I. Working Principle of 120-Degree Countersunk Rivets
The working principle of the 120-degree countersunk rivet is based on its unique geometric structure. When the rivet is installed, its 120-degree conical head fully embeds into a pre-machined conical hole, creating a flush surface. This design prevents any protrusion at the connection point, making it particularly suitable for applications requiring high surface smoothness.
During installation, the rivet's shank undergoes plastic deformation under the pressure of specialized tools, forming a secure mechanical connection. The 120-degree angle ensures a perfect fit between the rivet head and the surface of the connected components, guaranteeing both reliability and an aesthetically pleasing finish.
Compared to traditional 90-degree countersunk rivets, the 120-degree design offers superior stress distribution. The larger contact angle allows for more even load transfer to the connected components, reducing stress concentration and enhancing the fatigue strength of the connection.
II. Typical Applications of 120-Degree Countersunk Rivets
In the aerospace industry, 120-degree countersunk rivets are widely used. Aircraft skin connections require extremely high surface smoothness to reduce air resistance while ensuring connection reliability. The 120-degree countersunk rivet perfectly meets these requirements, making it an indispensable fastener in aircraft manufacturing.
The automotive manufacturing industry also extensively uses these rivets. In applications such as body panel connections and interior component fastening, 120-degree countersunk rivets provide both strong connections and a visually appealing finish. Their use is particularly prevalent in the production of new energy vehicles.
In the field of precision instrument manufacturing, 120-degree countersunk rivets are equally important. Instruments and equipment often require frequent disassembly and maintenance, and the flush connection surface provided by these rivets does not interfere with the installation and operation of other components while ensuring connection reliability.
III. Technical Advantages of 120-Degree Countersunk Rivets
The most notable advantage of 120-degree countersunk rivets is their excellent surface smoothness. This characteristic not only improves the appearance of products but, more importantly, significantly reduces air resistance in applications requiring good aerodynamic performance, such as the external surfaces of aircraft and high-speed trains.
In terms of structural strength, the 120-degree design offers better load distribution. The larger contact area ensures more uniform stress distribution, reducing local stress concentration and enhancing the fatigue life of the connection. This feature is particularly important in applications subjected to vibrational loads.
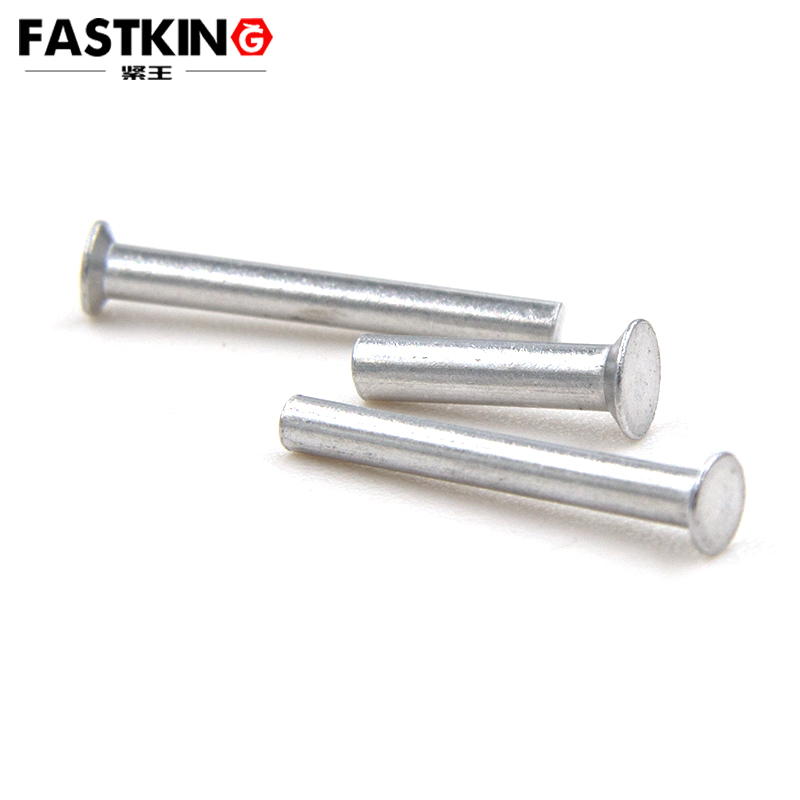
From an aerodynamic optimization perspective, the flush surface of 120-degree countersunk rivets effectively reduces turbulence generation and lowers air resistance. This characteristic is of great value in the manufacturing of aerospace and high-speed transportation vehicles, significantly improving overall product performance.
The design of 120-degree countersunk rivets reflects the modern industrial manufacturing's pursuit of precision and performance. As manufacturing technology continues to advance, these fasteners will play an increasingly important role in various fields, providing more reliable and optimized connection solutions for industrial products. In the future, with the application of new materials and processes, the performance of 120-degree countersunk rivets will be further enhanced, bringing more possibilities to industrial manufacturing.