Overview of Square Nuts
Square nuts, as fundamental components in mechanical fastening, are square-shaped fasteners that work in conjunction with bolts and screws to achieve secure connections through threaded engagement. Compared to standard hex nuts, square nuts offer unique performance advantages and application characteristics due to their distinctive geometric shape.
Structurally, square nuts are typically manufactured from carbon steel, stainless steel, or copper alloys, often with surface treatments like zinc plating or black oxide for corrosion resistance. Their four right-angled sides provide greater contact area, making them indispensable in specific applications. Standard square nuts range from M3 to M36 in size, accommodating various load requirements.
Primary Application Scenarios
1. Timber Construction SectorIn traditional timber framing and modern wooden structure assembly, square nuts play a vital role. Their larger contact surface prevents sinking into softer wood materials during tightening, unlike hex nuts. Key applications include:
- Reinforcement of beam-to-column connections
- Fixation of wooden stair treads
- Framework assembly for large wooden furniture
- Construction of outdoor wooden decks
2. Rail Transportation Industry
In rail vehicle manufacturing, square nuts are commonly used for:
- Interior panel mounting: Their anti-rotation feature facilitates single-person operation in confined spaces
- Seat adjustment systems: Nuts embedded in specialized tracks allow flexible positioning
- Electrical equipment racks: Vibration resistance prevents loosening
3. Agricultural Machinery
Agricultural equipment operating in harsh environments benefits from square nuts in:
- Combine harvester sieve plate fixation
- Tractor transmission system guard installation
- Irrigation system pipe connections
4. Special Industrial Environments
- High-temperature settings: Heat-resistant alloy nuts for boilers and thermal pipelines
- Chemical processing equipment: Stainless steel nuts for corrosion resistance
- High-vibration applications: Used with locking washers to prevent loosening
Detailed Usage Methods
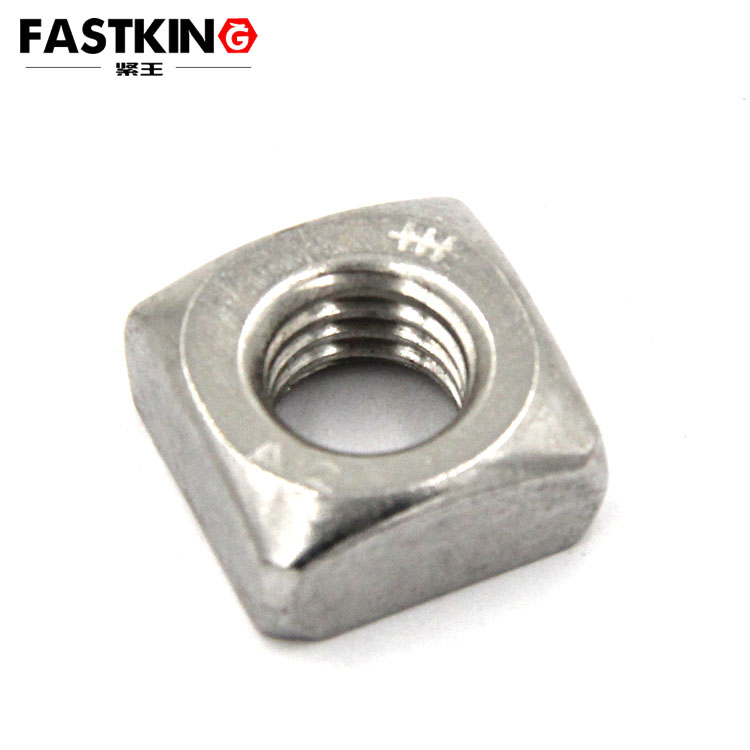
1. Pre-installation Preparation
Tool Selection:
- Exposed installations: Adjustable wrenches, open-end wrenches, or specialized square nut sockets
- Embedded installations: Rubber or wooden mallets for positioning
- Critical connections: Torque wrenches for precise tightening
Surface Preparation:
- Clean contaminants and burrs from mating surfaces
- Inspect thread integrity, using taps for repairs when necessary
- Apply anti-seize compounds or threadlockers in corrosive environments
2. Installation Procedures
Standard Installation:
Insert bolt through connection hole
Hand-tighten square nut several turns
Secure nut with appropriate tool
Tighten bolt head to specified torque
Verify connection integrity
Embedded Installation (for wood/soft materials):
Create square hole slightly smaller than nut dimensions
Align nut perpendicular to hole
Gently tap flush with surface
Remove debris from cavity
Insert and tighten bolt
Channel Installation (for T-slots/dovetails):
Insert nut at angle along channel
Rotate 90° to engage channel
Slide to desired position
Complete bolt connection
3. Usage Precautions
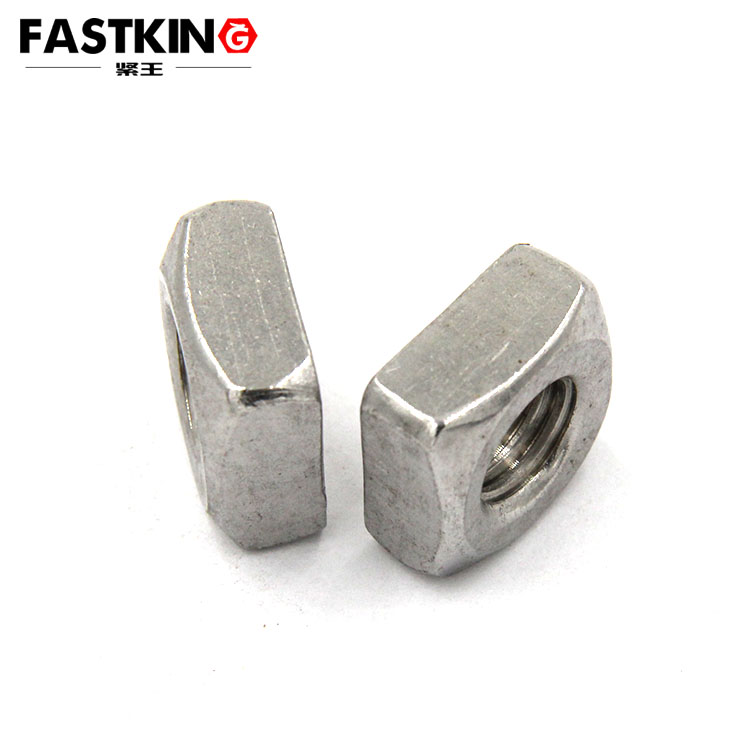
Torque Control: Follow manufacturer specifications (e.g., ~45N·m for M10 grade 8.8 nuts)
Anti-loosening: Use double-nutting, spring washers, or threadlockers in vibrating environments
Inspection Intervals: Implement regular checks (typically every 500 operating hours)
Corrosion Prevention: Select appropriate materials and maintain protective coatings
Maintenance and Replacement
1. Routine Maintenance
Regular cleaning of surface contaminants
Inspection for corrosion signs
Verification of positional stability
Examination for wear or deformation
2. Replacement Indicators
Consider replacement when:
Thread wear compromises engagement
Visible cracks or deformation appear
Corrosion exceeds 30% of thread height
Torque values degrade significantly after multiple uses
3. Replacement Protocol
Attempt standard removal first
Apply penetrating oil for rusted nuts (wait 15-30 minutes)
For stubborn cases, use controlled heat application
As last resort, carefully cut nut while protecting bolt threads
Clean threads before installing new nut
Selection Guidelines
1. Material Selection
General purpose: Carbon steel Q235/45#
Corrosive environments: Stainless steel 304/316
High-temperature: Alloy steels 35CrMo/25Cr2MoV
Electrical conductivity: Brass H62/copper T2
2. Specification Matching
Ensure bolt/nut diameter compatibility
Select height based on material thickness
Choose heavy-duty versions for high loads
Consider coated variants for special environments
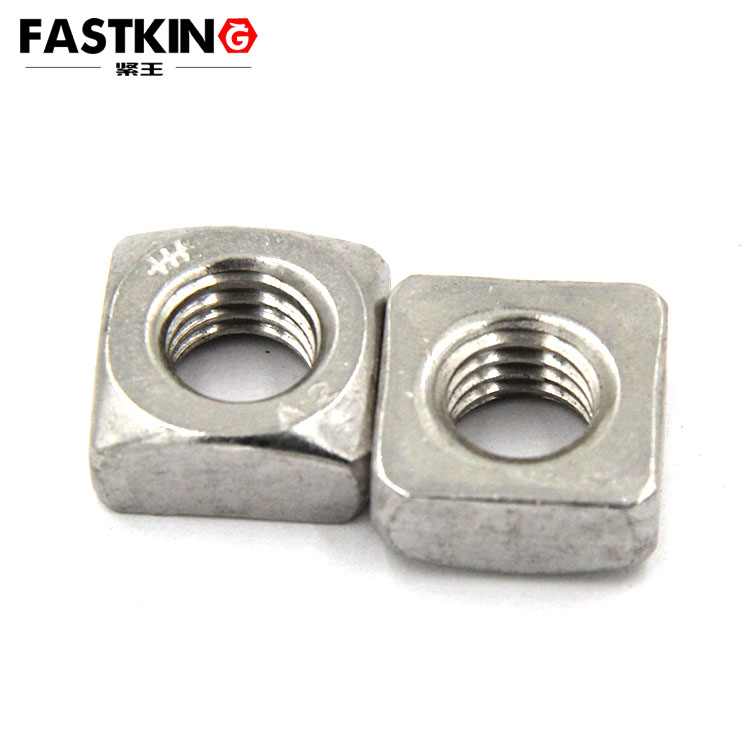
3. Economic Considerations
Bulk purchasing reduces costs
Avoid over-specification for application needs
Evaluate total lifecycle costs including maintenance
Conclusion
As a classic fastener, square nuts maintain irreplaceable roles in modern industry and daily applications. Proper understanding and application of square nut technology ensures reliable mechanical connections while improving efficiency and reducing maintenance costs. With advancements in materials and manufacturing, square nut performance continues to evolve, expanding their application potential. Engineering professionals should select and implement square nuts appropriately to maximize their unique advantages across various connection scenarios.