivet and pull the trigger. The rivet gun will pull out the mandrel, causing the rivet body to expand and form a strong connection.
Complete Installation: Once the mandrel breaks, the rivet installation is complete. Check that the rivet head is flush with the workpiece surface and that the connection is secure.
4. Inspection and Maintenance
Inspect the Connection: After installation, check that the rivet connection is secure and the surface is smooth.
Maintain Tools: Regularly maintain the rivet gun to ensure it remains in good working condition, thereby improving installation efficiency and quality.
Precautions
1. Choose the Right Rivet: Select the appropriate rivet size and material based on the thickness and strength requirements of the materials being connected to ensure a secure connection.
2. Drilling Precision: Pay attention to the precision of the hole diameter and position during drilling to avoid oversized or undersized holes, which can affect the installation outcome.
3. Installation Force: When using the rivet gun, control the force to avoid excessive pulling that may damage the rivet or result in an insecure connection.
4. Safety Operations: During the installation process, follow safety protocols to prevent accidents from the rivet gun or flying rivets.
Conclusion
Countersunk blind rivets, as an efficient and reliable fastener, are widely used in industries such as aerospace, automotive manufacturing, electronics, construction, and home appliance manufacturing. Their smooth surface, strong connection, and easy installation make them an essential fastener in many applications. By selecting the right rivets and following proper usage methods, the advantages of countersunk blind rivets can be fully realized, enhancing connection quality and efficiency.