I. Basic Concept and Structural Features of Through-Hole Knurled High Nuts
Through-hole knurled high nuts represent a specially designed fastening component that plays a vital role in modern mechanical assembly and industrial production. Compared with standard nuts, these nuts exhibit several distinctive structural characteristics: Firstly, their overall height significantly exceeds that of conventional nuts, with this elevated design providing enhanced load-bearing capacity and deeper thread engagement. Secondly, the nut's exterior surface undergoes knurling treatment, creating uniform concave-convex patterns that not only improve aesthetics but more importantly substantially increase manual handling friction. Thirdly, the "through-hole" design features continuous internal threading throughout the entire nut body without any closed end, allowing bolts or screws to pass completely through the nut.
The knurling process constitutes a critical manufacturing step for these nuts, typically employing straight or diamond knurling patterns. Straight knurling produces linear patterns parallel to the axis, while diamond knurling creates intersecting rhombic motifs. Knurling patterns also vary in coarseness, with options including coarse, medium, or fine knurls according to application requirements. This surface treatment enhances not only appearance but more significantly its practical value—enabling operators to easily tighten or loosen nuts even without tools or while wearing gloves.
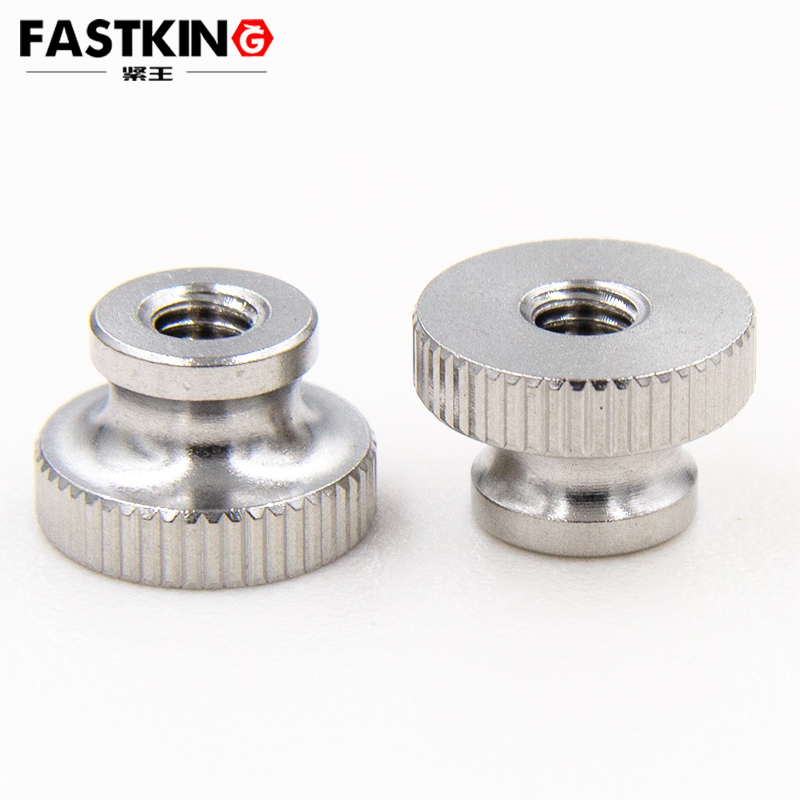
II. Working Principles of Through-Hole Knurled High Nuts
The fastening mechanism of through-hole knurled high nuts relies on the mechanical properties of threaded pairs. When engaged with bolts, the interaction between their threaded inclines converts rotational motion into linear motion, generating powerful axial preload forces. The heightened nut design increases thread engagement length, and according to mechanical principles, longer engagement translates to more uniform load distribution and superior anti-loosening capability. Research indicates that the first 3-4 threads bear most of the load in threaded connections, and high nuts effectively reduce individual thread burden by increasing engagement count, markedly improving connection reliability.
The knurled surface performs multiple functions during nut operation. From a tribological perspective, knurling increases surface roughness and friction coefficient, facilitating more efficient manual operation with reduced slippage. In vibratory environments, the high-friction knurled surface can also help suppress spontaneous rotational loosening. Additionally, the knurled structure disrupts the nut's external surface continuity, with this microscopic discontinuity aiding stress dispersion and minimizing stress concentration phenomena.
The through-hole design offers installation flexibility. In applications requiring both bolt ends to protrude—such as when secondary fixation with pins is necessary—the through-hole configuration proves particularly valuable. Simultaneously, this design facilitates thread engagement inspection and maintenance cleaning.
III. Mechanical Performance Advantages of Through-Hole Knurled High Nuts
Through-hole knurled high nuts demonstrate multiple mechanical performance advantages. Foremost is their exceptional anti-loosening capability. In vibratory conditions, standard nuts tend to gradually loosen through micro-displacement, whereas high nuts require substantially greater cumulative displacement for complete detachment due to increased thread engagement. Experimental data shows that under identical vibration conditions, high nuts exhibit 3-5 times longer loosening durations compared to standard nuts.
Load-bearing capacity represents another notable advantage. The strength of threaded connections depends on their weakest link, typically thread stripping failure for standard nuts. High nuts dramatically improve stripping resistance by increasing thread engagement count. Taking M10 nuts as an example, standard-height nuts provide approximately 40kN proof load, while equivalent-material high nuts can achieve over 60kN.
Temperature adaptability also characterizes high nuts. In environments with significant thermal variation, material expansion and contraction affect connection tightness. With their extended thread contact length, high nuts better compensate for dimensional changes induced by temperature differentials, maintaining stable preload. This property makes them indispensable in outdoor equipment, aerospace, and similar fields.
IV. Primary Application Scenarios for Through-Hole Knurled High Nuts
Equipment maintenance sectors constitute traditional application areas for through-hole knurled high nuts. Their advantages become particularly evident for frequently disassembled maintenance panels and inspection covers. Maintenance personnel often work in confined spaces under tool-restricted conditions where knurled surfaces enable rapid operation. For instance, large motor protective covers and gearbox inspection windows commonly employ this design. Reports from a heavy machinery manufacturer indicate that adopting through-hole knurled high nuts reduced average routine maintenance time by 25%.
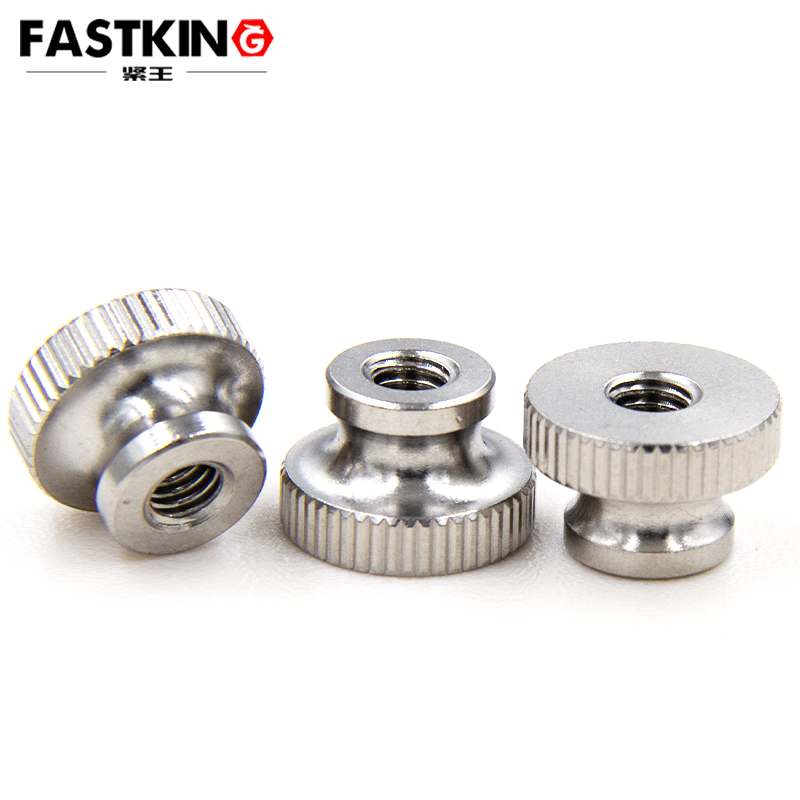
Electronics and electrical industries present special requirements for these nuts. In server racks and communication equipment where tool contact might cause short circuits, manually operated knurled nuts serve as ideal solutions. Simultaneously, insulating material knurled nuts are frequently used in high-voltage electrical equipment, ensuring secure installation while preventing conductivity risks. Tests by a prominent network equipment supplier revealed that using nylon knurled high nuts improved assembly efficiency by 40% over traditional screw connections while reducing electrostatic discharge incidents by 90%.
Automotive manufacturing and repair represents another crucial application field. For interior component fixation and battery terminal fastening, knurled nuts facilitate quick assembly/disassembly without specialized tools. Race and specialty vehicles incorporate this design more extensively considering emergency repair needs. Automotive manufacturer data demonstrates that connection points using knurled nuts showed 70% lower failure rates in vibration testing.
Medical equipment shows growing demand for through-hole knurled high nuts. On hospital beds, wheelchairs, and medical carts requiring frequent positional adjustments, knurled surfaces provide necessary friction for gloved healthcare workers. Additionally, medical-grade stainless steel knurled nuts are employed for surgical instruments and imaging equipment, meeting hygiene standards while simplifying sterilization. Statistics from a hospital equipment department indicate that medical devices incorporating knurled nuts extended adjustable component service life threefold.
Aerospace applications impose extreme requirements on fasteners, where through-hole knurled high nuts find specialized use. Aircraft interior panel and access panel fixation must balance weight, reliability, and rapid maintenance considerations. Aerospace-grade aluminum or titanium knurled nuts offer ideal solutions by ensuring strength while reducing weight. An airline engineering department reported that switching to high nuts in aircraft seat mounting systems reduced annual maintenance costs by $150,000 per aircraft.
V. Selection Criteria for Through-Hole Knurled High Nuts
Choosing appropriate through-hole knurled high nuts requires considering multiple factors. Material compatibility forms the primary principle, with nut material matching or complementing bolt material to prevent galvanic corrosion. Common materials include carbon steel, stainless steel, brass, aluminum alloys, and engineering plastics—each offering different strength grades and corrosion resistance. For example, marine environments favor 316 stainless steel, while lightweight applications may consider 7075 aluminum alloy.
Dimensional parameters determination proves equally critical. Thread specifications must precisely match bolts, including nominal diameter, pitch, and thread type (metric, imperial, etc.). Nut height typically ranges 1.5-2 times nominal diameter—insufficient height negates high nut advantages, while excessive height wastes material. Knurling pattern selection should balance practical needs, with coarse patterns providing greater friction (potentially affecting aesthetics) and fine patterns offering the opposite.
Special environment considerations must not be overlooked. High-temperature settings require heat-resistant alloys, corrosive environments demand Hastelloy or plated protection, while insulation needs may specify nylon or PEEK engineering plastics. Reports indicate that a chemical plant switching from standard carbon steel to specialty alloy knurled nuts reduced replacement frequency from monthly to annually, dramatically cutting maintenance costs and safety risks.
VI. Installation and Maintenance Guidelines
Proper installation methods are essential for optimizing through-hole knurled high nut performance. Preload control represents the core element, as excessive tightness risks thread damage or fracture while insufficient tightness compromises anti-loosening effectiveness. For critical applications, torque wrenches should apply standardized values. Data suggests approximately 35% of threaded connection failures originate from improper preload.
Regular inspection systems are indispensable. Even high nuts may loosen in vibratory environments, necessitating established inspection intervals. Inspections should verify not only nut tightness but also thread wear and surface corrosion conditions. A wind farm technical manual specifying quarterly comprehensive inspections for tower connection knurled nuts achieved 60% reduction in mechanical failure rates.
Maintenance practices significantly extend service life. Appropriate lubrication reduces thread wear but requires compatibility with operating environments. Stainless steel nuts in chloride-rich settings need particular attention to prevent stress corrosion cracking. Documented cases show a coastal power station extending knurled nut lifespan fourfold through regular cleaning and specialized anti-corrosion grease application.
VII. Future Development Trends
With advancing manufacturing technology, through-hole knurled high nuts are progressing toward intelligentization. Smart nuts incorporating sensing elements have begun appearing in critical equipment, enabling real-time preload monitoring and loosening risk alerts. A bridge monitoring project adopting this technology successfully prevented multiple potential incidents.
Advanced material applications represent another trend. Carbon fiber reinforced composite knurled nuts combining high strength with lightweight properties are emerging in aerospace. Graphene coating technology promises further improvements in wear and corrosion resistance. Laboratory data indicates new coatings increase nut wear resistance by 80%.
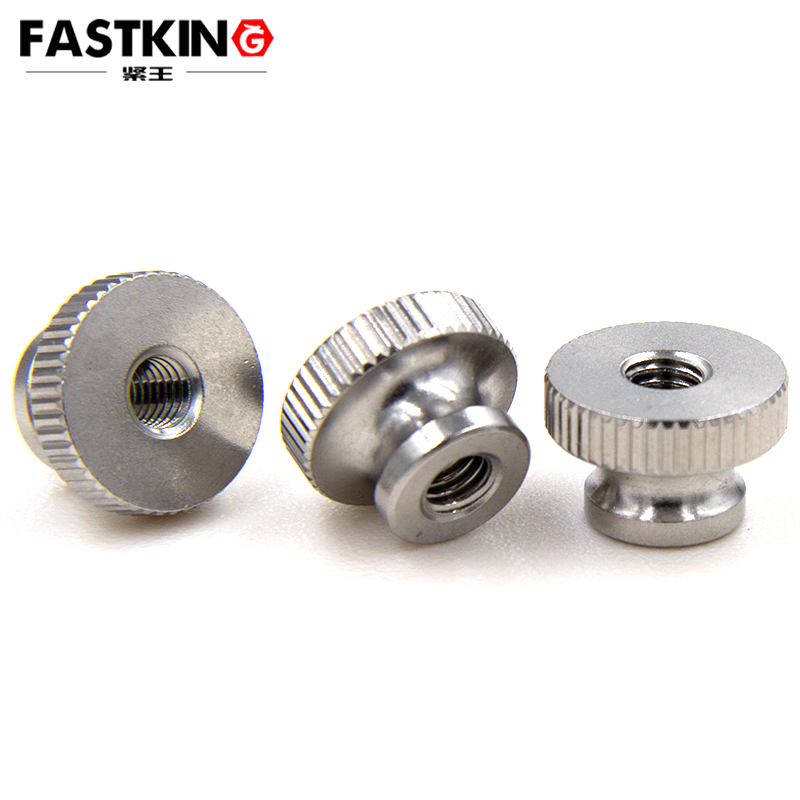
Manufacturing process innovations are underway. 3D printing enables rapid prototyping and small-batch custom production, particularly suited for special specification knurled nuts. Laser knurling and other novel processes create more precise surface patterns, enhancing operational feel. A precision instrument manufacturer adopting 3D-printed custom knurled nuts reduced development cycles by 50%.
In conclusion, through-hole knurled high nuts have become indispensable fastening components in modern industry due to their unique design advantages and broad application adaptability. Proper understanding of their working principles combined with appropriate selection and usage can significantly improve mechanical connection reliability and maintenance efficiency. As technology progresses, this traditional component will continue evolving to meet increasingly complex engineering demands.