Plain square weld nuts are common metal fasteners widely used in various metal structure connections. Compared to standard nuts, square weld nuts feature unique structural characteristics and installation methods that demonstrate significant advantages in specific applications.
Basic Structure and Features
Typically made from carbon steel or stainless steel with untreated surfaces (plain finish), these nuts feature:
Square base: Provides larger welding contact area for secure bonding
Central threaded hole: Standard thread specifications compatible with bolts
Uniform thickness: Ensures even heat distribution during welding
Precise dimensions: Guarantees compatibility with matching bolts
Materials and Specifications
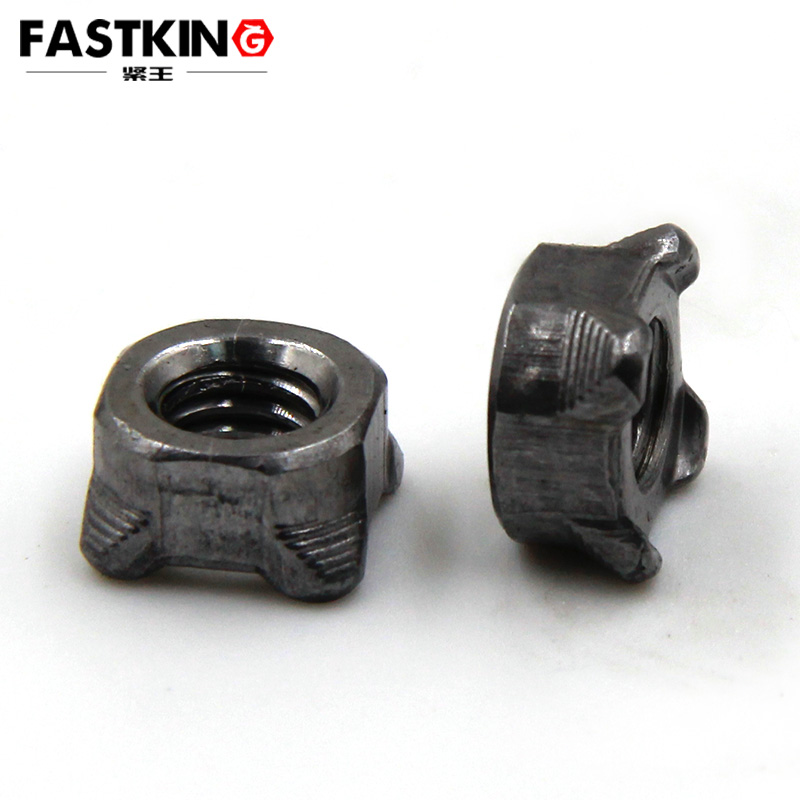
Common materials include:
Q235 carbon steel: Cost-effective with moderate strength
45# steel: Higher strength for heavy-duty applications
Stainless steel 304/316: Superior corrosion resistance for special environments
Standard sizes follow thread dimensions (M3, M4, M5, M6, M8, etc.), selectable according to project requirements.
Usage Instructions for Plain Square Weld Nuts
Proper installation is crucial for ensuring connection strength and safety. Below are detailed procedures and precautions.
Preparation
Before installation:
Surface cleaning: Remove oil, rust, and contaminants from welding areas
Nut selection: Choose appropriate specifications based on material thickness and load requirements
Equipment preparation: Prepare suitable welding tools and protective gear
Position marking: Accurately mark installation positions on base materials
Welding Method Selection
Available welding techniques:
Spot Welding (Most Common)
Procedure:
Position nut at designated location
Clamp with spot welder electrodes
Apply current to create instant weld points
Typically requires four spot welds at each corner
Arc Welding
For thicker materials:
Weld along nut edges using electrodes/wire
Maintain consistent weld seams
Control heat input to prevent deformation
Projection Welding
Professional method requiring special equipment:
Nuts feature pre-formed projections
Projections melt first during welding
Delivers high-quality welds with minimal distortion
Welding Procedure
Positioning: Secure nut precisely using clamps/jigs
Parameter setting: Adjust current/time based on material
Welding execution: Perform according to selected method
Quality inspection: Check for solid welds without defects
Slag removal: Clean oxidation residues and spatter
Post-Welding Treatment
Thread protection: Clear any slag from threads using taps
Rust prevention: Apply anti-rust oil to untreated surfaces
Strength testing: Conduct pull tests for critical connections
Application Scenarios
Square weld nuts are extensively used across industries due to their structural advantages.
Automotive Manufacturing
Essential for:
Body structures (doors, hoods, trunks)
Chassis components (suspension, exhaust systems)
Interior fittings (dashboards, seats)
Advantages:
No backside access required
High vibration resistance
Suitable for automated production
Machinery Equipment
Common applications:
Frame assemblies
Removable guard panels
Pipe mounting brackets
Ideal for:
Enclosed structures
Frequently disassembled parts
Space-constrained locations
Electrical/Electronics Industry
Used in:
Control panel installations
Grounding terminals
Internal component assembly
Benefits:
Stable threaded connections
Flush surface finish
Simplified assembly processes
Architectural Steelwork
Construction applications:
- Curtain wall systems
- Beam-column joints
- Decorative elements
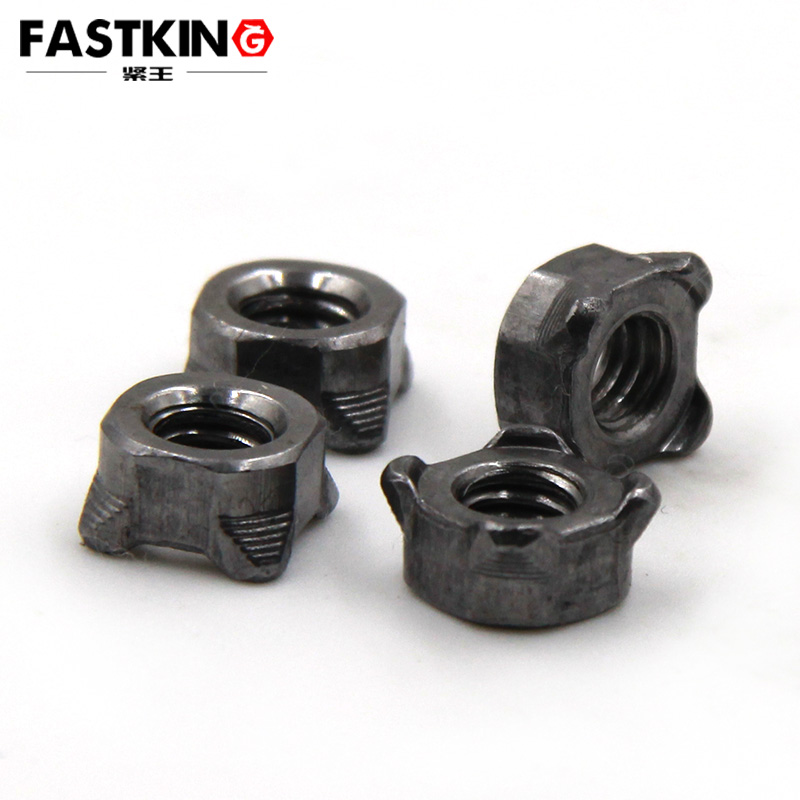
Features:
- High load capacity
- Flexible positioning
- Aesthetic concealed fastening
Furniture Production
Modern metal furniture uses:
- Office furniture frames
- Display shelving
- Outdoor furniture structures
Advantages:
- Smooth surface profile
- Durable connections
- Mass-production suitability
Usage Precautions
Selection Guidelines
Material compatibility with base metal
Thickness ratio (nut ≥1.2× base thickness)
Correct thread-bolt matching
Welding Quality Control
Avoid excessive heat input
Distribute weld points evenly
Consider full-perimeter welding for critical joints
Environmental Considerations
Use stainless steel in corrosive environments
Avoid exceeding temperature limits
Add anti-loosening measures for vibrating parts
Maintenance
Regular weld inspections
Thread lubrication for storage
Timely replacement of damaged parts
Troubleshooting Guide
Weak Welds
Causes:
- Improper welding parameters
- Poor surface preparation
- Misalignment
Solutions:
- Adjust current/time settings
- Re-clean surfaces
- Use positioning fixtures
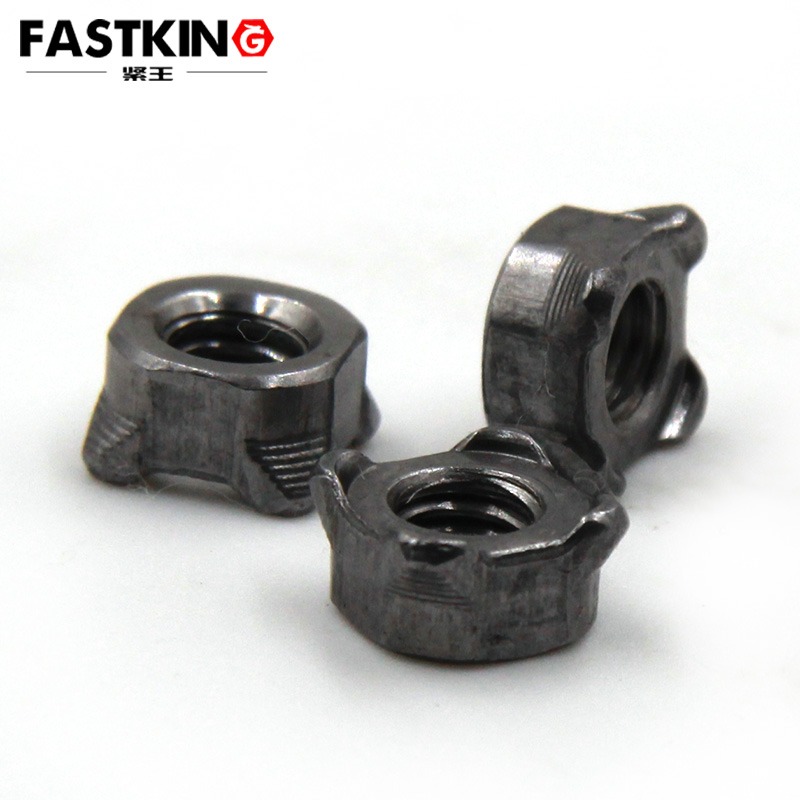
Thread Damage
Causes:
- Weld spatter contamination
- Bolt mismatch
- Improper disassembly
Conclusion
Plain square weld nuts serve as economical and practical fastening solutions across industries. Proper selection and installation not only enhance production efficiency but also ensure connection reliability. Understanding their usage methods and applications enables engineers to implement this solution effectively.
With advancing manufacturing technologies, weld nut materials, processes, and applications continue expanding. Future developments will yield higher-strength, more corrosion-resistant, and easier-to-install variants to meet evolving industrial demands.