Introduction
In modern industrial manufacturing, rivets, as a classic mechanical fastener, are widely used in aerospace, automotive manufacturing, electronics, and other fields due to their high reliability and low cost. Among them, the countersunk vertical stripe rivet (Countersunk Vertical Stripe Rivet), as a special type of rivet, has gradually become a preferred solution in precision assembly due to its unique structural design and performance advantages. This article will analyze its structural characteristics, usage principles, and typical application scenarios to reveal its value in practical engineering.
I. Structural Characteristics of Countersunk Vertical Stripe Rivets
Countersunk Head Design
The rivet head is conical with a 120° or 90° angle, allowing it to sit flush with the material surface after installation. This avoids interference with aerodynamic performance or aesthetics, making it indispensable in applications such as aircraft skins and high-speed train exteriors where surface smoothness is critical.
Vertical Stripe Surface Treatment
The shank surface is machined with longitudinal grooves, typically 0.1-0.3mm deep. These stripes create a mechanical interlocking effect with the hole wall during riveting, increasing shear strength by 15%-20% compared to smooth rivets.
Miniaturized Specifications
Typical specifications include diameters of 2-5mm and lengths of 6-15mm, making them suitable for precision connections in thin materials (0.5-3mm thickness). They are particularly ideal for confined spaces in electronic devices.
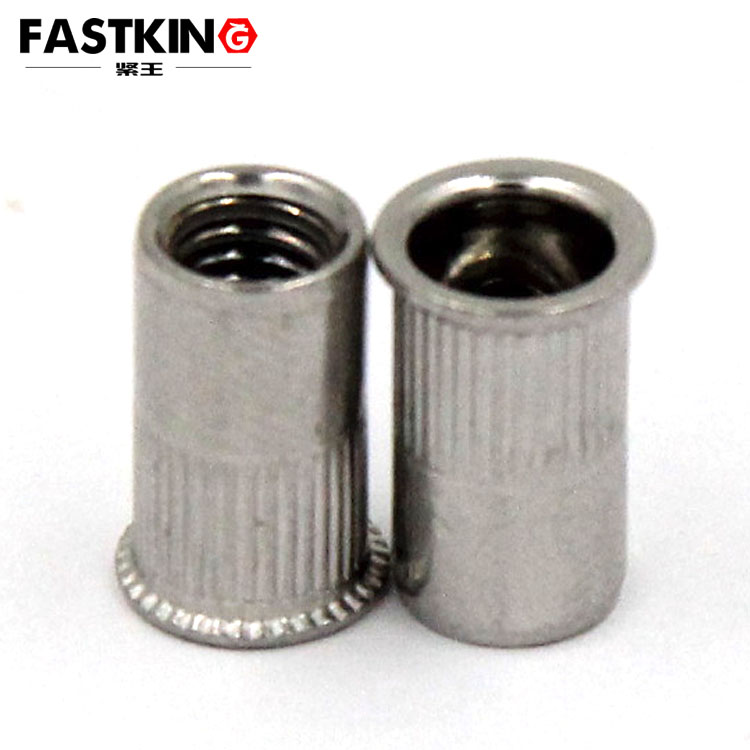
II. Usage Principles and Technical Advantages
The connection process of countersunk vertical stripe rivets follows the principle of plastic deformation and can be divided into three stages:
Pre-tightening Stage
After inserting the rivet into the pre-drilled hole, axial pressure is applied using specialized tools (e.g., pneumatic rivet guns). The friction coefficient between the vertical stripes and the hole wall is 30% higher than that of ordinary rivets, effectively preventing unintended rotation during installation and ensuring positioning accuracy.
Deformation Stage
The tail undergoes plastic expansion under pressure, with the vertical stripe structure guiding material flow along the axis to form a symmetrical drum-shaped tail. Experimental data shows that this design improves load distribution uniformity by 40%, significantly reducing stress concentration risks.
Locking Stage
After complete riveting, the countersunk head fits flush with the base material surface, and the vertical stripes and deformed tail together form a dual-locking mechanism:
Mechanical interlocking between the stripes and hole wall provides static shear resistance.
The expanded tail creates dynamic pull-out resistance.
Compared to traditional rivets, their vibration fatigue life can be extended by 3-5 times, making them particularly outstanding in high-frequency vibration environments such as vehicle electronics and drone structures.
III. Analysis of Typical Application Scenarios
Aerospace Industry
Application Areas: Aircraft skin splicing, cabin equipment bracket fixation
Technical Requirements: Compliance with MIL-SPEC-5021 standards, use of 7075 aluminum alloy or titanium alloy materials
Case Study: The Boeing 787 aircraft wing leading edge uses over 200,000 such rivets per plane, achieving a 12% weight reduction.
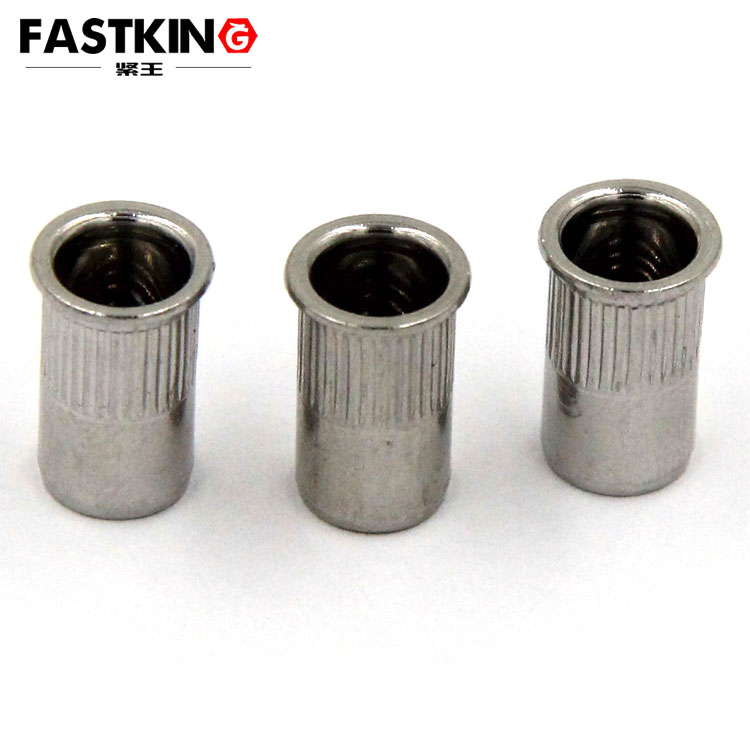
New Energy Vehicle Manufacturing
Application Scenarios: Battery pack casing sealing, motor bracket connections
Advantages: IP67 waterproof certification, resistance to electrolyte corrosion for up to 500 hours without failure
Consumer Electronics
Typical Applications: Laptop hinge structures, smartwatch band connections
Innovative Practice: The 2021 Apple MacBook Pro首次 used 0.8mm ultra-miniature vertical stripe rivets in the hinge, achieving 0.01mm-level assembly precision.
Medical Device Industry
Special Requirements: Compliance with ISO 13485 medical material standards, surface passivation treatment
Application Example: Da Vinci surgical robot joint connections, enduring 20,000 cycles per day
IV. Technological Development Trends
Material Innovation
The application of nano-composite coatings (e.g., diamond-like carbon coatings) reduces the rivet friction coefficient by 50% and installation energy consumption by 30%.
Intelligent Assembly
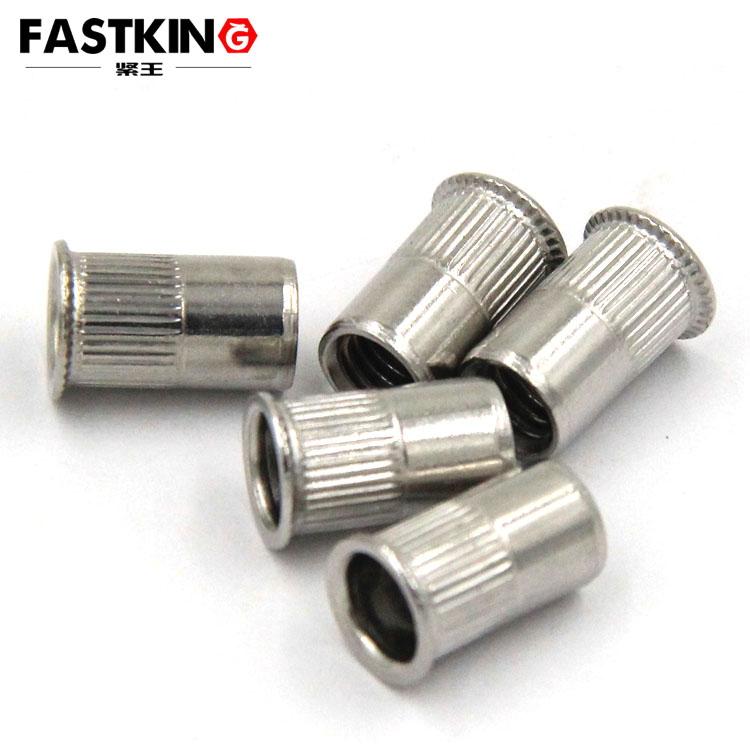
Smart rivets equipped with RFID chips are being piloted, enabling real-time monitoring of connection stress states and providing data for predictive maintenance.
Eco-friendly Processes
The adoption of cold riveting technology eliminates the need for heating during installation, reducing carbon emissions and aligning with ISO 14064 environmental management standards.
Conclusion
The engineering value of countersunk vertical stripe rivets lies in their perfect integration of fundamental physical principles and precision manufacturing technologies. From micron-level stripe machining to ton-level pressure control, every technical detail redefines the reliability boundaries of mechanical connections. With the deepening of Industry 4.0, this seemingly simple fastener is gaining new vitality through intelligent and green transformations, continuing to provide robust connection solutions for high-end equipment manufacturing.