From a material perspective, hex nuts can be categorized into carbon steel, stainless steel, brass, nylon, and other types. Surface treatments include galvanizing, nickel plating, black oxide, Dacromet coating, and other processes. In terms of performance grades, common classifications include Grade 4, 6, 8, 10, and 12, with different strength levels. These varied specifications meet diverse environmental and usage requirements.
Correct Usage Methods of Hex Nuts
Tool Selection and Matching
Choosing appropriate tools is crucial when working with hex nuts. Common tools include:
Open-end wrenches: Suitable for routine fastening operations, but ensure the wrench size exactly matches the nut's across-flats dimension to prevent edge rounding
Box-end wrenches: More effective at preventing slippage than open-end wrenches, especially useful in space-constrained locations
Socket wrenches: Most efficient when used with ratchet handles, ideal for batch assembly operations
Adjustable wrenches: While versatile, recommended only for temporary use as prolonged usage may damage nuts
Torque wrenches: Essential for applications requiring precise fastening force, such as engines or precision equipment
Tool sizes must strictly correspond to nut specifications. For example, an M10 nut with a 16mm across-flats dimension requires a 16mm wrench.
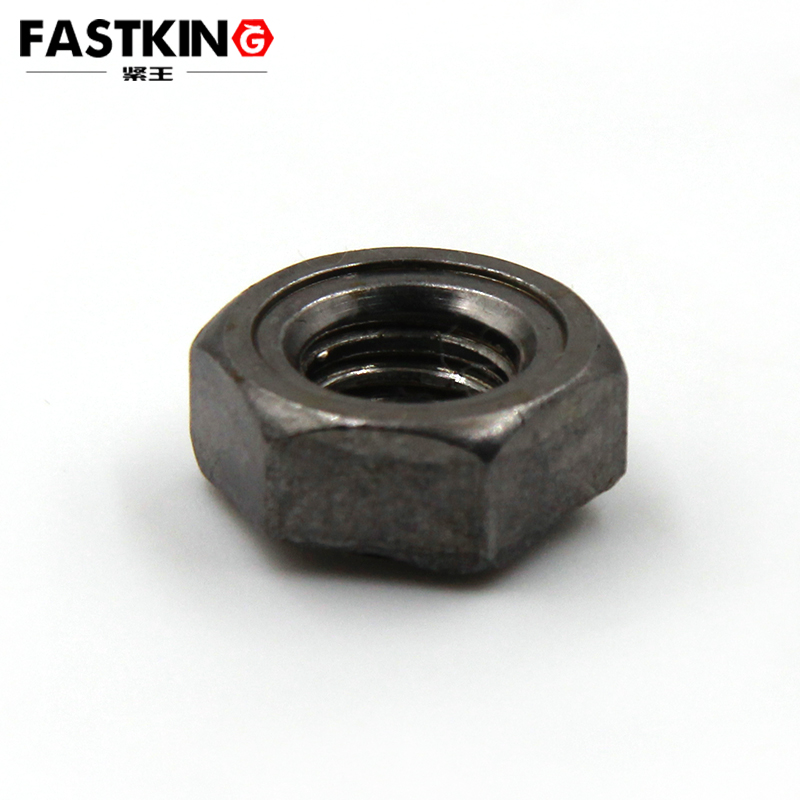
Installation Procedures and Techniques
Proper hex nut installation should follow these steps:
1. Clean threads: Remove debris and burrs from both bolt and nut threads using a wire brush to ensure smooth engagement
2. Hand-tighten first: Rotate the nut onto the bolt several turns by hand to confirm smooth threading before using tools
3. Symmetrical tightening: When multiple nuts are involved (e.g., flange connections), follow a crisscross pattern for even tightening
4. Progressive loading: Critical connections should reach final torque values in 2-3 stages, avoiding single-step tightening
5. Anti-loosening measures: Apply lock washers or thread-locking compounds in vibrating environments
Special attention: When pairing stainless steel nuts with carbon steel bolts, apply specialized lubricant to threads to prevent galling.
Torque Control Methods
Different hex nut sizes have corresponding recommended torque values. Over-tightening may cause:
- Thread deformation and damage
- Bolt stretching or fracture
- Connected component distortion
Insufficient torque may lead to:
- Loose connections
- Self-loosening under vibration
- Leakage at sealed joints
Reference torque values for common sizes:
- M6 nut: 8-10N·m
- M8 nut: 20-25N·m
- M10 nut: 40-50N·m
- M12 nut: 70-80N·m
Actual applications should consider material, surface treatment, lubrication, and other factors, with critical applications strictly following technical specifications.
Common Application Scenarios for Hex Nuts
Machinery Manufacturing Sector
Hex nuts are indispensable connecting elements in various mechanical equipment:
Machine tools: Fixing guides, protective covers, motor mounts
Conveying machinery: Assembling rollers, sprockets, and brackets
Agricultural machinery : Maintenance of tractors, harvesters
Automotive manufacturing: Engine, chassis, and body system bolt connections
For example, automotive wheel hub bearings typically use M12 or M14 high-strength hex nuts with cotter pins or lock washers to prevent loosening.
Construction and Steel Structure Engineering
Construction applications include:
Steel structure connections: Critical joints like H-beam columns and truss nodes
Curtain wall installation: Fixing mullions for glass or metal curtain walls
Pipe supports: Suspension systems for fire protection and ventilation pipes
Prefabricated components: Mechanical connections between concrete precast elements
Large steel structures typically use hot-dip galvanized high-strength hex nuts with matching high-strength bolts to ensure structural safety.
Electronics and Electrical Industry
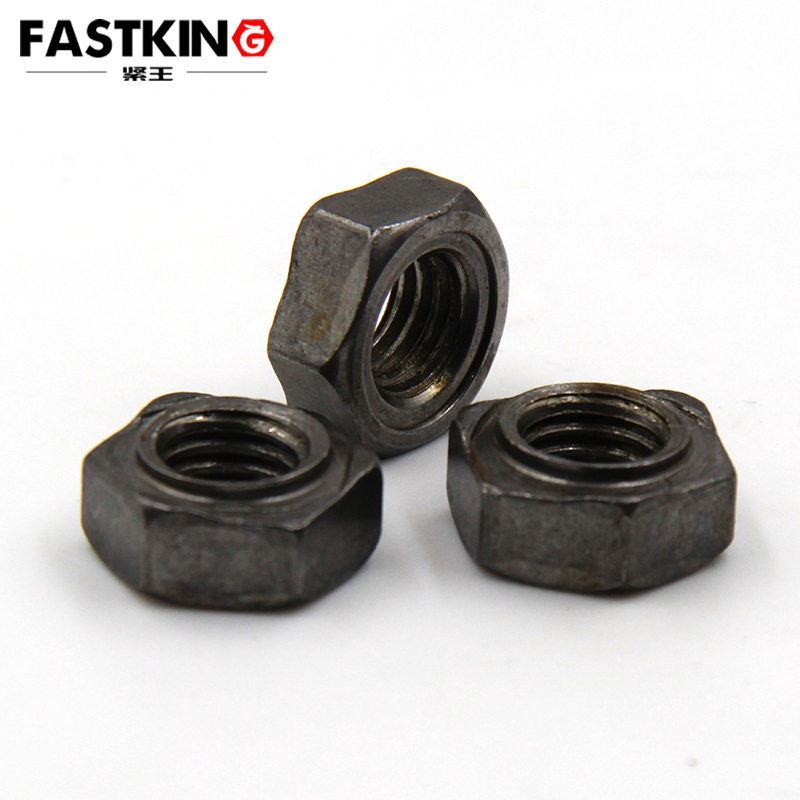
Though smaller in size, hex nuts are equally important:
Electrical enclosures: Assembly of distribution boxes and control cabinets
Heat sink installation: Mounting CPU coolers and power device heat sinks
Equipment racks: Installation of server racks and monitoring devices
PCB mounting: Mechanical support for high-power circuit boards
These applications often use M3-M6 small stainless steel hex nuts for corrosion resistance and aesthetic appeal.
Home Improvement and Repairs
Hex nuts are ubiquitous in daily life:
Furniture assembly: Connectors for panel furniture and hardware fixtures
Plumbing installation: Toilet and sink mounting
Appliance repairs: Disassembly of washing machines, air conditioners
Bicycle maintenance: Adjusting handlebars, seats, and racks
The home improvement sector typically uses standard galvanized hex nuts for cost-effectiveness and adequate strength.
Special Environment Applications
Special conditions require specific hex nuts:
High-temperature environments: Stainless steel or heat-resistant alloys
Corrosive environments: 316 stainless steel or copper-nickel alloys
Explosion-proof situations: Copper or non-sparking materials
Food/pharmaceutical: Hygienic 304/316 stainless steel nuts
For example, chemical plant pipeline flanges often use stainless steel hex nuts to prevent medium-induced corrosion failure.
Precautions for Hex Nut Usage
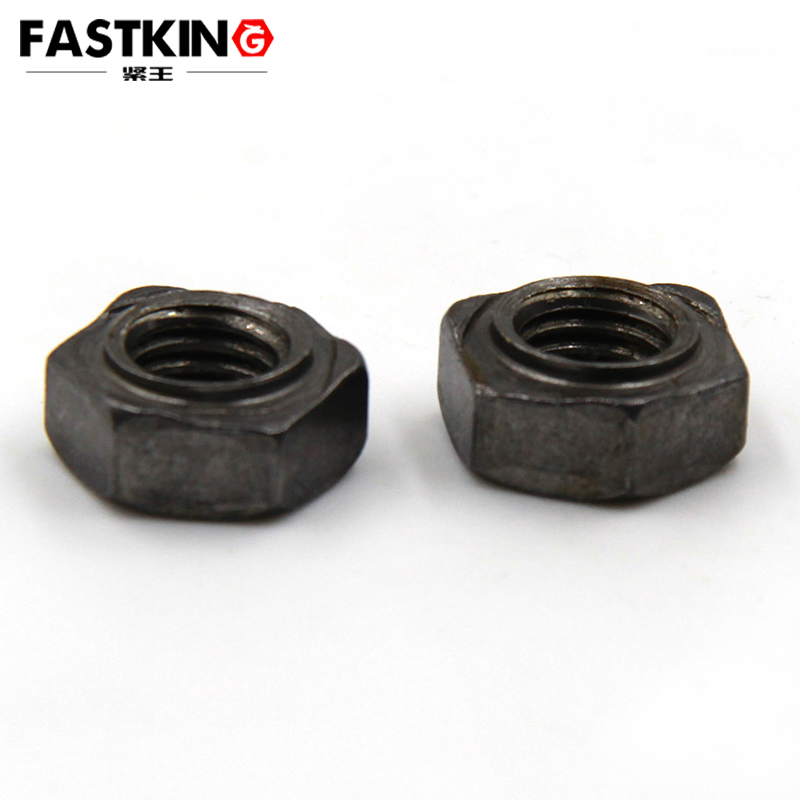
1. Avoid material mixing: Prevent galvanic corrosion (e.g., don't pair carbon steel bolts with stainless nuts)
2. Regular inspection: Check nut tightness periodically in vibrating environments
3. Proper storage: Organize nuts by specification and material to prevent confusion
4. Damaged nut disposal: Replace deformed or severely corroded nuts promptly
5. Safety measures: Wear gloves during tightening; use specialized tools in high-pressure environments
Though small, hex nuts play vital roles in various engineering projects and daily life. Mastering their proper usage and understanding application requirements not only improves work efficiency but also ensures connection safety and reliability. Both professionals and general users should value these seemingly simple yet crucial mechanical components.