Spot welding nuts are specialized fasteners designed specifically for welding processes, which permanently connect to metal sheets or other metal components through resistance spot welding. Compared to traditional threaded fasteners, spot welding nuts offer significant advantages such as high connection strength, fast installation efficiency, and excellent aesthetic appeal, making them indispensable connecting components in modern manufacturing.
Primary Application Scenarios of Spot Welding Nuts
1. Automotive Manufacturing
The automotive industry represents the largest application field for spot welding nuts. In vehicle body manufacturing, they are extensively used in:
- Door hinge installation points
- Dashboard bracket fixing locations
- Seat rail connection areas
- Bumper mounting positions
- Various decorative and functional component fastening
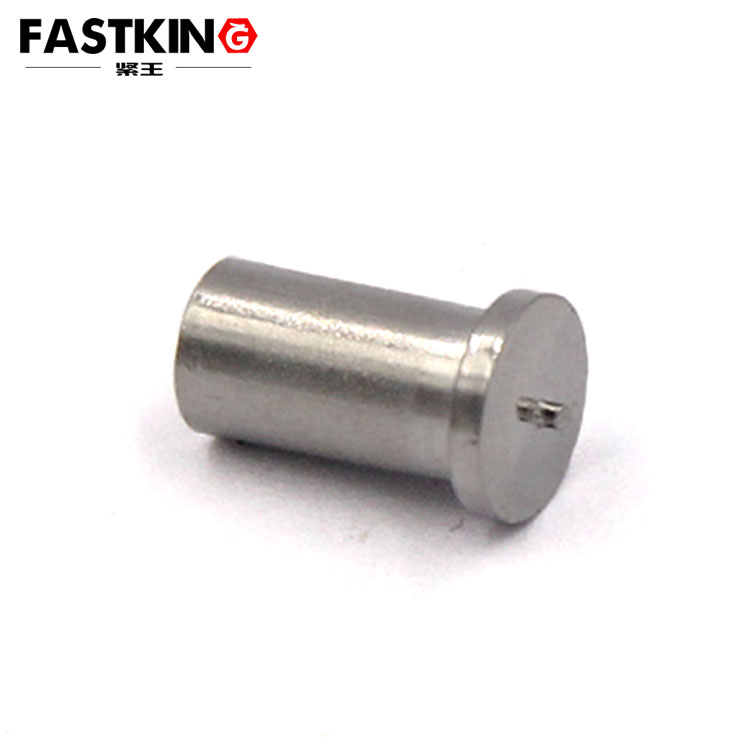
The use of spot welding nuts in automotive manufacturing can significantly improve assembly efficiency, with skilled workers capable of completing thousands of welding points daily. The connection strength is reliable, capable of withstanding vibrations and impacts during vehicle operation.
2. Household Appliances
Spot welding nuts are also widely used in white goods and consumer electronics:
- Refrigerator and washing machine casing assembly
- Structural connections for indoor/outdoor air conditioning units
- TV backplate bracket fixing
- Internal component installation for microwaves and ovens
- Base fixing for small appliances like rice cookers and electric kettles
In household appliances, spot welding nuts enable clean, flush installations while ensuring connection strength that meets product lifecycle requirements.
3. Electronic Equipment
Precision electronic devices have special requirements for connectors, making spot welding nuts ideal for:
- Server rack assembly
- Communication equipment chassis
- Industrial control cabinets
- Electronic instrument housings
- PCB mounting brackets
In these applications, spot welding nuts not only provide reliable mechanical connections but also maintain excellent electromagnetic compatibility, minimizing interference with signal transmission.
4. Architectural Decoration
Modern architectural metal decoration projects increasingly adopt spot welding nuts for:
- Curtain wall system connections
- Metal ceiling installations
- Interior partition fixing
- Decorative trim assembly
- Door/window hardware installation
In construction, spot welding nuts enable concealed installations that preserve architectural aesthetics while meeting structural safety requirements.
5. Rail Transportation
In high-speed rail and subway vehicle manufacturing:
- Car body side panel connections
- Interior trim fixing
- Equipment mounting racks
- Seat tracks
- Various panel fixings
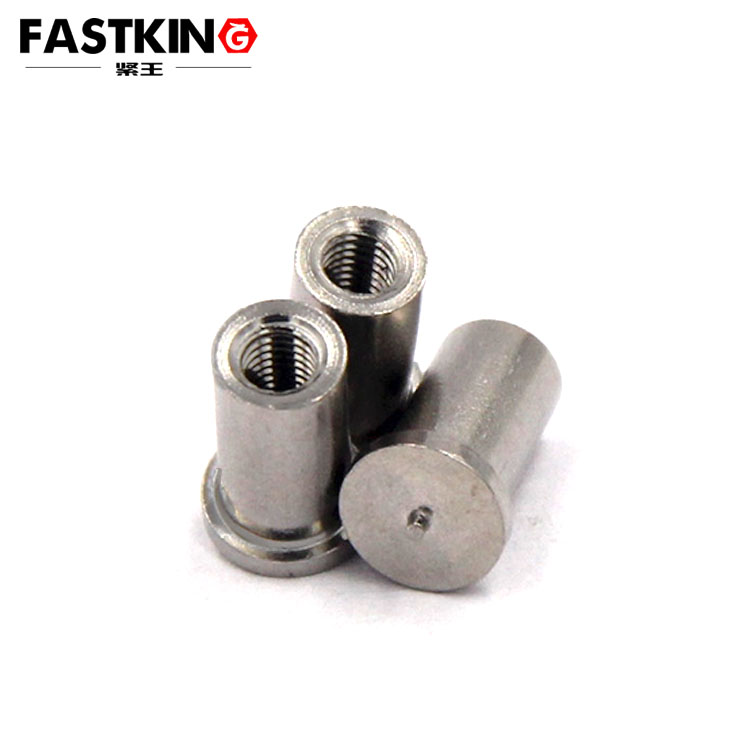
Rail transportation demands extremely high safety standards, and spot welding nuts ensure connections remain secure during long-term operation, guaranteeing travel safety.
Usage Methods of Spot Welding Nuts
1. Preparation Work
Selection Considerations:
- Choose appropriate nut height based on base material thickness
- Determine thread specifications (commonly M3-M12) according to load requirements
- Select surface treatment (zinc plating, nickel plating, etc.) based on usage environment
- Stainless steel material required for special applications
Workpiece Preparation:
- Clean welding surfaces, removing oil and oxidation layers
- Ensure sheet metal is flat without severe deformation
- Accurate positioning with markings or positioning fixtures
2. Welding Equipment Setup
Resistance Spot Welder Parameter Adjustment:
- Welding current: Typically 5000-15000A, set according to nut specifications and sheet thickness
- Welding time: Generally controlled at 5-30 cycles (0.1-0.6 seconds)
- Electrode pressure: Approximately 200-600N, ensuring good contact without damaging workpiece
- Electrode selection: Flat or spherical electrodes, diameter usually 1.5 times the nut boss diameter
Equipment Inspection:
- Confirm cooling system functions properly
- Check electrode wear, dress or replace as needed
- Conduct test welds and inspect quality
3. Welding Operation Steps
Positioning Placement: Accurately place spot welding nut at predetermined position with boss facing sheet metal
Electrode Alignment: Align upper/lower electrodes with nut welding boss, ensuring concentricity
Pressure Application: Apply pre-pressure to ensure tight contact between nut and sheet
Power Activation: Trigger welding current to complete weld per set parameters
Pressure Maintenance: Maintain pressure briefly (≈0.1s) after current cutoff
Electrode Removal: Slowly lift electrode to prevent cracking from sudden release
Quality Inspection: Visually inspect weld appearance, conduct destructive testing if necessary
4. Post-Welding Treatment
Remove welding spatter
Check for thread damage, re-tap if needed
Apply necessary anti-corrosion treatment
Mark or record welded areas
5. Special Application Techniques
Thin Sheet Welding:
Use small diameter nuts (M3-M5)
Reduce welding current and shorten duration
Employ flanged nuts to increase contact area
Multi-layer Sheet Welding:
Ensure tight contact between all layers
Appropriately increase welding current and pressure
Consider through-type welding nuts
Dissimilar Metal Welding:
Note differences in conductivity and thermal expansion coefficients
May require parameter adjustments
Consider transition layers or special platings
Precautions for Using Spot Welding Nuts
Safety Protection: Wear protective goggles to prevent spatter injuries; ensure proper ventilation.
Parameter Optimization: Determine optimal parameters through testing for different material/thickness combinations—avoid simple copying.
Electrode Maintenance: Regularly clean and dress electrodes to maintain good contact surfaces and prevent inconsistent welding quality.
Quality Inspection: Establish periodic sampling systems using torque tests, tensile tests, etc. to verify weld strength.
Storage Conditions: Store spot welding nuts in dry environments to prevent thread corrosion affecting subsequent assembly.
Compatibility Considerations: Match subsequent assembly bolts with nut materials to prevent galvanic corrosion.
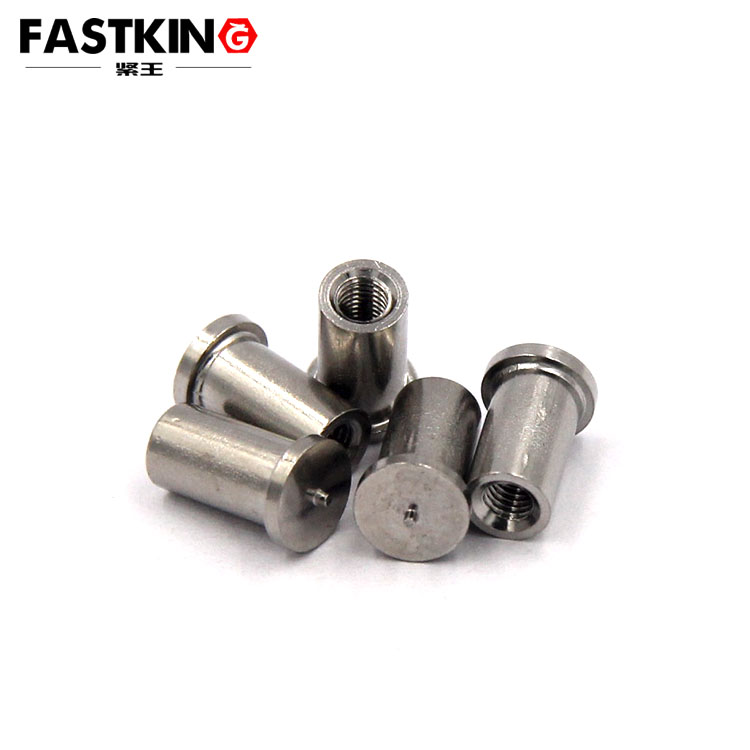
Conclusion
As an efficient and reliable connection method, spot welding nuts have found widespread application across industrial sectors. Proper selection and usage can significantly enhance product quality and production efficiency while reducing overall costs. With advancements in materials science and welding technology, the performance and applications of spot welding nuts will continue to expand, offering superior connection solutions for modern manufacturing. For practical applications, we recommend close collaboration with professional suppliers to obtain the most suitable technical support and product selection.