Brass threaded inserts, also known as brass bushings, brass nuts, or brass threaded sleeves, are internally threaded fasteners made from copper alloys. Compared to standard nuts, brass threaded inserts possess unique physical and chemical properties, making them indispensable in various industrial fields. Typically manufactured from materials such as brass, bronze, or copper, they exhibit excellent electrical conductivity, thermal conductivity, corrosion resistance, and machinability.
Brass threaded inserts come in diverse structural designs, including straight knurls, diamond knurls, and helical knurls, to enhance their grip in plastic or soft materials. Based on application requirements, they can be categorized into through-hole and blind-hole types, with sizes ranging from M2 to M12 to accommodate different usage scenarios.
Primary Application Scenarios
1. Plastic Products Industry
Brass threaded inserts are most widely used in the plastic manufacturing sector. During injection molding, they are pre-placed in molds and integrated into plastic components. Common applications include:
Household appliance casings: Frequently disassembled parts such as washing machine control panels and air conditioner housings
Electronic devices: Enclosure fastening for routers, switches, and other networking equipment
Daily-use plastic products: Luggage wheel mounts and connection points for plastic furniture
Automotive plastic parts: Dashboard and door panel assemblies requiring metal-threaded reinforcement
Using brass threaded inserts in plastic components prevents thread wear caused by direct tapping into plastic, significantly improving product lifespan and assembly reliability.
2. Electronics and Electrical Industry
The superior conductivity of brass threaded inserts makes them ideal for electronic applications:
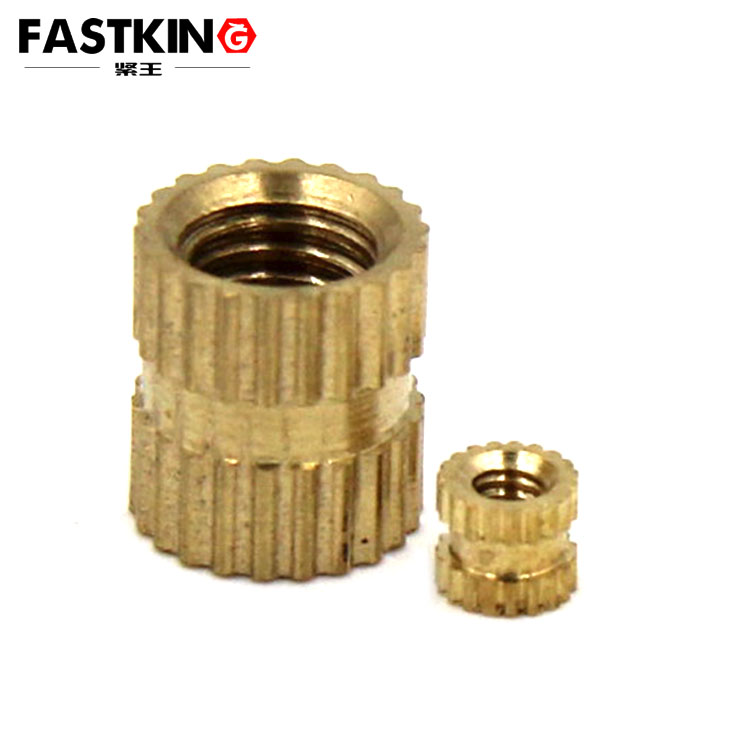
PCB mounting: Secures circuit boards while providing effective grounding
Electronic enclosures: Reliable threaded connections in aluminum or plastic housings
Power equipment: High-current connection points requiring both conductivity and fastening
LED lighting: Heat sink and fixture connections leveraging copper’s thermal properties
3. Automotive Manufacturing
Modern automotive applications include:
Interior component fastening: Headliners, door panels, and dashboards
Cable harness fixation: Provides secure anchor points for wiring
Engine bay components: High-temperature-resistant threaded connections
In-vehicle electronics: Navigation systems and audio equipment installation
4. Furniture and Building Materials
Key applications in this sector:
Flat-pack furniture: Connection points for modular furniture
Sanitary ware: Secure fittings for shower enclosures and sinks in humid environments
Door/window hardware: Hinge installations for premium doors and windows
Decorative materials: Concealed fasteners for wall panels
5. Medical Equipment
Brass threaded inserts meet stringent medical requirements:
Sterilization devices: Corrosion- and heat-resistant autoclave components
Imaging equipment: Plastic housing connections for CT/MRI machines
Surgical instruments: Reusable, sterilizable threaded joints
Installation Methods
1. Injection Molding
The most common method involves:
Mold preparation: Machining insert placement cavities per product design
Insert pretreatment: Cleaning or surface treatment as needed
Mold insertion: Precision placement via robotic arms or manual labor
Plastic injection: Molten plastic bonds with inserts during cooling
Demolding inspection: Verifying insert alignment and retention strength
Key considerations:
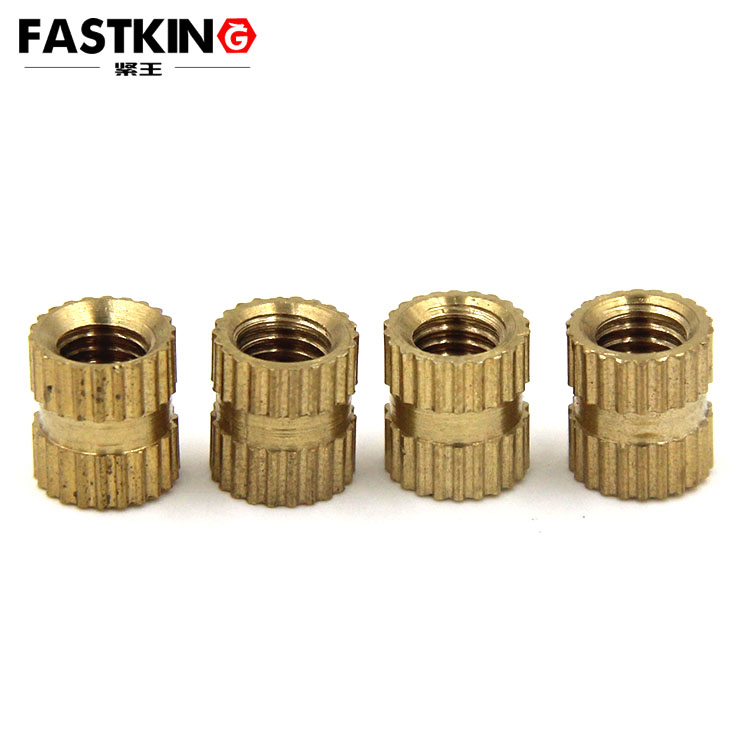
- Ensure precise mold-insert fit
- Control temperature/pressure to prevent displacement
- Use ultrasonic or thermal methods for precision parts
2. Press-Fit Installation
For small batches or repairs:
Pilot hole drilling: Create holes slightly smaller than insert OD
Surface treatment: Roughen hole walls for better adhesion
Pressing operation: Install using arbor presses or specialized tools
Inspection: Confirm perpendicularity and retention strength
3. Thermal Insertion
For thermoplastic materials:
Preheating: Heat inserts to optimal temperature
Insertion: Press into pre-drilled holes while hot
Cooling: Maintain pressure until plastic solidifies
Trimming: Remove excess plastic flash
4. Ultrasonic Installation
High-efficiency method:
Alignment: Position inserts over pilot holes
Ultrasonic activation: Vibrations melt contact surfaces
Pressurization: Simultaneous pressure embeds inserts
Solidification: Brief post-vibration pressure hold
Usage Considerations
Material selection: Choose alloys like naval brass for marine environments
Dimensional accuracy: Ensure proper thread engagement with bolts
Orientation: Install chamfered end toward load-bearing direction
Corrosion protection: Apply nickel plating for harsh conditions
Maintenance: Periodic inspections and anti-corrosion lubrication
Future Trends
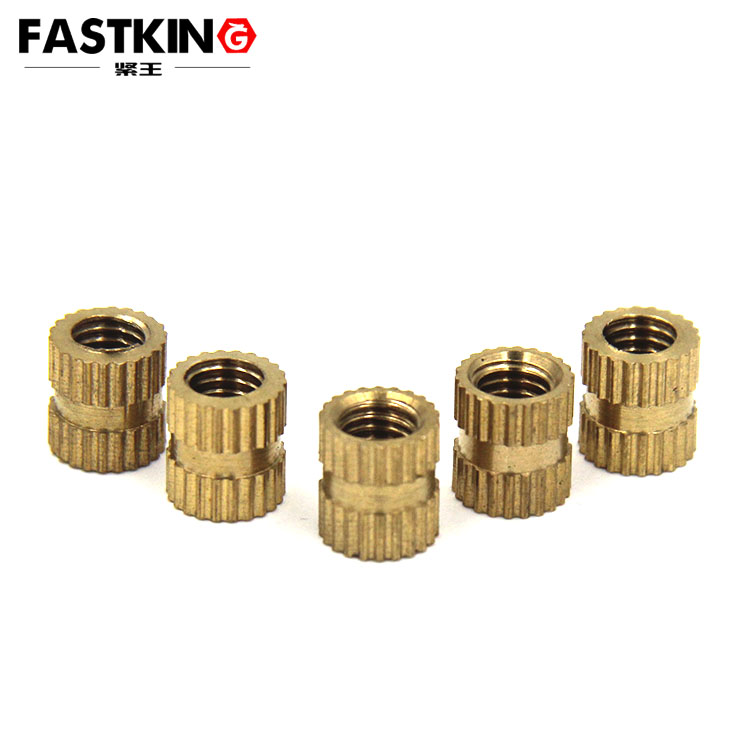
Advancements are driving developments in:
High-performance alloys: Stronger, more corrosion-resistant materials
Miniaturization: Micro-inserts for compact electronics
Specialized designs: Self-locking, waterproof variants
Eco-friendly production: Sustainable surface treatments
Smart installation: Integration with automated production lines
As a seemingly simple yet critical fastener, brass threaded inserts will continue expanding their applications alongside industrial progress. Proper selection and usage significantly enhance product quality while reducing maintenance costs.