120° countersunk aluminum solid rivets are a common type of fastener widely used in applications requiring high strength and lightweight connections. Their distinguishing feature is the 120° countersunk head design, which allows the rivet to sit flush with the material surface after installation, minimizing protrusions. This makes them ideal for applications where surface smoothness is critical. Made from aluminum, these rivets are lightweight, corrosion-resistant, and offer good electrical conductivity, making them suitable for industries such as aerospace, automotive, and electronics.
Usage Methods for 120° Countersunk Aluminum Solid Rivets
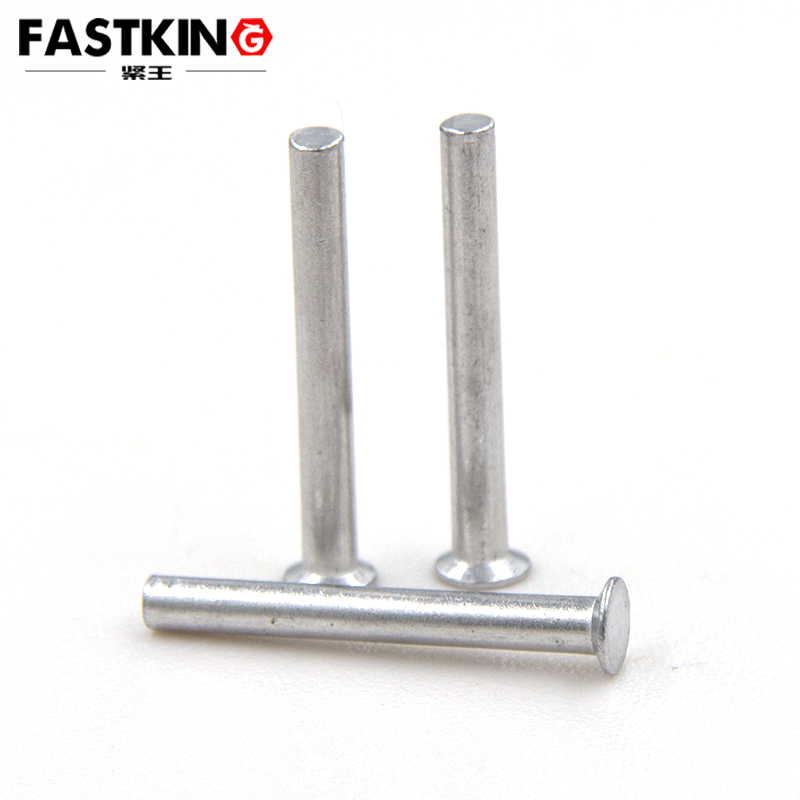
1. Preparation
Tools Required: To use 120° countersunk aluminum solid rivets, you typically need a rivet gun, drilling tools, and deburring tools.
Material Preparation: Ensure the surfaces of the materials to be joined are clean, flat, and free from oil or rust. Select a drill bit matching the rivet diameter and pre-drill holes in the materials.
2. Drilling
Choose a drill bit that matches the rivet diameter and drill holes in the materials. The hole diameter should be slightly larger than the rivet shank to allow easy insertion but not too large, as this could compromise the joint's strength.
After drilling, use a deburring tool to remove any burrs around the hole edges, ensuring smooth rivet installation.
3. Rivet Installation
Insert the rivet into the pre-drilled hole, ensuring the rivet head sits flush with the material surface.
Use a rivet gun to secure the rivet. Place the rivet gun's pull head over the rivet's tail and pull the handle firmly. This action deforms the rivet tail, forming a head that clamps the materials together.
After installation, check that the rivet head is flush with the material surface to ensure a proper finish.
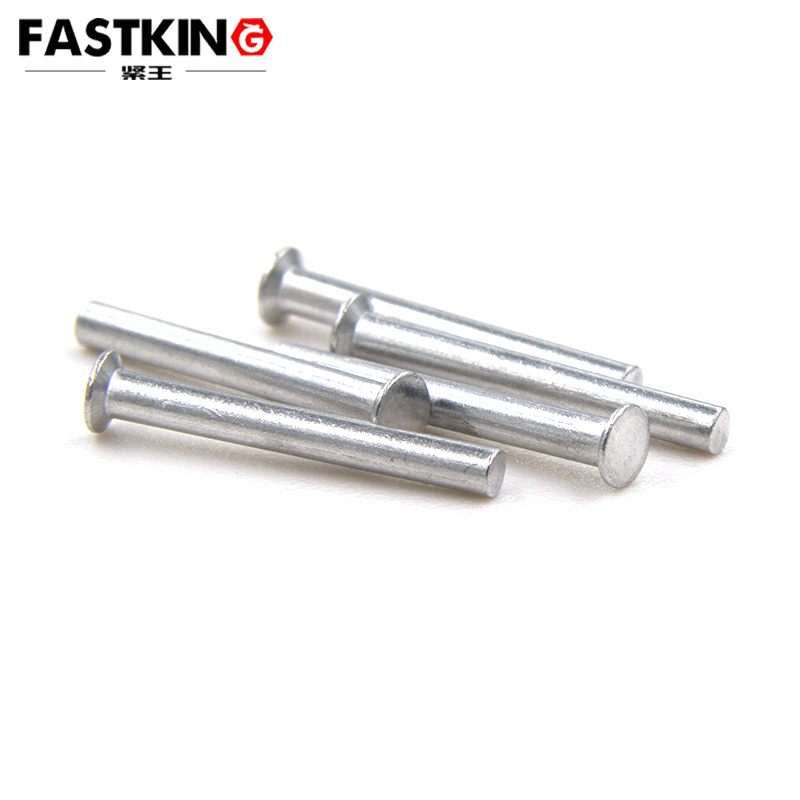
4. Inspection and Cleanup
After riveting, inspect the joint for strength and ensure the rivet head is flush. If there are any irregularities or looseness, rework the rivet.
Clean the work area to remove any rivet fragments or debris.
Applications of 120° Countersunk Aluminum Solid Rivets
1. Aerospace Industry
In aerospace, lightweight and high-strength connections are critical. 120° countersunk aluminum solid rivets are widely used in aircraft fuselages, wings, and engine components due to their lightweight, corrosion resistance, and high strength. The countersunk design reduces air resistance, enhancing flight efficiency.
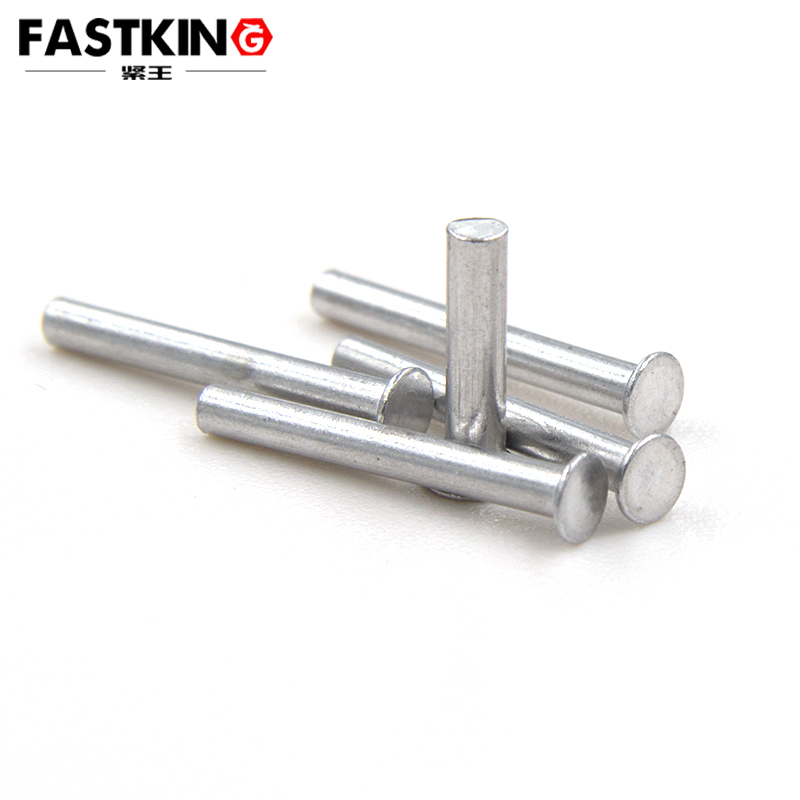
2. Automotive Manufacturing
In automotive manufacturing, these rivets are commonly used for joining body panels, chassis, and interior components. Aluminum rivets help reduce vehicle weight and resist vibrations and corrosion, extending the vehicle's lifespan.
3. Electronics
In electronics manufacturing, 120° countersunk aluminum solid rivets are often used to secure circuit boards, heat sinks, and enclosures. Aluminum's excellent conductivity and thermal properties enhance the performance and stability of electronic devices.
4. Architectural Decoration
In architectural decoration, these rivets are used for fixing aluminum doors, windows, curtain walls, and ceilings. The countersunk design ensures a smooth, aesthetically pleasing finish, while aluminum's weather resistance makes it suitable for both indoor and outdoor environments.
5. Rail Transportation
In rail transportation, 120° countersunk aluminum solid rivets are extensively used in high-speed trains and subway carriages. Their lightweight and high-strength properties help reduce vehicle weight and improve operational efficiency, while aluminum's corrosion resistance ensures durability in harsh environments.
Advantages of 120° Countersunk Aluminum Solid Rivets
1. Lightweight: Aluminum's low density reduces the weight of connected components, making it ideal for weight-sensitive applications.
2. Corrosion Resistance: Aluminum offers excellent resistance to corrosion, ensuring long-term performance in harsh environments.
3. High Strength: The solid design provides high tensile and shear strength, enabling the rivets to withstand significant loads.
4. Aesthetic Appeal: The 120° countersunk head design ensures a flush finish, enhancing the visual appeal of the joint.
Precautions
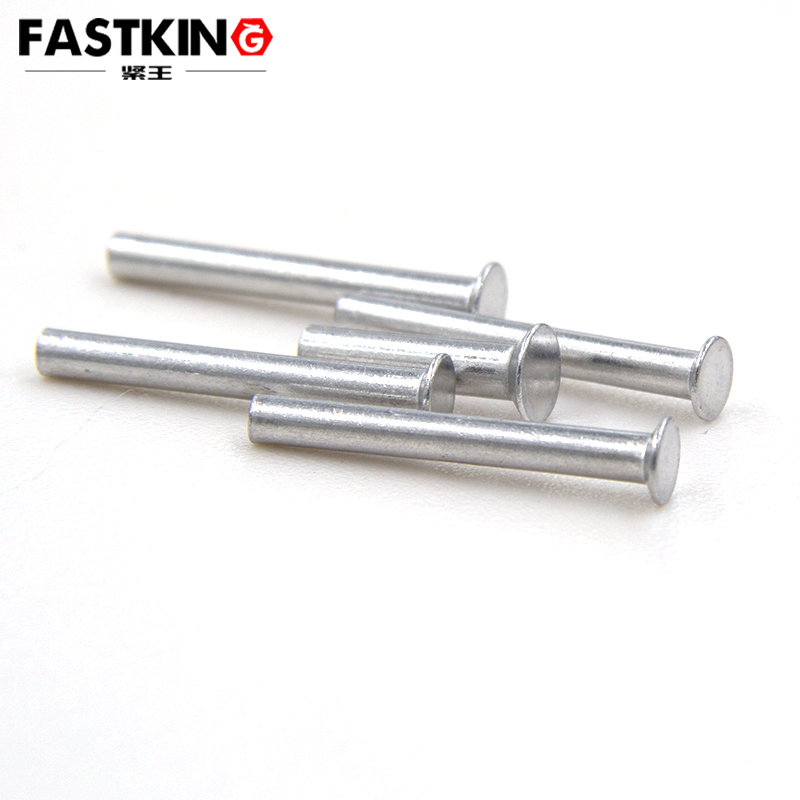
1. Select the Right Rivet Size: Choose the appropriate rivet size based on the material thickness and strength requirements to ensure a secure joint.
2. Avoid Over-Riveting: Apply the right amount of force during riveting to prevent material deformation or rivet damage.
3. Regular Inspections: Periodically check the riveted joints during long-term use to ensure their integrity and safety.
Conclusion
120° countersunk aluminum solid rivets are a highly efficient and reliable fastener widely used in aerospace, automotive, electronics, architectural decoration, and rail transportation industries. Their lightweight, corrosion-resistant, and high-strength properties make them a preferred choice for many applications. By following proper usage methods and precautions, their performance advantages can be fully utilized, enhancing the reliability and aesthetics of connected components.